Introducción
La producción y el consumo de residuos plásticos está aumentando a un ritmo alarmante, con el incremento de la población humana, el rápido crecimiento económico, la continua urbanización y los cambios en el estilo de vida. Además, la corta vida del plástico acelera la producción de residuos plásticos a diario. La producción mundial de plástico se estimó en unos 300 millones de toneladas al año y aumenta continuamente cada año (Miandad et al., 2016a; Ratnasari et al., 2017). Los plásticos están hechos de hidrocarburos petroquímicos con aditivos como retardantes de llama, estabilizadores y oxidantes que dificultan su biodegradación (Ma et al., 2017). El reciclaje de residuos plásticos se lleva a cabo de diferentes maneras, pero en la mayoría de los países en desarrollo, la eliminación a cielo abierto o en vertederos es una práctica común para la gestión de residuos plásticos (Gandidi et al., 2018). La eliminación de residuos plásticos en vertederos proporciona un hábitat para insectos y roedores, que pueden causar diferentes tipos de enfermedades (Alexandra, 2012). Además, el coste del transporte, la mano de obra y el mantenimiento pueden aumentar el coste de los proyectos de reciclaje (Gandidi et al., 2018). Además, debido a la rápida urbanización, el terreno disponible para los vertederos, especialmente en las ciudades, se está reduciendo. La pirólisis es una técnica común utilizada para convertir los residuos plásticos en energía, en forma de combustibles sólidos, líquidos y gaseosos.
La pirólisis es la degradación térmica de los residuos plásticos a diferentes temperaturas (300-900°C), en ausencia de oxígeno, para producir aceite líquido (Rehan et al., 2017). Se utilizan diferentes tipos de catalizadores para mejorar el proceso de pirólisis de los residuos plásticos en general y para mejorar la eficiencia del proceso. Los catalizadores tienen un papel muy crítico en la promoción de la eficiencia del proceso, dirigiéndose a la reacción específica y reduciendo la temperatura y el tiempo del proceso (Serrano et al., 2012; Ratnasari et al., 2017). Se ha empleado una amplia gama de catalizadores en los procesos de pirólisis de plásticos, pero los catalizadores más utilizados son ZSM-5, zeolita, Y-zeolita, FCC y MCM-41 (Ratnasari et al., 2017). La reacción catalítica durante la pirólisis de residuos plásticos en catalizadores ácidos sólidos puede incluir reacciones de craqueo, oligomerización, ciclación, aromatización e isomerización (Serrano et al., 2012).
Varios estudios reportaron el uso de catalizadores microporosos y mesoporosos para la conversión de residuos plásticos en aceite líquido y carbón. Uemichi et al. (1998) llevaron a cabo la pirólisis catalítica de polietileno (PE) con catalizadores HZSM-5. El uso de HZSM-5 aumentó la producción de aceite líquido con la composición de compuestos aromáticos e isoalcanos. Gaca et al. (2008) llevaron a cabo la pirólisis de residuos plásticos con MCM-41 modificado y HZSM-5 e informaron que el uso de HZSM-5 produjo hidrocarburos más ligeros (C3-C4) con un máximo de compuestos aromáticos. Lin et al. (2004) utilizaron diferentes tipos de catalizadores e informaron que incluso la mezcla de HZSM-5 con SiO2-Al2O3 mesoporoso o MCM-41 condujo a la máxima producción de aceite líquido con una mínima producción de gas. Aguado et al. (1997) informaron de la producción de compuestos aromáticos y alifáticos a partir de la pirólisis catalítica de PE con HZSM-5, mientras que el uso de MCM-41 mesoporoso disminuyó los compuestos aromáticos producidos debido a su baja actividad catalítica ácida. El uso de catalizadores sintéticos mejoró el proceso global de pirólisis y la calidad del aceite líquido producido. Sin embargo, el uso de catalizadores sintéticos aumentó el coste del proceso de pirólisis.
Los catalizadores NZ pueden utilizarse para superar los retos económicos de la pirólisis catalítica que conlleva el uso de catalizadores caros. En los últimos años, el NZ ha ganado mucha atención por sus potenciales aplicaciones medioambientales. Naturalmente, la NZ se encuentra en Japón, Estados Unidos, Cuba, Indonesia, Hungría, Italia y el Reino de Arabia Saudí (KSA) (Sriningsih et al., 2014; Nizami et al., 2016). El yacimiento de NZ en KSA se encuentra principalmente en Harrat Shama y Jabbal Shama y contiene principalmente minerales de mordenita con alta estabilidad térmica, lo que lo hace adecuado como catalizador en la pirólisis de residuos plásticos. Sriningsih et al. (2014) modificaron NZ de Sukabumi, Indonesia, depositando metales de transición como Ni, Co y Mo y llevaron a cabo la pirólisis de polietileno de baja densidad (LDPE). Gandidi et al. (2018) utilizaron NZ de Lampung, Indonesia, para la pirólisis catalítica de residuos sólidos municipales.
Este es el primer estudio que investiga el efecto de la zeolita natural saudí modificada, sobre la calidad y el rendimiento del producto de la pirólisis catalítica de residuos plásticos. El catalizador de zeolita natural saudí se modificó mediante una nueva activación térmica (TA-NZ) a 550°C y una activación ácida (AA-NZ) con HNO3 para mejorar sus propiedades catalíticas. Se llevó a cabo por primera vez la pirólisis catalítica de diferentes tipos de residuos plásticos (PS, PE, PP y PET) como simples o mezclados en diferentes proporciones, en presencia de catalizadores de zeolita natural (NZ) modificados en un reactor de pirólisis a pequeña escala piloto. Se estudió la calidad y el rendimiento de los productos de pirólisis, como el aceite líquido, el gas y el carbón vegetal. La composición química del aceite líquido se analizó mediante GC-MS. Además, se ha discutido el potencial y los retos de las biorrefinerías basadas en la pirólisis.
Materiales y métodos
Preparación de la materia prima y puesta en marcha del reactor
Los residuos plásticos utilizados como materia prima en el proceso de pirólisis catalítica se recogieron en Jeddah e incluían bolsas de supermercado, vasos y platos de zumo desechables y botellas de agua potable, que consisten en plásticos de polietileno (PE), polipropileno (PP), poliestireno (PS) y tereftalato de polietileno (PET), respectivamente. La selección de estos materiales plásticos se basó en el hecho de que son la principal fuente de residuos plásticos producidos en KSA. Para obtener una mezcla homogénea, todas las muestras de residuos se trituraron en trozos más pequeños de unos 2 cm2. La pirólisis catalítica se llevó a cabo utilizando un individuo o una mezcla de estos residuos plásticos en diferentes proporciones (Tabla 1). Se utilizaron 1000 g de materia prima, con 100 g de catalizador en cada experimento. La zeolita natural saudí (NZ), recogida en Harrat-Shama, situada en el noroeste de la ciudad de Jeddah, KSA (Nizami et al., 2016), se modificó mediante tratamiento térmico y ácido y se utilizó en estos experimentos de pirólisis catalítica. La NZ fue triturada hasta convertirla en polvo (<100 nm) en una máquina de molienda de bolas (Retsch MM 480) durante 3 h utilizando 20 Hz/seg, antes de la modificación y su uso en la pirólisis. Para la activación térmica (AT), el NZ se calentó en un horno de mufla a 550°C durante 5 h, mientras que para la activación ácida (AA) el NZ se sumergió en una solución 0,1 M de ácido nítrico (HNO3) durante 48 h y se agitó continuamente utilizando un agitador digital IKA HS 501 con 50 rpm. Después, la muestra se lavó con agua desionizada hasta obtener un pH normal.
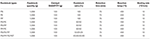
Tabla 1. Esquema experimental.
Los experimentos se llevaron a cabo en un pequeño reactor de pirólisis a escala piloto a 450°C, utilizando una velocidad de calentamiento de 10°C/min y un tiempo de reacción de 75 min (Figura 1). El rendimiento obtenido de cada producto de pirólisis se calculó en base al peso, tras la finalización de cada experimento. La caracterización del aceite líquido producido se llevó a cabo para investigar el efecto de la composición de la materia prima en la calidad del aceite líquido producido en presencia de la NZ modificada. Se llevó a cabo el TGA en la materia prima para obtener las condiciones óptimas del proceso, como la temperatura y el tiempo de reacción (75 min) en condiciones controladas. En el TGA, se tomaron 10 μg de cada tipo de residuo plástico y se calentaron con una tasa de 10°C de 25 a 900°C bajo un flujo continuo de nitrógeno (50 ml/min). Los autores de este estudio han publicado recientemente un trabajo sobre el efecto de la composición de la materia prima y los catalizadores de zeolita natural y sintética sin modificación del catalizador en diferentes tipos de residuos plásticos (Miandad et al., 2017b; Rehan et al., 2017).
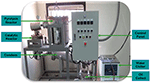
Figura 1. Reactor de pirólisis a pequeña escala piloto (Miandad et al., 2016b).
Sistema experimental
El reactor a pequeña escala piloto tiene la capacidad de ser utilizado como pirólisis térmica y catalítica, utilizando diferentes materias primas como materiales plásticos y biomasa (Figura 1). En este estudio, se añadieron catalizadores NZ modificados en el reactor con la materia prima. El reactor de pirólisis puede contener hasta 20 L de materia prima y la temperatura máxima de trabajo segura de hasta 600°C puede alcanzarse con las tasas de calentamiento deseadas. Los parámetros detallados del reactor de pirólisis se publicaron anteriormente (Miandad et al., 2016b, 2017b). Al aumentar la temperatura por encima de ciertos valores, los residuos de plástico (polímeros orgánicos) se convierten en monómeros que se transfieren al condensador, donde estos vapores se condensan en aceite líquido. Se utilizó un sistema de condensación continua con un baño de agua y el refrigerante ACDelco Classic para garantizar que la temperatura de condensación se mantuviera por debajo de los 10°C, y para asegurar la máxima condensación del vapor en aceite líquido. El aceite líquido producido se recogió del tanque de recogida de aceite, y se llevó a cabo una caracterización adicional para descubrir su composición química y sus características para otras aplicaciones potenciales.
