Introduction
Produkcja i zużycie odpadów plastikowych wzrasta w alarmującym tempie, wraz ze wzrostem populacji ludzkiej, szybkim wzrostem gospodarczym, ciągłą urbanizacją i zmianami w stylu życia. Ponadto, krótka żywotność tworzyw sztucznych przyspiesza codzienną produkcję odpadów z tworzyw sztucznych. Światowa produkcja tworzyw sztucznych została oszacowana na około 300 mln ton rocznie i z roku na rok stale wzrasta (Miandad i in., 2016a; Ratnasari i in., 2017). Tworzywa sztuczne są wykonane z węglowodorów petrochemicznych z dodatkami, takimi jak środki zmniejszające palność, stabilizator i utleniacze, które utrudniają biodegradację (Ma i in., 2017). Recykling odpadów z tworzyw sztucznych jest prowadzony na różne sposoby, ale w większości krajów rozwijających się powszechną praktyką w gospodarce odpadami z tworzyw sztucznych jest składowanie na otwartej przestrzeni lub na składowiskach (Gandidi i in., 2018). Unieszkodliwianie odpadów z tworzyw sztucznych na składowiskach stanowi siedlisko dla owadów i gryzoni, które mogą powodować różnego rodzaju choroby (Alexandra, 2012). Ponadto koszty transportu, pracy i konserwacji mogą zwiększyć koszty projektów recyklingowych (Gandidi i in., 2018). Dodatkowo, ze względu na szybką urbanizację, zmniejsza się powierzchnia dostępna na składowiska odpadów, zwłaszcza w miastach. Piroliza jest powszechną techniką stosowaną do przekształcania odpadów z tworzyw sztucznych w energię, w postaci paliw stałych, ciekłych i gazowych.
Piroliza to degradacja termiczna odpadów z tworzyw sztucznych w różnych temperaturach (300-900°C), przy braku tlenu, w celu wytworzenia ciekłego oleju (Rehan et al., 2017). Różne rodzaje katalizatorów są stosowane w celu poprawy procesu pirolizy odpadów z tworzyw sztucznych i zwiększenia wydajności procesu. Katalizatory mają bardzo krytyczną rolę w promowaniu wydajności procesu, ukierunkowaniu na konkretną reakcję i zmniejszeniu temperatury i czasu procesu (Serrano i in., 2012; Ratnasari i in., 2017). Szeroki zakres katalizatorów został zastosowany w procesach pirolizy tworzyw sztucznych, ale najszerzej stosowanymi katalizatorami są ZSM-5, zeolit, Y-zeolit, FCC i MCM-41 (Ratnasari i in., 2017). Reakcja katalityczna podczas pirolizy odpadów z tworzyw sztucznych na stałych katalizatorach kwasowych może obejmować reakcje krakingu, oligomeryzacji, cyklizacji, aromatyzacji i izomeryzacji (Serrano i in., 2012).
Wiele badań donosi o zastosowaniu mikroporowatych i mezoporowatych katalizatorów do konwersji odpadów z tworzyw sztucznych do ciekłego oleju i węgla drzewnego. Uemichi i wsp. (1998) przeprowadzili katalityczną pirolizę polietylenu (PE) przy użyciu katalizatorów HZSM-5. Zastosowanie HZSM-5 spowodowało zwiększenie produkcji ciekłego oleju o składzie związków aromatycznych i izoalkanów. Gaca i wsp. (2008) przeprowadzili pirolizę odpadów tworzyw sztucznych z udziałem modyfikowanych katalizatorów MCM-41 i HZSM-5 i stwierdzili, że zastosowanie HZSM-5 prowadzi do produkcji lżejszych węglowodorów (C3-C4) z maksymalną zawartością związków aromatycznych. Lin et al. (2004) zastosowali różne rodzaje katalizatorów i stwierdzili, że nawet mieszanie HZSM-5 z mezoporowatym SiO2-Al2O3 lub MCM-41 prowadzi do maksymalnej produkcji ciekłego oleju przy minimalnej produkcji gazu. Aguado i wsp. (1997) stwierdzili, że z katalitycznej pirolizy PE z udziałem HZSM-5 można uzyskać związki aromatyczne i alifatyczne, natomiast zastosowanie mezoporowatego MCM-41 spowodowało zmniejszenie ilości wytwarzanych związków aromatycznych ze względu na jego niską aktywność katalityczną wobec kwasów. Zastosowanie katalizatorów syntetycznych usprawniło cały proces pirolizy i poprawiło jakość produkowanego oleju ciekłego. Jednakże zastosowanie katalizatorów syntetycznych zwiększyło koszty procesu pirolizy.