Métodos analíticos
El aceite de pirólisis se caracterizó utilizando diferentes técnicas como la cromatografía de gases acoplada a la espectrofotometría de masas (GC-MS), la espectroscopia de infrarrojos por transformada de Fourier (FT-IR),
Calorímetro de Bomba y TGA (Mettler Toledo TGA/SDTA851) adoptando los métodos estándar ASTM. Los grupos funcionales en el aceite de pirólisis se analizaron mediante un instrumento FT-IR, Perkin Elmer’s, Reino Unido. El análisis FT-IR se realizó utilizando un mínimo de 32 escaneos con una media de 4 señales IR cm-1 dentro del rango de frecuencias de 500-4.000 cm-1.
La composición química del aceite se estudió utilizando un GC-MS (Shimadzu QP-Plus 2010) con detector FI. Se utilizó una columna GC capilar de 30 m de longitud y 0,25 mm de ancho recubierta con una película de 0,25 μm de espesor de fenilmetilpolisiloxano al 5% (HP-5). La estufa se ajustó a 50 °C durante 2 min y luego se aumentó hasta 290 °C utilizando una velocidad de calentamiento de 5 °C/min. La temperatura de la fuente de iones y de la línea de transferencia se mantuvo a 230 y 300°C y se aplicó la inyección sin división a 290°C. Se utilizó la biblioteca de datos espectrales de masas NIST08s para identificar los picos cromatográficos, y se evaluaron los porcentajes de los picos por su área de pico del cromatograma iónico total (TIC). Los valores caloríficos elevados (HHV) del aceite líquido producido, obtenido a partir de diferentes tipos de residuos plásticos, se midieron siguiendo el método estándar ASTM D 240 con un Calorímetro de Bomba (Calorímetro Parr 6200), mientras que la producción de gas se estimó utilizando la fórmula estándar de balance de masas, considerando la diferencia de pesos del aceite líquido y del carbón.
Resultados y discusión
Análisis TGA de la materia prima
El TGA se llevó a cabo para cada tipo de residuo plástico de forma individual para determinar la temperatura óptima para la degradación térmica. Todos los tipos de residuos plásticos muestran un comportamiento de degradación similar con la rápida pérdida de peso de los hidrocarburos dentro del estrecho rango de temperatura (150-250°C) (Figura 2). La máxima degradación para cada tipo de residuo plástico se alcanzó dentro de los 420-490°C. El PS y el PP mostraron una descomposición de un solo paso, mientras que el PE y el PET mostraron una descomposición de dos pasos en condiciones controladas. La descomposición en un solo paso corresponde a la presencia de un enlace carbono-carbono que promueve el mecanismo de escisión aleatoria con el aumento de la temperatura (Kim et al., 2006). La degradación del PP comenzó a una temperatura muy baja (240°C) en comparación con otras materias primas. La mitad del carbono presente en la cadena del PP consiste en carbono terciario, lo que promueve la formación de carbocationes durante su proceso de degradación térmica (Jung et al., 2010). Esta es probablemente la razón por la que se consigue la máxima degradación del PP a una temperatura más baja. La degradación inicial del PS comenzó a 330°C y la máxima degradación se alcanzó a 470°C. El PS tiene una estructura cíclica, y su degradación en condiciones térmicas implica tanto la escisión de la cadena aleatoria como de la cadena final, lo que potencia su proceso de degradación (Demirbas, 2004; Lee, 2012).
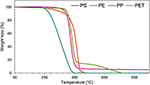
Figura 2. Análisis termogravimétrico (TGA) de residuos plásticos de PS, PE, PP y PET.
El PE y el PET mostraron un proceso de descomposición en dos etapas; la degradación inicial comenzó a temperaturas más bajas, seguida de la otra etapa de degradación a una temperatura más alta. La degradación inicial del PE comenzó a 270°C y se propagó lenta pero gradualmente hasta que la temperatura alcanzó los 385°C. Después de esa temperatura, se observó una degradación brusca, y se alcanzó el 95% de degradación con un aumento adicional de unos 100°C. En el caso del plástico PET se observó un patrón de degradación similar en dos etapas y la degradación inicial comenzó a 400°C con una fuerte disminución de la pérdida de peso. Sin embargo, la segunda degradación comenzó a una temperatura ligeramente superior (550°C). La degradación inicial del PE y el PET puede deberse a la presencia de algunas impurezas volátiles como el relleno aditivo utilizado durante la síntesis del plástico (Dimitrov et al., 2013).
Varios investigadores han informado de que la degradación del PE y el PET requiere temperaturas más altas en comparación con otros plásticos (Dimitrov et al., 2013; Rizzarelli et al., 2016). Lee (2012) informó de que el PE tiene una estructura ramificada de cadena larga y que su degradación se produce a través de la escisión aleatoria de la cadena, por lo que requiere una temperatura más alta, mientras que la degradación del PET sigue la escisión aleatoria del enlace de éster que da lugar a la formación de oligómeros (Dziecioł y Trzeszczynski, 2000; Lecomte y Liggat, 2006). La degradación inicial del PET se debió quizás a la presencia de algunas impurezas volátiles como el dietilenglicol (Dimitrov et al., 2013). La literatura informa de que la presencia de estas impurezas volátiles promueve aún más el proceso de degradación de los polímeros (McNeill y Bounekhel, 1991; Dziecioł y Trzeszczynski, 2000). La diferencia en las curvas TGA de varios tipos de plásticos podría deberse a su estructura mesoporosa (Chandrasekaran et al., 2015). Además, López et al. (2011) informaron de que el uso de catalizadores disminuye la temperatura del proceso. Por lo tanto, 450°C podría tomarse como la temperatura óptima, en presencia de NZ activado, para la pirólisis catalítica de los residuos plásticos mencionados.
Efecto de la materia prima y los catalizadores en el rendimiento de los productos de pirólisis
Se examinó el efecto de la activación térmica y ácida de NZ en el rendimiento de los productos del proceso de pirólisis (Figura 3). La pirólisis catalítica de plástico PS individual utilizando catalizadores TA-NZ y AA-NZ mostró los mayores rendimientos de aceite líquido del 70 y 60%, respectivamente, en comparación con todos los demás tipos de residuos plásticos individuales y combinados estudiados. El alto rendimiento de aceite líquido a partir de la pirólisis catalítica del PS también se informó en varios otros estudios (Siddiqui y Redhwi, 2009; Lee, 2012; Rehan et al., 2017). Siddiqui y Redhwi (2009) informaron de que el PS tiene una estructura cíclica, lo que conduce a un alto rendimiento de aceite líquido a partir de la pirólisis catalítica. Lee (2012) informó de que la degradación del PS se producía a través de escisiones tanto de la cadena aleatoria como de la cadena final, lo que conduce a la producción de la estructura de anillo de benceno estable, que mejora el craqueo posterior y puede aumentar la producción de aceite líquido. Además, en presencia de catalizadores ácidos, la degradación de la PS siguió un mecanismo de carbenio, que además sufrió hidrogenación (transferencia de hidrógeno inter/intramolecular) y β-escisión (Serrano et al., 2000). Además, la degradación del PS se produjo a una temperatura más baja, en comparación con otros plásticos como el PE, debido a su estructura cíclica (Wu et al., 2014). Por otro lado, la pirólisis catalítica del PS produjo una mayor cantidad de carbón (24,6%) con el catalizador AA-NZ que con el catalizador TA-NZ (15,8%). Ma et al. (2017) también informaron de la alta producción de carbón a partir de la pirólisis catalítica de PS con un catalizador de zeolita ácida (Hβ). Las altas cifras de producción de carbón se debieron a la alta acidez del catalizador, que favorece la producción de carbón a través de intensas reacciones de reticulación secundaria (Serrano et al., 2000).
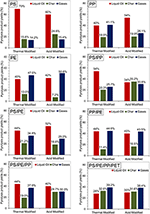
Figura 3. Efecto de TA-NZ y AA-NZ en el rendimiento del producto de pirólisis.
La pirólisis catalítica del PP produjo mayor aceite líquido (54%) con el catalizador AA-NZ que con el catalizador TA-NZ (40%) (Figura 3). Por otro lado, el catalizador TA-NZ produjo grandes cantidades de gas (41,1%), lo que puede deberse a la menor actividad catalítica del catalizador TA-NZ. Según Kim et al. (2002) los catalizadores con baja acidez y áreas superficiales BET con estructuras microporosas, favorecen la degradación inicial del PP lo que puede llevar a la máxima producción de gases. Obali et al. (2012) llevaron a cabo la pirólisis de PP con un catalizador cargado de alúmina e informaron de la máxima producción de gas. Además, la formación de carbocationes durante la degradación del PP, debido a la presencia de carbono terciario en su cadena de carbono, también puede favorecer la producción de gas (Jung et al., 2010). Syamsiro et al. (2014) también informaron de que la pirólisis catalítica de PP y PS con un catalizador de zeolita natural activado con ácido (HCL) produjo más gases que el proceso con un catalizador de zeolita natural activado térmicamente, debido a su alta acidez y a su área superficial BET.