Katalizatory NZ mogą być wykorzystane do przezwyciężenia ekonomicznych wyzwań pirolizy katalitycznej, które wiążą się ze stosowaniem drogich katalizatorów. W ostatnich latach, NZ zyskał znaczną uwagę ze względu na swoje potencjalne zastosowania środowiskowe. Naturalnie, NZ występuje w Japonii, USA, na Kubie, w Indonezji, na Węgrzech, we Włoszech i w Królestwie Arabii Saudyjskiej (KSA) (Sriningsih i in., 2014; Nizami i in., 2016). Złoże NZ w KSA leży głównie w Harrat Shama i Jabbal Shama i zawiera głównie minerały mordenitu o wysokiej stabilności termicznej, co czyni go odpowiednim jako katalizator w pirolizie odpadów z tworzyw sztucznych. Sriningsih et al. (2014) zmodyfikowali NZ z Sukabumi w Indonezji poprzez osadzanie metali przejściowych, takich jak Ni, Co i Mo i przeprowadzili pirolizę polietylenu o niskiej gęstości (LDPE). Gandidi et al. (2018) wykorzystali NZ z Lampung, Indonezja do katalitycznej pirolizy stałych odpadów komunalnych.
Jest to pierwsze badanie mające na celu zbadanie wpływu zmodyfikowanego saudyjskiego zeolitu naturalnego, na jakość produktu i wydajność z katalitycznej pirolizy odpadów z tworzyw sztucznych. Katalizator z naturalnego zeolitu saudyjskiego był modyfikowany poprzez nowatorską aktywację termiczną (TA-NZ) w 550°C oraz aktywację kwasową (AA-NZ) za pomocą HNO3 w celu poprawy jego właściwości katalitycznych. Po raz pierwszy przeprowadzono katalityczną pirolizę różnych rodzajów odpadów tworzyw sztucznych (PS, PE, PP i PET) pojedynczych lub zmieszanych w różnych proporcjach, w obecności zmodyfikowanego katalizatora zeolitu naturalnego (NZ) w małym reaktorze pirolizy w skali pilotowej. Badano jakość i wydajność produktów pirolizy, takich jak ciekły olej, gaz i węgiel drzewny. Skład chemiczny ciekłego oleju analizowano metodą GC-MS. Ponadto, przedyskutowano potencjał i wyzwania stojące przed biorafineriami opartymi na pirolizie.
Materiały i metody
Przygotowanie materiału wsadowego i uruchomienie reaktora
Odpady plastikowe użyte jako materiał wsadowy w procesie pirolizy katalitycznej zostały zebrane z Jeddah i obejmowały torby na zakupy, jednorazowe kubki i talerze na soki oraz butelki na wodę pitną, które składają się odpowiednio z polietylenu (PE), polipropylenu (PP), polistyrenu (PS) i politereftalanu etylenu (PET). Wyboru tych tworzyw dokonano ze względu na fakt, że są one głównym źródłem odpadów z tworzyw sztucznych wytwarzanych w KSA. W celu uzyskania jednorodnej mieszaniny, wszystkie próbki odpadów rozdrobniono na mniejsze kawałki o powierzchni około 2 cm2. Pirolizę katalityczną prowadzono z wykorzystaniem pojedynczych lub mieszaniny tych odpadów z tworzyw sztucznych w różnych proporcjach (tabela 1). W każdym eksperymencie stosowano 1000 g substratu i 100 g katalizatora. Saudyjski zeolit naturalny (NZ), zebrany z Harrat-Shama położonego w północno-zachodniej części miasta Jeddah, KSA (Nizami i in., 2016), został zmodyfikowany przez obróbkę termiczną i kwasową i użyty w tych eksperymentach pirolizy katalitycznej. Przed modyfikacją i wykorzystaniem w pirolizie NZ został rozdrobniony do postaci proszku (<100 nm) w młynie kulowym (Retsch MM 480) przez 3 h z częstotliwością 20 Hz/sek. W celu aktywacji termicznej (TA) NZ wygrzewano w piecu muflowym w temperaturze 550°C przez 5 h, natomiast w celu aktywacji kwasowej (AA) NZ moczono w 0,1 M roztworze kwasu azotowego (HNO3) przez 48 h i wytrząsano w sposób ciągły przy użyciu wytrząsarki cyfrowej IKA HS 501 z prędkością 50 obr/min. Następnie próbkę przemywano wodą dejonizowaną aż do uzyskania normalnego pH.