La pirólisis catalítica de PE con catalizadores TA-NZ y AA-NZ produjo cantidades similares de aceite líquido (40 y 42%). Sin embargo, las mayores cantidades de gases (50,8 y 47,0%) se produjeron a partir del PE, utilizando AA-NZ y TA-NZ respectivamente, en comparación con todos los demás tipos de plástico estudiados. La producción de carbón fue la más baja en este caso, 7,2 y 13,0% con AA-NZ y TA-NZ, respectivamente. Varios estudios también informaron de la menor producción de carbón a partir de la pirólisis catalítica de PE (Xue et al., 2017). López et al. (2011) informaron que los catalizadores con alta acidez mejoraron el craqueo de los polímeros durante la pirólisis catalítica. El aumento del craqueo, en presencia de un catalizador de alta acidez, promueve la producción de gases (Miandad et al., 2016b, 2017a). Zeaiter (2014) llevó a cabo la pirólisis catalítica de PE con zeolita HBeta y reportó una producción de gas del 95,7% debido a la alta acidez del catalizador. Batool et al. (2016) también reportaron la máxima producción de gas a partir de la pirólisis catalítica de PE, con un catalizador ZSM-5 altamente ácido. Según Lee (2012) y Williams (2006), el PE tiene una estructura de carbono de cadena larga, y su degradación se produce aleatoriamente en moléculas de cadena más pequeñas a través de la escisión aleatoria de la cadena, lo que puede promover la producción de gas. Durante la pirólisis del PE, que sólo mantiene los enlaces C-H y C-C, inicialmente se produjo la ruptura de la columna vertebral de la macromolécula y se produjeron radicales libres estables. Además, se produjeron los pasos de hidrogenación, lo que condujo a la síntesis de radicales libres secundarios (nuevo enlace C-H estable), que dio lugar a la β-escisión y produjo un grupo insaturado (Rizzarelli et al., 2016).
La pirólisis catalítica de PP/PE (proporción 50/50%) no mostró ninguna diferencia significativa en los rendimientos generales del producto cuando se utilizó tanto AA-NZ como TA-NZ. El aceite líquido producido a partir de la pirólisis catalítica de PP/PE fue del 44 y el 40% con los catalizadores TA-NZ y AA-NZ, respectivamente. Una ligera disminución en el rendimiento de aceite líquido de AA-NZ podría deberse a su alta acidez. Syamsiro et al. (2014) informaron de que AA-NZ con HCl tiene una alta acidez en comparación con TA-NZ, produjo menos rendimiento de aceite líquido y tuvo una alta producción de gases. En general, la pirólisis catalítica de PP/PE produjo la máxima cantidad de gas con bajas cantidades de carbón. La elevada producción de gas puede deberse a la presencia de PP. La degradación del PP potencia el proceso de carbocación debido a la presencia de carbono terciario en su cadena de carbono (Jung et al., 2010). Además, la degradación del PE en presencia del catalizador también favorece la producción de gas con un bajo rendimiento de aceite líquido. Sin embargo, cuando la pirólisis catalítica de PP y PE se llevó a cabo por separado con PS, se observó una diferencia significativa en el rendimiento del producto.
Hubo una diferencia significativa en el rendimiento de aceite líquido de 54 y 34% para la pirólisis catalítica de PS/PP (proporción 50/50%) con catalizadores TA-NZ y AA-NZ, respectivamente. Del mismo modo, se observó una diferencia significativa en el rendimiento de carbón de 20,3 y 35,2%, mientras que el alto rendimiento de gases fue de 25,7 y 30,8% utilizando los catalizadores TA-NZ y AA-NZ, respectivamente. López et al. (2011) y Seo et al. (2003) informaron que un catalizador con alta acidez promueve el proceso de craqueo y produce la máxima producción de gas. Además, la presencia de PP también mejora la producción de gas debido al proceso de carbocación durante la degradación (Jung et al., 2010). Kim et al. (2002) informaron de que la degradación del PP produce el máximo de gas en presencia de catalizadores ácidos.
La pirólisis catalítica del PS con el PE (proporción 50/50%) en presencia del catalizador TA-NZ produjo un 44% de aceite líquido, sin embargo se obtuvo un 52% de aceite líquido utilizando el catalizador AA-NZ. Kiran et al. (2000) llevaron a cabo la pirólisis de PS con PE en diferentes proporciones e informaron de que un aumento de la concentración de PE disminuía la concentración de aceite líquido con el aumento de gas. La presencia de PS con PE promueve el proceso de degradación debido a la producción de un anillo de benceno estable activo del PS (Miandad et al., 2016b). Wu et al. (2014) realizaron un TGA de PS con PE y observaron dos picos, el primero para el PS a baja temperatura, seguido de la degradación del PE a alta temperatura. Además, la degradación del PE sigue un proceso de cadena de radicales libres y un proceso de hidrogenación, mientras que el PS sigue un proceso de cadena de radicales que incluye varios pasos (Kiran et al., 2000). Por lo tanto, incluso teniendo en cuenta los fenómenos de degradación, el PS dio lugar a una mayor degradación en comparación con el PE y produjo anillos de benceno estables (McNeill et al., 1990).
La pirólisis catalítica de PS/PE/PP (proporción 50/25/25%) mostró rendimientos de aceite líquido ligeramente inferiores en comparación con la pirólisis catalítica de todos los tipos de plástico individuales. El rendimiento de aceite de ambos catalizadores, TA-NZ y AA-NZ, en este caso, es similar, 44 y 40%, respectivamente. La producción de carbón fue mayor (29,7%) con el catalizador AA-NZ que (19,0%) con el catalizador TA-NZ, lo que puede deberse a las reacciones de polimerización (Wu y Williams, 2010). Además, la adición de PET con PS, PE y PP (proporción 20/40/20/20%) redujo los rendimientos de aceite líquido hasta el 28 y el 30% en general, utilizando los catalizadores TA-NZ y AA-NZ, respectivamente, con mayores fracciones de carbón y gas. Demirbas (2004) llevó a cabo la pirólisis de PS/PE/PP e informó de resultados similares para el rendimiento del producto. Adnan et al. (2014) llevaron a cabo la pirólisis catalítica de PS y PET utilizando el catalizador Al-Al2O3 con proporciones de 80/20% y reportaron sólo un 37% de aceite líquido. Además, Yoshioka et al. (2004) informaron de la máxima producción de gas y carbón con una producción insignificante de aceite líquido a partir de la pirólisis catalítica de PET. Además, también se informó de la máxima producción de carbón cuando la pirólisis catalítica de PET se llevó a cabo con otros plásticos (Bhaskar et al., 2004). La mayor producción de carbón de la pirólisis de PET se debió a las reacciones de carbonización y condensación durante su pirólisis a alta temperatura (Yoshioka et al., 2004). Además, la presencia del átomo de oxígeno también favorece la alta producción de char de la pirólisis catalítica del PET (Xue et al., 2017). Thilakaratne et al. (2016) informaron de que la producción de radicales libres de benceno, con dos carbonos activados, es el precursor del coque catalítico de la degradación del PET.
Efecto de los catalizadores en la composición del aceite líquido
La composición química del aceite líquido producido por la pirólisis catalítica de diferentes residuos plásticos utilizando catalizadores TA-NZ y AA-NZ se caracterizó por GC-MS (Figuras 4, 5). La composición del aceite líquido producido se ve afectada por los diferentes tipos de materia prima y catalizadores utilizados en el proceso de pirólisis (Miandad et al., 2016a,b,c). El aceite líquido producido a partir de los distintos tipos de plástico, como el PS, el PP y el PE, contenía una mezcla de compuestos aromáticos, alifáticos y otros hidrocarburos. Los compuestos aromáticos encontrados en el aceite, procedentes del PS y del PE, eran mayores que los del PP utilizando el catalizador TA-NZ. Los compuestos aromáticos aumentaron en el aceite de PS y PP, pero se redujeron en el de PE cuando se utilizó el catalizador AA-NZ. El catalizador mesoporoso y ácido conduce a la producción de hidrocarburos de cadena más corta debido a su alta capacidad de craqueo (López et al., 2011). Sin embargo, los catalizadores microporosos y menos ácidos favorecen la producción de hidrocarburos de cadena larga ya que el proceso de craqueo se produjo sólo en la superficie exterior de los catalizadores. En general, en presencia de catalizadores, el PE y el PP siguen el mecanismo de escisión de la cadena aleatoria, mientras que el PS sigue el mecanismo de descomposición o escisión de la cadena final (Cullis y Hirschler, 1981; Peterson et al., 2001). La escisión de la cadena final da lugar a la producción de monómeros, mientras que la escisión de la cadena aleatoria produce oligómeros y monómeros (Peterson et al., 2001).
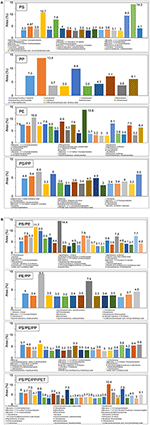
Figura 4. (A,B) GC-MS de aceite líquido producido a partir de diferentes tipos de residuos de plástico con TA-NZ.
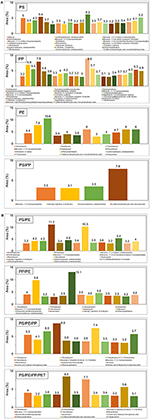
Figura 5. (A,B) GC-MS del aceite líquido producido a partir de diferentes tipos de residuos plásticos con AA-NZ.
El aceite líquido producido a partir de la pirólisis catalítica del PE, cuando se utilizan ambos catalizadores, produjo principalmente naftaleno, fenantreno, naftaleno, 2-etil-, 1-pentadeceno, antraceno, 2-metil-, hexadecano, etc. (Figuras 4A, 5A). Estos resultados coinciden con varios otros estudios (Lee, 2012; Xue et al., 2017). La producción de un derivado del benceno revela que TA-NZ mejora el proceso de aromatización en comparación con AA-NZ. Xue et al. (2017) informaron de que las olefinas intermedias producidas a partir de la pirólisis catalítica de PE, se aromatizaron aún más dentro de los poros de los catalizadores. Sin embargo, la reacción de aromatización conduce además a la producción de átomos de hidrógeno que pueden mejorar el proceso de aromatización. Lee (2012) informó de que el ZSM-5 producía más compuestos aromáticos en comparación con el catalizador de mordenita, debido a su estructura cristalina.