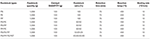
Tabela 1. Schemat doświadczenia.
Doświadczenia przeprowadzono w małym reaktorze do pirolizy w skali pilotowej w temperaturze 450°C, stosując szybkość ogrzewania 10°C/min i czas reakcji 75 min (rys. 1). Po zakończeniu każdego eksperymentu obliczono wagowy uzysk każdego z produktów pirolizy. Charakterystykę wytworzonego oleju ciekłego przeprowadzono w celu zbadania wpływu składu surowca na jakość oleju ciekłego wytworzonego w obecności modyfikowanego NZ. W celu uzyskania optymalnych warunków prowadzenia procesu, takich jak temperatura i czas reakcji (75 min) w warunkach kontrolowanych, przeprowadzono analizę TGA. W TGA pobierano po 10 μg każdego rodzaju odpadów z tworzyw sztucznych i ogrzewano z szybkością 10°C od 25 do 900°C pod ciągłym przepływem azotu (50 ml/min). Autorzy niniejszej pracy opublikowali ostatnio prace dotyczące wpływu składu substratów oraz naturalnych i syntetycznych katalizatorów zeolitowych bez modyfikacji katalizatora na różne rodzaje odpadów z tworzyw sztucznych (Miandad et al., 2017b; Rehan et al., 2017).
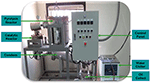
Rysunek 1. Reaktor do pirolizy w małej skali pilotażowej (Miandad et al., 2016b).
Ustawa eksperymentalna
Reaktor w małej skali pilotażowej ma możliwość zastosowania zarówno jako piroliza termiczna, jak i katalityczna, z wykorzystaniem różnych substratów, takich jak tworzywa sztuczne i materiały biomasowe (rys. 1). W tym badaniu, zmodyfikowane katalizatory NZ zostały dodane do reaktora wraz z materiałem wsadowym. Reaktor do pirolizy może pomieścić do 20 L substratu, a maksymalna bezpieczna temperatura robocza do 600°C może być osiągnięta przy pożądanych szybkościach ogrzewania. Szczegółowe parametry reaktora pirolizy zostały opublikowane wcześniej (Miandad et al., 2016b, 2017b). Wraz ze wzrostem temperatury powyżej określonych wartości, odpady z tworzyw sztucznych (polimery organiczne) przekształcają się w monomery, które trafiają do skraplacza, gdzie pary te są skraplane do ciekłego oleju. Aby utrzymać temperaturę kondensacji poniżej 10°C i zapewnić maksymalną kondensację oparów do ciekłego oleju, zastosowano system ciągłej kondensacji wykorzystujący łaźnię wodną i chłodziwo ACDelco Classic. Wyprodukowany ciekły olej został zebrany ze zbiornika zbierającego olej i przeprowadzono dalszą charakterystykę, aby odkryć jego skład chemiczny i właściwości dla innych potencjalnych zastosowań.
Metody analityczne
Olej z pirolizy scharakteryzowano przy użyciu różnych technik, takich jak chromatografia gazowa sprzężona ze spektrofotometrią masową (GC-MS), spektroskopia w podczerwieni z transformacją Fouriera (FT-IR),
kalorymetr bombowy i TGA (Mettler Toledo TGA/SDTA851), przyjmując standardowe metody ASTM. Grupy funkcyjne w oleju pirolitycznym analizowano za pomocą urządzenia FT-IR, Perkin Elmer’s, UK. Analizę FT-IR przeprowadzono stosując minimum 32 skany ze średnią 4 cm-1 sygnałów IR w zakresie częstotliwości 500-4000 cm-1.