Hay dos posibles mecanismos que pueden implicar la degradación del PE en presencia de un catalizador; la abstracción de iones híbridos debido a la presencia de sitios Lewis o, debido al mecanismo de iones de carbenio a través de la adición de un protón (Rizzarelli et al., 2016). Inicialmente, la degradación comienza en la superficie externa de los catalizadores y, posteriormente, procede a una mayor degradación en los poros interiores de los mismos (Lee, 2012). Sin embargo, los catalizadores microporosos dificultan la entrada de moléculas más grandes y, por lo tanto, se producen compuestos de mayor cadena de carbono a partir de la pirólisis catalítica de PE con catalizadores microporosos. Además, en presencia de catalizadores ácidos, debido al mecanismo del carbenio, puede aumentar la formación de compuestos aromáticos y olefinas (Lee, 2012). Lin et al. (2004) informaron de la producción de olefinas altamente reactivas, como productos intermedios durante la pirólisis catalítica de PE, que pueden favorecer la producción de parafinas y compuestos aromáticos en el aceite líquido producido. Además, la presencia de un catalizador ácido y un átomo de hidrógeno libre puede conducir a la alquilación del tolueno y el benceno, convirtiendo el benceno alquilado intermedio en la producción de naftaleno debido a la aromatización (Xue et al., 2017).
El aceite líquido producido a partir de la pirólisis catalítica de PS con TA-NZ y AA-NZ, contiene diferentes tipos de compuestos. El alfa-metilestireno, el benceno, el 1,1′-(2-buteno-1,4-diil)bis-, el bibencilo, el benceno, el (1,3-propanediilo), el fenantreno, el 2-fenilnaftaleno, etc., fueron los principales compuestos encontrados en el aceite líquido producido (Figuras 4A, 5A). El aceite líquido producido a partir de la pirólisis catalítica del PS, con ambos catalizadores activados, contiene principalmente hidrocarburos aromáticos con algunos compuestos de parafinas, naftalina y olefinas (Rehan et al., 2017). Sin embargo, en presencia de un catalizador, se logró la máxima producción de compuestos aromáticos (Xue et al., 2017). Ramli et al. (2011) también informaron de la producción de olefinas, naftaleno con compuestos aromáticos a partir de la pirólisis catalítica de PS con Al2O3, soportado con catalizadores de Cd y Sn. La degradación del PS comienza con el craqueo en la superficie exterior del catalizador y luego es seguido por la reformación dentro de los poros del catalizador (Uemichi et al., 1999). Inicialmente, el craqueo del polímero se lleva a cabo por el sitio del ácido de Lewis en la superficie de los catalizadores para producir intermedios carbocatiónicos, que luego se evaporan o se someten a reformación dentro de los poros del catalizador (Xue et al., 2017).
La pirólisis catalítica del PS produce principalmente estireno y su derivado como los principales compuestos en el aceite líquido producido (Siddiqui y Redhwi, 2009; Rehan et al., 2017). La conversión del estireno en su derivado aumentó en presencia de catalizadores protonados debido a la hidrogenación (Kim et al., 2002). Shah y Jan (2015) y Ukei et al. (2000) informaron de que la hidrogenación del estireno aumentaba con el incremento de la temperatura de reacción. Ogawa et al. (1982) llevaron a cabo la pirólisis del PS con el catalizador de alúmina-sílice a 300°C y encontraron la hidrogenación del estireno a su derivado. Ramli et al. (2011) informaron del posible mecanismo de degradación del PS en catalizadores ácidos que puede ocurrir debido al ataque de un protón asociado a los sitios ácidos de Bronsted, dando lugar al mecanismo de iones de carbenio, que además sufre β-escisión y posteriormente es seguido por la transferencia de hidrógeno. Además, la reacción de reticulación se vio favorecida por los sitios ácidos de Bronsted fuertes y cuando se produjo esta reacción, el craqueo completo puede disminuir en cierta medida y mejorar la producción de carbón (Serrano et al., 2000). Además, los catalizadores de sílice-alúmina no tienen sitios ácidos de Bronsted fuertes, aunque puede que no mejore la reacción de reticulación pero sí favorezca el proceso de hidrogenación. Por lo tanto, puede ser la razón por la que no se encontró estireno en el aceite líquido, sin embargo, se detectó su derivado en altas cantidades (Lee et al., 2001). Xue et al. (2017) también informaron de la desalquilación del estireno, debido al retraso en la evaporación dentro del reactor, lo que puede conducir a un proceso de reformado mejorado y dar lugar a la producción de un derivado del estireno. TA-NZ y AA-NZ contienen una elevada cantidad de alúmina y sílice que conduce a la hidrogenación del estireno a su derivado, dando lugar a la producción de monómeros de estireno en lugar de estireno.
La pirólisis catalítica del PP produjo una mezcla compleja de aceite líquido que contenía compuestos aromáticos, olefinas y naftalina. El benceno, el 1,1′-(2-buteno-1,4-diil)bis-, el benceno, el 1,1′-(1,3-propanediil)bis-, el antraceno, el 9-metil-, el naftaleno, el 2-fenil-, el 1,2,3,4-tetrahidro-1-fenil-, el naftaleno, el fenantreno, etc. fueron los principales compuestos encontrados en el aceite líquido (Figuras 4A, 5A). Estos resultados están en consonancia con otros estudios que llevaron a cabo la pirólisis catalítica de PP con varios catalizadores (Marcilla et al., 2004). Además, la degradación del PP con AA-NZ dio lugar a la máxima producción de compuestos fenólicos. La mayor producción se debió quizás a la presencia de sitios altamente ácidos, ya que favorece la producción de compuestos fenólicos. Además, la presencia de un sitio altamente ácido en los catalizadores potenció el mecanismo de oligomerización, aromatización y desoxigenación que condujo a la producción de compuestos poliaromáticos y naftalenos. Dawood y Miura (2002) también informaron de la elevada producción de estos compuestos a partir de la pirólisis catalítica de PP con una HY-zeolita modificada de alta acidez.
La composición del aceite procedente de la pirólisis catalítica de PP con PE contiene compuestos que se encuentran en el aceite de ambas materias primas de tipo plástico individuales. Miandad et al. (2016b) informaron de que la composición de la materia prima también afecta a la calidad y la composición química del aceite. El aceite líquido producido a partir de la pirólisis catalítica de PE/PP contiene compuestos aromáticos, olefinas y naftalina. Los principales compuestos encontrados fueron: benceno, 1,1′-(1,3-propanediil)bis-, mono(2-etilhexilo) éster, ácido 1,2-bencenodicarboxílico, antraceno, pentadecano, fenantreno, 2-fenilnaftaleno, etc. (Figuras 4B, 5B). Jung et al. (2010) informaron de que la producción de aromáticos a partir de la pirólisis catalítica de PP/PE podría seguir el mecanismo de reacción de Diels-Alder y a continuación la deshidrogenación. Además, la pirólisis catalítica de PP y PE realizada individualmente con PS, produjo principalmente compuestos aromáticos debido a la presencia de PS. El aceite líquido producido a partir de PS/PP contiene benceno, 1,1′-(1,3-propanediil)bis, ácido 1,2-bencenodicarboxílico, éster disooctil, bibencilo, fenantreno, 2-fenilnaftaleno, benceno, (4-metil-1-decenil)-, etc. (Figuras 4A, 5A). La pirólisis catalítica de PS con PE produjo principalmente aceite líquido con compuestos principales de azuleno, naftaleno, 1-metil-, naftaleno, 2-etenilo, benceno, 1,1′-(1,3-propanodiil)bis-, fenantreno, 2-fenilnaftaleno, benceno, 1,1′-(1-metil-1,2-etanodiil)bis- y algunos otros compuestos también (Figuras 4B, 5B). Miskolczi et al. (2006) llevaron a cabo la pirólisis de PS con PE con una proporción del 10 y el 90%, respectivamente, e informaron de la máxima producción de aromáticos incluso con una proporción muy baja de PS. Miandad et al. (2016b) informaron que la pirólisis térmica de PE con PS sin catalizador, dio lugar a la conversión de PE en aceite líquido con una alta composición de aromáticos. Sin embargo, la pirólisis térmica del único PE sin catalizador lo convirtió en cera en lugar de aceite líquido debido a su fuerte estructura ramificada de cadena larga (Lee, 2012; Miandad et al., 2016b). Wu et al. (2014) llevaron a cabo el TGA de PS con PE e informaron de que la presencia de PS favorece la degradación del PE, debido a la producción de anillos de benceno estables.
La composición química del aceite de pirólisis, por diferentes grupos funcionales, se estudió mediante FT-IR. Los datos obtenidos revelaron la presencia de grupos funcionales aromáticos y alifáticos en el aceite (Figuras 6, 7). Se observó un pico muy fuerte a 696 cm-1 en la mayoría de los aceites líquidos obtenidos utilizando ambos catalizadores, que corresponde a la alta concentración de compuestos aromáticos. Otros dos picos, que son evidentes, fueron visibles en torno a 1.456 y 1.495 cm-1 para C-C con enlaces simples y dobles, correspondientes a compuestos aromáticos. Además, al final del espectro, se observaron fuertes picos a 2.850, 2.923 y 2.958 cm-1 en todos los tipos de aceites líquidos, excepto el PS, correspondientes al tramo C-H de los compuestos alcanos. En general, el aceite líquido obtenido de la pirólisis catalítica de diferentes residuos plásticos utilizando el catalizador AA-NZ, mostró más picos que las muestras de los catalizadores TA-NZ. Estos picos adicionales correspondían a compuestos aromáticos, alcanos y alquenos. Esto indica que, como se esperaba, el AA-NZ tenía mejores propiedades catalíticas que el TA-NZ. Varios investigadores han informado de resultados similares, según los cuales en el aceite líquido producido a partir de PS predominaban los aromáticos. Tekin et al. (2012) y Panda y Singh (2013) también informaron de la presencia de aromáticos con algunos alcanos y alquenos a partir de la pirólisis catalítica del PP. Kunwar et al. (2016) llevaron a cabo la pirólisis térmica y catalítica de PE e informaron de que el aceite líquido producido contenía alcanos y alquenos como grupo funcional principal. En general, el análisis FT-IR proporcionó más información sobre la composición química del aceite líquido producido, a partir de la pirólisis catalítica de diferentes residuos plásticos, utilizando catalizadores NZ modificados y confirmó aún más nuestros resultados de GC-MS.
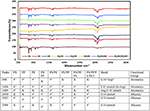
Figura 6. Análisis FT-IR del aceite líquido producido por pirólisis catalítica con TA-NZ.
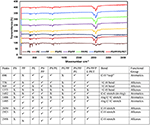
Figura 7. Análisis FT-IR del aceite líquido producido a partir de la pirólisis catalítica con AA-NZ.
Aplicaciones potenciales de los productos de pirólisis
El aceite líquido producido a partir de la pirólisis catalítica de diferentes tipos de materias primas plásticas tiene un elevado número de compuestos aromáticos, olefinas y naftalinas que se encuentran en los productos del petróleo. Además, el HHV del aceite líquido producido se ha encontrado en el rango de 41,7-44,2 MJ/kg (Tabla 2), que está muy cerca del valor energético del diesel convencional. El HHV más bajo, de 41,7 MJ/kg, se encontró en el aceite líquido obtenido a partir de PS utilizando el catalizador TA-NZ, mientras que el HHV más alto, de 44,2 MJ/kg, se obtuvo a partir de PS/PE/PP utilizando el catalizador AA-NZ. Por lo tanto, el aceite líquido de pirólisis producido a partir de varios residuos plásticos tiene el potencial de ser utilizado como una fuente alternativa de energía. Según Lee et al. (2015) y Rehan et al. (2016), la producción de electricidad se puede lograr utilizando aceite líquido de pirólisis en un motor diesel. Saptoadi y Pratama (2015) utilizaron con éxito el aceite líquido de pirólisis como alternativa en una estufa de queroseno. Además, los compuestos aromáticos producidos pueden utilizarse como materia prima para la polimerización en diversas industrias químicas (Sarker y Rashid, 2013; Shah y Jan, 2015). Además, varios investigadores utilizaron el aceite líquido producido como combustible para el transporte después de mezclarlo con diésel convencional en diferentes proporciones. Los estudios se llevaron a cabo para explorar el potencial del aceite líquido producido en el contexto del rendimiento del motor y las emisiones de escape del vehículo. Nileshkumar et al. (2015) y Lee et al. (2015) informaron de que la proporción de mezcla de 20:80% de aceite líquido pirolítico y diésel convencional, respectivamente, dio resultados de rendimiento del motor similares a los del diésel convencional. Además, con la misma proporción de mezcla, las emisiones de escape también fueron similares, sin embargo, las emisiones de escape aumentaron con el aumento de la cantidad mezclada de aceite de pirólisis (Frigo et al., 2014; Mukherjee y Thamotharan, 2014).
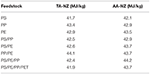
Tabla 2. Altos valores caloríficos (HHV) del aceite de pirólisis de varias materias primas utilizando catalizadores TA-NZ y AA-NZ.
El residuo (char) que queda después del proceso de pirólisis puede utilizarse para varias aplicaciones medioambientales. Varios investigadores activaron el char mediante vapor y activación térmica (López et al., 2009; Heras et al., 2014). El proceso de activación aumentó la superficie BET y redujo el tamaño de los poros del carbón (López et al., 2009). Además, Bernando (2011) mejoró el carbón plástico con biomaterial y llevó a cabo la adsorción (3,6-22,2 mg/g) del colorante azul de metileno de las aguas residuales. Miandad et al. (2018) utilizaron el carbón vegetal obtenido de la pirólisis de residuos plásticos PS para sintetizar un novedoso nanoadsorbente de óxidos de carbono-metal de doble capa (C/MnCuAl-LDOs) para la adsorción de rojo Congo (CR) en aguas residuales. Además, el carbón puede utilizarse como materia prima para la producción de carbón activado.
Limitaciones del análisis por GC-MS del aceite de pirólisis
Existen algunas limitaciones a la hora de realizar el análisis cuantitativo preciso de los componentes químicos del aceite de pirólisis mediante GC-MS. En este estudio, utilizamos el porcentaje de masa de las diferentes sustancias químicas encontradas en las muestras de aceite, calculado en base a las áreas de los picos identificados por una columna DP5-MS de fase normal y FID. Los picos identificados se cotejaron con la biblioteca de espectros del NIST y del banco de masas. Los compuestos se eligieron en función del índice de similitud (SI > 90%). La comparación posterior con estándares conocidos (CRM) permitió confirmar los compuestos identificados. La columna y los detectores utilizados estaban limitados únicamente a los hidrocarburos. Sin embargo, en realidad, el aceite de la mayoría de los residuos plásticos tiene una estructura química compleja y puede contener otros grupos de sustancias químicas no identificadas, como hidrocarburos que contienen azufre, nitrógeno y oxígeno. Por ello, es necesario un análisis químico cualitativo más profundo y preciso para comprender plenamente la química del aceite de pirólisis, utilizando una calibración y estandarización avanzadas y empleando diferentes detectores de EM como SCD y NCD, así como diferentes columnas de GC.
El potencial y los retos de las biorrefinerías basadas en la pirólisis
Las biorrefinerías de residuos están atrayendo una enorme atención como solución para convertir los RSU y otros residuos de biomasa en una serie de productos como combustibles, energía, calor y otros productos químicos y materiales valiosos. Se pueden desarrollar diferentes tipos de biorrefinerías, como una biorrefinería basada en la agricultura, una biorrefinería de residuos animales, una biorrefinería de aguas residuales, una biorrefinería basada en algas, una refinería de residuos plásticos, una biorrefinería basada en la silvicultura, una biorrefinería de residuos industriales y una biorrefinería de residuos alimentarios, etc., en función del tipo y la fuente de los residuos (Gebreslassie et al., 2013; De Wild et al., 2014; Nizami et al., 2017a,b; Waqas et al., 2018). Estas biorrefinerías pueden desempeñar un papel importante para reducir la contaminación ambiental relacionada con los residuos y las emisiones de GEI. Además, generan beneficios económicos sustanciales y pueden ayudar a lograr una economía circular en cualquier país.
Se puede desarrollar una biorrefinería basada en la pirólisis para tratar una serie de residuos de biomasa y residuos plásticos para producir combustibles líquidos y gaseosos, energía, biocarbón y otros productos químicos de mayor valor utilizando un enfoque integrado. El enfoque integrado ayuda a conseguir los máximos beneficios económicos y medioambientales con una producción mínima de residuos. Las biorrefinerías basadas en la pirólisis tienen muchos retos y posibilidades de mejora que deben abordarse y optimizarse para garantizar los máximos beneficios. Aunque el aceite de pirólisis contiene más energía que el carbón y algunos otros combustibles, la pirólisis en sí es un proceso que requiere mucha energía, y el producto de aceite requiere más energía para ser refinado (Inman, 2012). Esto significa que el aceite de pirólisis puede no ser mucho mejor que el diésel convencional u otros combustibles de origen fósil en términos de emisiones de gases de efecto invernadero, aunque se necesitan estudios de investigación muy detallados sobre el balance de masa y energía en todos los límites del proceso para confirmarlo. Para superar estos requisitos energéticos del proceso, pueden desarrollarse tecnologías más avanzadas que utilicen la integración de energías renovables, como la solar o la hidráulica, con biorrefinerías basadas en la pirólisis, para lograr los máximos beneficios económicos y medioambientales.
La disponibilidad de flujos de residuos plásticos y de biomasa como materias primas para las biorrefinerías basadas en la pirólisis, es otro reto importante, ya que el reciclaje no es actualmente muy eficiente, especialmente en los países en desarrollo. Los gases producidos por la pirólisis de algunos residuos plásticos, como el PVC, son tóxicos, por lo que la tecnología de tratamiento de las emisiones de la pirólisis debe perfeccionarse para lograr los máximos beneficios medioambientales. El aceite de pirólisis obtenido a partir de diversos tipos de plástico debe limpiarse considerablemente antes de utilizarlo en cualquier aplicación, para garantizar un impacto medioambiental mínimo. El alto contenido aromático del aceite de pirólisis es bueno y algunos compuestos aromáticos como el benceno, el tolueno y el estireno pueden ser refinados y vendidos en un mercado ya establecido. Sin embargo, algunos de los hidrocarburos aromáticos son cancerígenos conocidos y pueden causar graves daños a la salud humana y al medio ambiente. Por lo tanto, es necesario considerar seriamente este aspecto.
Otros aspectos para la optimización de las biorrefinerías basadas en la pirólisis, como los nuevos catalizadores avanzados emergentes, incluidos los nanocatalizadores, tienen que desarrollarse y aplicarse en los procesos de pirólisis para aumentar la calidad y el rendimiento de los productos, y para optimizar el proceso global. El mercado de los productos de biorrefinería basados en la pirólisis debe crearse o ampliarse para atraer más interés y financiación, con el fin de que este concepto sea más práctico y exitoso. Del mismo modo, es necesario centrarse más en realizar más trabajos de investigación y desarrollo para enriquecer el concepto de biorrefinería y aprovechar su verdadero potencial. Además, es fundamental realizar una evaluación detallada del impacto económico y medioambiental de las biorrefinerías durante la fase de diseño, utilizando herramientas especializadas como la evaluación del ciclo de vida (ACV). La ECV puede analizar el impacto medioambiental de la biorrefinería y de todos los productos mediante la realización de balances detallados de energía y materiales de todas las etapas de la vida útil, incluyendo la extracción y el procesamiento de las materias primas, la fabricación, la distribución del producto, el uso, el mantenimiento y la eliminación/reciclaje. Los resultados del ACV ayudarán a determinar la sostenibilidad de las biorrefinerías, lo que es crucial para tomar la decisión correcta.
Conclusiones
La pirólisis catalítica es una técnica prometedora para convertir los residuos plásticos en aceite líquido y otros productos de valor añadido, utilizando un catalizador de zeolita natural (NZ) modificado. La modificación de los catalizadores NZ se llevó a cabo mediante una novedosa activación térmica (TA) y ácida (AA) que mejoró sus propiedades catalíticas. La pirólisis catalítica del PS produjo el mayor aceite líquido (70 y 60%) en comparación con el PP (40 y 54%) y el PE (40 y 42%), utilizando los catalizadores TA-NZ y AA-NZ, respectivamente. La composición química del aceite de pirólisis se analizó mediante GC-MS, y se descubrió que la mayor parte del aceite líquido producía un alto contenido aromático con algunos compuestos alifáticos y otros hidrocarburos. Estos resultados fueron confirmados además por el análisis FT-IR, que mostró picos claros correspondientes a grupos funcionales aromáticos y otros hidrocarburos. Además, el aceite líquido producido a partir de diferentes tipos de residuos plásticos presentaba valores caloríficos (HHV) más elevados en el rango de 41,7-44,2 MJ/kg, similares a los del gasóleo convencional. Por lo tanto, tiene el potencial de ser utilizado en diversas aplicaciones energéticas y de transporte después de su posterior tratamiento y refinado. Este estudio es un paso hacia el desarrollo de biorrefinerías basadas en la pirólisis. Las biorrefinerías tienen un gran potencial para convertir los residuos en energía y otros productos valiosos y podrían ayudar a conseguir economías circulares. Sin embargo, hay muchos desafíos técnicos, operativos y socioeconómicos, como se discutió anteriormente, que deben ser superados con el fin de lograr los máximos beneficios económicos y ambientales de las biorrefinerías.
Disponibilidad de datos
Todos los conjuntos de datos generados para este estudio se incluyen en el manuscrito y / o los archivos suplementarios.
Contribuciones de los autores
RM realizó los experimentos de pirólisis y ayudó en la redacción del manuscrito. HK, JD, JG y AH han llevado a cabo la caracterización detallada de los productos del proceso. MR y ASA han analizado los datos y han redactado partes del manuscrito. MAB, MR y A-SN han corregido y editado el manuscrito. ASA e IMII apoyaron el proyecto financiera y técnicamente.
Declaración de conflicto de intereses
Los autores declaran que la investigación se llevó a cabo en ausencia de cualquier relación comercial o financiera que pudiera interpretarse como un potencial conflicto de intereses.
Agradecimientos
MR y A-SN agradecen al Centro de Excelencia en Estudios Ambientales (CEES), Universidad Rey Abdulaziz (KAU), Jeddah, KSA y al Ministerio de Educación, KSA por el apoyo financiero bajo la Subvención No. 2/S/1438. Los autores también agradecen al Decanato de Investigación Científica (DSR) de la KAU por su apoyo financiero y técnico al CEES.
Adnan, A., Shah, J., y Jan, M. R. (2014). Estudios de degradación de poliestireno utilizando catalizadores con soporte de Cu. J. Anal. Appl. Pyrol. 109, 196-204. doi: 10.1016/j.jaap.2014.06.013
CrossRef Full Text | Google Scholar
Aguado, J., Sotelo, J. L., Serrano, D. P., Calles, J. A., and Escola, J. M. (1997). Conversión catalítica de poliolefinas en combustibles líquidos sobre MCM-41: comparación con ZSM-5 y SiO2-Al2O3 amorfo. Ener fuels 11, 1225-1231. doi: 10.1021/ef970055v
CrossRef Full Text | Google Scholar
Alexandra, L. C. (2012). Residuos sólidos urbanos: Turning a Problem Into Resourceewaste: Los desafíos que enfrentan los países en desarrollo, Especialista Urbano. Banco Mundial. 2-4 p.
Batool, M., Shah, A. T., Imran Din, M., y Li, B. (2016). Pirólisis catalítica de polietileno de baja densidad utilizando unidades de keggin monovacantes encapsuladas de cetiltrimetil amonio y ZSM-5. J. Chem. 2016:2857162. doi: 10.1155/2016/2857162
CrossRef Full Text | Google Scholar
Bernando, M. (2011). «Physico-chemical characterization of chars produced in the co-pyrolysis of wastes and possible routes of valorization», en Chemical Engineering (Lisboa: Universidade Nova de Lisboa), 27-36.
Bhaskar, T., Kaneko, J., Muto, A., Sakata, Y., Jakab, E., Matsui, T., et al. (2004). Pyrolysis studies of PP/PE/PS/PVC/HIPS-Br plastics mixed with PET and dehalogenation (Br, Cl) of the liquid products. J. Anal. Appl. Pyrolysis 72, 27-33. doi: 10.1016/j.jaap.2004.01.005
CrossRef Full Text | Google Scholar
Chandrasekaran, S. R., Kunwar, B., Moser, B. R., Rajagopalan, N., and Sharma, B. K. (2015). Catalytic thermal cracking of postconsumer waste plastics to fuels. 1. Kinetics and optimization. Energy Fuels 29, 6068-6077. doi: 10.1021/acs.energyfuels.5b01083
CrossRef Full Text | Google Scholar
Cullis, C. F., y Hirschler, M. M. (1981). The Combustion of Organic Polymers. Vol. 5. London: Oxford University Press.
Dawood, A., y Miura, K. (2002). Catalytic pyrolysis of c-irradiated polypropylene (PP) over HY-zeolite for enhancing the reactivity and the product selectivity. Polym. Degrad. Stab. 76, 45-52. doi: 10.1016/S0141-3910(01)00264-6
CrossRef Full Text | Google Scholar
De Wild, P. J., Huijgen, W. J., and Gosselink, R. J. (2014). Lignin pyrolysis for profitable lignocellulosic biorefineries. Biofuels Bioprod. Biorefining 8, 645-657. doi: 10.1002/bbb.1474
CrossRef Full Text | Google Scholar
Demirbas, A. (2004). Pyrolysis of municipal plastic wastes for recovery of gasoline-range hydrocarbons. J. Anal. Appl. Pyrolysis 72, 97-102. doi: 10.1016/j.jaap.2004.03.001
CrossRef Full Text | Google Scholar
Dimitrov, N., Krehula, L. K., Siročić, A. P., and Hrnjak-Murgić, Z. (2013). Análisis de los productos de las botellas de PET recicladas mediante cromatografía de gases por pirólisis. Polym. Degrad. Stab. 98, 972-979. doi: 10.1016/j.polymdegradstab.2013.02.013
CrossRef Full Text | Google Scholar
Dziecioł, M., and Trzeszczynski, J. (2000). Productos volátiles de la degradación térmica del poli (tereftalato de etileno) en atmósfera de nitrógeno. J. Appl. Polym. Sci. 77, 1894-1901. doi: 10.1002/1097-4628(20000829)77:9<1894::AID-APP5>3.0.CO;2-Y
CrossRef Full Text | Google Scholar
Frigo, S., Seggiani, M., Puccini, M., and Vitolo, S. (2014). Producción de combustible líquido a partir de la pirólisis de neumáticos usados y su utilización en un motor Diesel. Fuel 116, 399-408. doi: 10.1016/j.fuel.2013.08.044
CrossRef Full Text | Google Scholar
Gaca, P., Drzewiecka, M., Kaleta, W., Kozubek, H., and Nowinska, K. (2008). Catalytic degradation of polyethylene over mesoporous molecular sieve MCM-41 modified with heteropoly compounds. Polish J. Environ. Stud. 17, 25-35.
Google Scholar
Gandidi, I. M., Susila, M. D., Mustofa, A., y Pambudi, N. A. (2018). Cracking térmico-catalítico de RSU reales en Bio-Crudo. J. Energy Inst. 91, 304-310. doi: 10.1016/j.joei.2016.11.005
CrossRef Full Text | Google Scholar
Gebreslassie, B. H., Slivinsky, M., Wang, B., y You, F. (2013). Life cycle optimization for sustainable design and operations of hydrocarbon biorefinery via fast pyrolysis, hydrotreating and hydrocracking. Comput. Chem. Eng. 50, 71-91. doi: 10.1016/j.compchemeng.2012.10.013
CrossRef Full Text | Google Scholar
Heras, F., Jiménez-Cordero, D., Gilarranz, M. A., Alonso-Morales, N., y Rodríguez, J. J. (2014). Activación del carbón de neumáticos usados mediante oxidación cíclica en fase líquida. Fuel Process. Technol. 127, 157-162. doi: 10.1016/j.fuproc.2014.06.018
CrossRef Full Text | Google Scholar
Inman, M. (2012). Cocinando el combustible. Nat. Clim. Change 2, 218-220. doi: 10.1038/nclimate1466
CrossRef Full Text | Google Scholar
Jung, S. H., Cho, M. H., Kang, B. S., and Kim, J. S. (2010). Pirólisis de una fracción de residuos de polipropileno y polietileno para la recuperación de aromáticos BTX utilizando un reactor de lecho fluidizado. Fuel Process. Technol. 91, 277-284. doi: 10.1016/j.fuproc.2009.10.009
CrossRef Full Text | Google Scholar
Kim, H. S., Kim, S., Kim, H. J., and Yang, H. S. (2006). Thermal properties of bio-flour-filled polyolefin composites with different compatibilizing agent type and content. Thermochim. Acta 451, 181-188. doi: 10.1016/j.tca.2006.09.013
CrossRef Full Text | Google Scholar
Kim, J. R., Yoon, J. H., and Park, D. W. (2002). Reciclaje catalítico de la mezcla de polipropileno y poliestireno. Polym. Degrad. Stab. 76, 61-67. doi: 10.1016/S0141-3910(01)00266-X
CrossRef Full Text | Google Scholar
Kiran, N., Ekinci, E., y Snape, C. E. (2000). Recyling of plastic wastes via pyrolysis. Resour. Conserv. Recycl. 29, 273-283. doi: 10.1016/S0921-3449(00)00052-5
CrossRef Full Text | Google Scholar
Kunwar, B., Moser, B. R., Chandrasekaran, S. R., Rajagopalan, N., and Sharma, B. K. (2016). Despolimerización catalítica y térmica de plástico de polietileno de alta densidad postconsumo de bajo valor. Energy 111, 884-892. doi: 10.1016/j.energy.2016.06.024
CrossRef Full Text | Google Scholar
Lecomte, H. A., y Liggat, J. J. (2006). Mecanismo de degradación de las unidades de dietilenglicol en un polímero de tereftalato. Polym. Degrad. Stab. 91, 681-689. doi: 10.1016/j.polymdegradstab.2005.05.028
CrossRef Full Text | Google Scholar
Lee, K. H. (2012). Efectos de los tipos de zeolitas en la mejora catalítica del aceite de cera de pirólisis. J. Anal. Appl. Pyrol. 94, 209-214. doi: 10.1016/j.jaap.2011.12.015
CrossRef Full Text | Google Scholar
Lee, S., Yoshida, K., y Yoshikawa, K. (2015). Aplicación del aceite de pirólisis de residuos plásticos en un motor diésel de inyección directa: Para una electrificación a pequeña escala sin red. Energy Environ. Res. 5:18. doi: 10.5539/eer.v5n1p18
CrossRef Full Text
Lee, S. Y., Yoon, J. H., Kim, J. R., y Park, D. W. (2001). Catalytic degradation of polystyrene over natural clinoptilolite zeolite. Polym. Degrad. Stab. 74, 297-305. doi: 10.1016/S0141-3910(01)00162-8
CrossRef Full Text | Google Scholar
Lin, Y. H., Yang, M. H., Yeh, T. F., and Ger, M. D. (2004). Catalytic degradation of high density polyethylene over mesoporous and microporous catalysts in a fluidised-bed reactor. Polym. Degrad. Stab. 86, 121-128. doi: 10.1016/j.polymdegradstab.2004.02.015
CrossRef Full Text | Google Scholar
López, A., Marco d, I., Caballero, B. M., Laresgoiti, M. F., Adrados, A., y Torres, A. (2011). Pirólisis de residuos plásticos municipales II: influencia de la composición de la materia prima en condiciones catalíticas. Waste Manag. 31, 1973-1983. doi: 10.1016/j.wasman.2011.05.021
CrossRef Full Text | Google Scholar
López, G., Olazar, M., Artetxe, M., Amutio, M., Elordi, G., y Bilbao, J. (2009). Activación por vapor del carbón pirolítico de neumáticos a diferentes temperaturas. J. Anal. Appl. Pyrol. 85, 539-543. doi: 10.1016/j.jaap.2008.11.002
CrossRef Full Text | Google Scholar
Ma, C., Yu, J., Wang, B., Song, Z., Xiang, J., Hu, S., et al. (2017). Pirólisis catalítica de poliestireno de alto impacto retardado por la llama sobre varios catalizadores ácidos sólidos. Fuel Process. Technol. 155, 32-41. doi: 10.1016/j.fuproc.2016.01.018
CrossRef Full Text | Google Scholar
Marcilla, A., Beltrán, M. I., Hernández, F., y Navarro, R. (2004). Desactivación de HZSM5 y HUSY durante la pirólisis catalítica de polietileno. Appl. Catal. A Gen. 278, 37-43. doi: 10.1016/j.apcata.2004.09.023
CrossRef Full Text | Google Scholar
McNeill, I. C., and Bounekhel, M. (1991). Estudios de degradación térmica de poliésteres de tereftalato: 1. Poly (alkylene terephthalates). Polymer Degrad. Stab. 34, 187-204. doi: 10.1016/0141-3910(91)90119-C
CrossRef Full Text | Google Scholar
McNeill, I. C., Zulfiqar, M., y Kousar, T. (1990). Una investigación detallada de los productos de la degradación térmica del poliestireno. Polym. Degrad. Stab. 28, 131-151. doi: 10.1016/0141-3910(90)90002-O
CrossRef Full Text | Google Scholar
Miandad, R., Barakat, M. A., Aburiazaiza, A. S., Rehan, M., Ismail, I. M. I., y Nizami, A. S. (2017b). Efecto de los tipos de residuos plásticos en el aceite líquido de pirólisis. Int. Biodeterior. Biodegrad. 119, 239-252. doi: 10.1016/j.ibiod.2016.09.017
CrossRef Full Text | Google Scholar
Miandad, R., Barakat, M. A., Aburiazaiza, A. S., Rehan, M., y Nizami, A. S. (2016a). Pirólisis catalítica de residuos plásticos: una revisión. Process Safety Environ. Protect. 102, 822-838. doi: 10.1016/j.psep.2016.06.022
CrossRef Full Text | Google Scholar
Miandad, R., Barakat, M. A., Rehan, M., Aburiazaiza, A. S., Ismail, I. M. I., and Nizami, A. S. (2017a). Plastic waste to liquid oil through catalytic pyrolysis using natural and synthetic zeolite catalysts. Waste Manag. 69, 66-78. doi: 10.1016/j.wasman.2017.08.032
PubMed Abstract | CrossRef Full Text | Google Scholar
Miandad, R., Kumar, R., Barakat, M. A., Basheer, C., Aburiazaiza, A. S., Nizami, A. S., et al. (2018). Conversión no aprovechada del carbón de residuos plásticos en LDOs de carbono-metal para la adsorción de rojo Congo. J Colloid Interface Sci. 511, 402-410. doi: 10.1016/j.jcis.2017.10.029
PubMed Abstract | CrossRef Full Text | Google Scholar
Miandad, R., Nizami, A. S., Rehan, M., Barakat, M. A., Khan, M. I., Mustafa, A., et al. (2016b). Influencia de la temperatura y el tiempo de reacción en la conversión de residuos de poliestireno en aceite líquido de pirólisis. Waste Manag. 58, 250-259. doi: 10.1016/j.wasman.2016.09.023
PubMed Abstract | CrossRef Full Text | Google Scholar
Miandad, R., Rehan, M., Nizami, A. S., Barakat, M. A. E. F., and Ismail, I. M. (2016c). «The energy and value- added products from pyrolysis of waste plastics,» in Recycling of Solid Waste for Biofuels and Bio- Chemicals, eds O. P. Karthikeyan, K. H. Subramanian, and S. Muthu (Singapore: Springer), 333-355.
Google Scholar
Miskolczi, N., Bartha, L., and Deak, G. (2006). Thermal degradation of polyethylene and polystyrene from the packaging industry over different catalysts into fuel-like feed stocks. Polym. Degrad. Stab. 91, 517-526. doi: 10.1016/j.polymdegradstab.2005.01.056
CrossRef Full Text | Google Scholar
Mukherjee, M. K., and Thamotharan, P. C. (2014). Rendimiento y prueba de emisiones de varias mezclas de aceite de plástico de desecho con diésel y etanol en un motor diésel de dos cilindros de cuatro tiempos. IOSR J. Mech. Civil Eng. 11, 2278-1684. doi: 10.9790/1684-11214751
CrossRef Full Text
Nileshkumar, K. D., Jani, R. J., Patel, T. M., and Rathod, G. P. (2015). Efecto de la relación de mezcla de aceite de pirólisis de plástico y el combustible diesel en el rendimiento del motor CI de un solo cilindro. Int. J. Sci. Technol. Eng. 1, 2349-2784.
Google Scholar
Nizami, A. S., Ouda, O. K. M., Rehan, M., El-Maghraby, A. M. O., Gardy, J., Hassanpour, A., et al. (2016). El potencial de las zeolitas naturales de Arabia Saudí en las tecnologías de recuperación de energía. Energy 108, 162-171. doi: 10.1016/j.energy.2015.07.030
CrossRef Full Text | Google Scholar
Nizami, A. S., Rehan, M., Waqas, M., Naqvi, M., Ouda, O. K. M., Shahzad, K., et al. (2017a). Biorrefinerías de residuos: permitiendo las economías circulares en los países en desarrollo. Bioresour. Technol. 241, 1101-1117. doi: 10.1016/j.biortech.2017.05.097
PubMed Abstract | CrossRef Full Text | Google Scholar
Nizami, A. S., Shahzad, K., Rehan, M., Ouda, O. K. M., Khan, M. Z., Ismail, I. M. I., et al. (2017b). Desarrollo de la biorrefinería de residuos en makkah: un camino para convertir los residuos urbanos en energía renovable. Appl. Energy. 186, 189-196. doi: 10.1016/j.apenergy.2016.04.116
CrossRef Full Text | Google Scholar
Obali, Z., Sezgi, N. A., and Doğu, T. (2012). Degradación catalítica de polipropileno sobre catalizadores mesoporosos cargados de alúmina. Chem. Eng. J. 207, 421-425. doi: 10.1016/j.cej.2012.06.146
CrossRef Full Text | Google Scholar
Ogawa, T., Kuroki, T., Ide, S., and Ikemura, T. (1982). Recovery of indan derivatives from polystyrene waste. J. Appl. Polym. Sci. 27, 857-869. doi: 10.1002/app.1982.070270306
CrossRef Full Text | Google Scholar
Panda, A. K., and Singh, R. K. (2013). Optimización experimental del proceso para la degradación termo-catalítica de residuos de polipropileno a combustible líquido. Adv. Energy Eng. 1, 74-84.
Google Scholar
Peterson, J. D., Vyazovkin, S., y Wight, C. A. (2001). Kinetics of the thermal and thermo-oxidative degradation of polystyrene, polyethylene and poly (propylene). Macromol. Chem. Phys. 202, 775-784. doi: 10.1002/1521-3935(20010301)202:6<775::AID-MACP775>3.0.CO;2-G
CrossRef Full Text | Google Scholar
Ramli, M. R., Othman, M. B. H., Arifin, A., y Ahmad, Z. (2011). Red de enlaces cruzados de polidimetilsiloxano mediante mecanismos de adición y condensación (RTV). Parte I: síntesis y propiedades térmicas. Polym. Degrad. Stab. 96, 2064-2070. doi: 10.1016/j.polymdegradstab.2011.10.001
CrossRef Full Text | Google Scholar
Ratnasari, D. K., Nahil, M. A., and Williams, P. T. (2017). Pirólisis catalítica de plásticos de desecho utilizando catálisis por etapas para la producción de aceites de hidrocarburos de la gama de la gasolina. J. Anal. Appl. Pyrolysis 124, 631-637. doi: 10.1016/j.jaap.2016.12.027
CrossRef Full Text | Google Scholar
Rehan, M., Miandad, R., Barakat, M. A., Ismail, I. M. I., Almeelbi, T., Gardy, J., et al. (2017). Efecto de los catalizadores de zeolita en el aceite líquido de pirólisis. Int. Biodeterior. Biodegrad. 119, 162-175. doi: 10.1016/j.ibiod.2016.11.015
CrossRef Full Text | Google Scholar
Rehan, M., Nizami, A. S., Shahzad, K., Ouda, O. K. M., Ismail, I. M. I., Almeelbi, T., et al. (2016). Combustible líquido pirolítico: una fuente de energía renovable en La Meca. Energy Sources A 38, 2598-2603. doi: 10.1080/15567036.2016.1153753
CrossRef Full Text | Google Scholar
Rizzarelli, P., Rapisarda, M., Perna, S., Mirabella, E. F., La Carta, S., Puglisi, C., et al. (2016). Determinación de polietileno en mezclas de polímeros biodegradables y en bolsas compostables mediante Py-GC/MS y TGA. J. Anal. Appl. Pyrolysis 117,72-81. doi: 10.1016/j.jaap.2015.12.014
CrossRef Full Text | Google Scholar
Saptoadi, H., and Pratama, N. N. (2015). Utilización de aceite de desecho de plásticos como sustituto parcial del queroseno en cocinas presurizadas. Int. J. Environ. Sci. Dev. 6, 363-368. doi: 10.7763/IJESD.2015.V6.619
CrossRef Full Text | Google Scholar
Sarker, M., y Rashid, M. M. (2013). Mezcla de residuos plásticos de poliestireno y polipropileno en combustible de grado ligero utilizando el catalizador Fe2O3. Int. J. Renew. Energy Technol. Res. 2, 17-28.
Google Scholar
Seo, Y. H., Lee, K. H., y Shin, D. H. (2003). Investigation of catalytic degradation of high density, polyethylene by hydrocarbon group type analysis. J. Anal. Appl. Pyrol. 70, 383-398. doi: 10.1016/S0165-2370(02)00186-9
CrossRef Full Text | Google Scholar
Serrano, D. P., Aguado, J., and Escola, J. M. (2000). Conversión catalítica de poliestireno sobre HMCM-41, HZSM-5 y SiO2-Al2O3 amorfo: comparación con el craqueo térmico. Appl. Catal. B:Environ. 25, 181-189. doi: 10.1016/S0926-3373(99)00130-7
CrossRef Full Text | Google Scholar
Serrano, D. P., Aguado, J., and Escola, J. M. (2012). Desarrollo de catalizadores avanzados para la conversión de residuos plásticos poliolefínicos en combustibles y productos químicos. ACS Catal. 2, 1924-1941. doi: 10.1021/cs3003403
CrossRef Full Text | Google Scholar
Shah, J., and Jan, M. R. (2015). Efecto del tereftalato de polietileno en la pirólisis catalítica del poliestireno: Investigación de los productos líquidos. J. Taiwan Inst. Chem. Eng. 51, 96-102. doi: 10.1016/j.jtice.2015.01.015
CrossRef Full Text | Google Scholar
Siddiqui, M. N., and Redhwi, H. H. (2009). Pirólisis de plásticos mixtos para la recuperación de productos útiles. Fuel Process. Technol. 90, 545-552. doi: 10.1016/j.fuproc.2009.01.003
CrossRef Full Text | Google Scholar
Sriningsih, W., Saerodji, M. G., Trisunaryanti, W., Armunanto, R., and Falah, I. I. (2014). Producción de combustible a partir de residuos de plástico LDPE sobre zeolita natural soportada por metales Ni, Ni-Mo, Co y Co-Mo. Proc. Environ. Sci. 20, 215-224. doi: 10.1016/j.proenv.2014.03.028
CrossRef Full Text | Google Scholar
Syamsiro, M., Cheng, S., Hu, W., Saptoadi, H., Pratama, N. N., Trisunaryanti, W., et al. (2014). Combustible líquido y gaseoso a partir de residuos plásticos mediante procesos secuenciales de pirólisis y reformado catalítico sobre catalizadores de zeolita natural de Indonesia. Waste Technol. 2, 44-51. doi: 10.12777/wastech.2.2.44-51
CrossRef Full Text | Google Scholar
Tekin, K., Akalin, M. K., Kadi, C., and Karagöz, S. (2012). Degradación catalítica de residuos de polipropileno por pirólisis. J. Energy Ins. 85, 150-155. doi: 10.1179/1743967112Z.00000000029
CrossRef Full Text | Google Scholar
Thilakaratne, R., Tessonnier, J. P., and Brown, R. C. (2016). Conversión de funcionalidades metoxi e hidroxilo de monómeros fenólicos sobre zeolitas. Green Chem. 18, 2231-2239. doi: 10.1039/c5gc02548f
CrossRef Full Text | Google Scholar
Uemichi, Y., Hattori, M., Itoh, T., Nakamura, J., y Sugioka, M. (1998). Deactivation behaviors of Zeolite and Silica- Alumina catalysts in the degradation of polyethylene. Ind. Eng. Chem. Res. 37, 867-872. doi: 10.1021/ie970605c
CrossRef Full Text | Google Scholar
Uemichi, Y., Nakamura, J., Itoh, T., Sugioka, M., Garforth, A. A., and Dwyer, J. (1999). Conversión de polietileno en combustibles para gasolina mediante una degradación catalítica en dos etapas utilizando sílice-alúmina y zeolita HZSM-5. Ind. Eng. Chem. Res. 38, 385-390. doi: 10.1021/ie980341+
CrossRef Full Text | Google Scholar
Ukei, H., Hirose, T., Horikawa, S., Takai, Y., Taka, M., Azuma, N., et al. (2000). Catalytic degradation of polystyrene into styrene and a design of recyclable polystyrene with dispersed catalysts. Catal. Today 62, 67-75. doi: 10.1016/S0920-5861(00)00409-0
CrossRef Full Text | Google Scholar
Waqas, M., Rehan, M., Aburiazaiza, A. S., y Nizami, A. S. (2018). «Chapter 17-Wastewater Biorefinery based on the microbial electrolysis cell: opportunities and challenges», en Progress and Recent Trends in Microbial Fuel Cells, eds K. Dutta and P. Kundu (New York, NY: Elsevier Inc.), 347-374. doi: 10.1016/B978-0-444-64017-8.00017-8
CrossRef Full Text
Williams, P. T. (2006). «Rendimiento y composición de los gases y aceites / ceras de la materia prima de reciclaje de residuos de plástico». En Reciclaje de materias primas y pirólisis de plásticos de desecho: Converting Waste Plastics into Diesel and Other Fuels, eds J. Scheirs and W. Kaminsky (West Sussex: John Wiley & Sons Press), 285-309.
Google Scholar
Wu, C., and Williams, P. T. (2010). Pirólisis-gasificación de plásticos, plásticos mixtos y residuos plásticos del mundo real con y sin catalizador Ni-Mg-Al. Fuel 89, 3022-3032. doi: 10.1016/j.fuel.2010.05.032
CrossRef Full Text | Google Scholar
Wu, J., Chen, T., Luo, X., Han, D., Wang, Z., and Wu, J. (2014). Análisis TG/FTIR sobre el comportamiento de copirólisis de PE, PVC y PS. Waste Manag. 34, 676-682. doi: 10.1016/j.wasman.2013.12.005
PubMed Abstract | CrossRef Full Text | Google Scholar
Xue, Y., Johnston, P., y Bai, X. (2017). Efecto del modo de contacto del catalizador y la atmósfera de gas durante la pirólisis catalítica de plásticos de desecho. Energy Conv. Manag. 142, 441-451. doi: 10.1016/j.enconman.2017.03.071
CrossRef Full Text | Google Scholar
Yoshioka, T., Grause, G., Eger, C., Kaminsky, W., y Okuwaki, A. (2004). Pirólisis de poli (tereftalato de etileno) en una planta de lecho fluidizado. Polym. Degrad. Stab. 86, 499-504. doi: 10.1016/j.polymdegradstab.2004.06.001
CrossRef Full Text | Google Scholar
Zeaiter, J. (2014). Un estudio de proceso sobre la pirólisis de residuos de polietileno. Fuel 133, 276-282. doi: 10.1016/j.fuel.2014.05.028
CrossRef Full Text | Google Scholar