Skład chemiczny oleju badano za pomocą GC-MS (Shimadzu QP-Plus 2010) z detektorem FI. Zastosowano kapilarną kolumnę GC o długości 30 m i szerokości 0,25 mm pokrytą warstwą 5% fenylometylopolisiloksanu (HP-5) o grubości 0,25 μm. Piec ustawiono na 50°C na 2 min, a następnie zwiększano temperaturę do 290°C, stosując szybkość ogrzewania 5°C/min. Temperaturę źródła jonów i linii transferowej utrzymywano na poziomie 230 i 300°C, a wtrysk typu splitless stosowano w temperaturze 290°C. Biblioteka danych widma masowego NIST08s została wykorzystana do identyfikacji pików chromatograficznych, a udziały procentowe pików zostały ocenione pod kątem ich całkowitej powierzchni piku chromatogramu jonowego (TIC). Wysokie wartości opałowe (HHV) wytworzonego oleju ciekłego otrzymanego z różnych rodzajów odpadów z tworzyw sztucznych mierzono zgodnie ze standardową metodą ASTM D 240 przy użyciu kalorymetru bombowego (Parr 6200 Calorimeter), natomiast wytwarzanie gazu szacowano przy użyciu standardowej formuły bilansu masowego, uwzględniając różnicę mas oleju ciekłego i węgla drzewnego.
Wyniki i dyskusja
Analiza TGA substratów
TGA została przeprowadzona indywidualnie dla każdego rodzaju odpadów z tworzyw sztucznych w celu określenia optymalnej temperatury degradacji termicznej. Wszystkie rodzaje odpadów z tworzyw sztucznych wykazują podobne zachowanie degradacyjne z szybką utratą masy węglowodorów w wąskim zakresie temperatur (150-250°C) (rys. 2). Maksymalna degradacja dla każdego rodzaju odpadów tworzyw sztucznych została osiągnięta w zakresie 420-490°C. PS i PP wykazywały rozkład jednostopniowy, natomiast PE i PET rozkład dwustopniowy w kontrolowanych warunkach. Jednostopniowy rozkład odpowiada obecności wiązania węgiel-węgiel, które sprzyja mechanizmowi losowej rozpadu wraz ze wzrostem temperatury (Kim et al., 2006). Degradacja PP rozpoczęła się w bardzo niskiej temperaturze (240°C) w porównaniu z innymi surowcami. Połowa węgla obecnego w łańcuchu PP składa się z węgla trzeciorzędowego, co sprzyja tworzeniu się karbokationów podczas procesu jego degradacji termicznej (Jung i in., 2010). Jest to prawdopodobnie przyczyna osiągnięcia maksymalnej degradacji PP w niższej temperaturze. Początkowa degradacja PS rozpoczęła się w temperaturze 330°C, a maksymalną degradację osiągnięto w temperaturze 470°C. PS ma strukturę cykliczną, a jego degradacja w warunkach termicznych obejmuje zarówno przypadkowe rozerwanie łańcucha, jak i łańcucha końcowego, co potęguje proces jego degradacji (Demirbas, 2004; Lee, 2012).
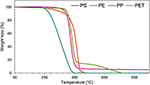
Rysunek 2. Analiza termograwimetryczna (TGA) odpadów z tworzyw sztucznych PS, PE, PP i PET.
PE i PET wykazywały dwuetapowy proces rozkładu; początkowa degradacja rozpoczynała się w niższych temperaturach, po czym następował drugi etap degradacji w wyższej temperaturze. Początkowa degradacja PE rozpoczęła się w temperaturze 270°C i postępowała powoli, ale stopniowo, aż do osiągnięcia temperatury 385°C. Po tej temperaturze zaobserwowano gwałtowną degradację, a 95% degradację osiągnięto przy dalszym wzroście temperatury o około 100°C. Podobny dwuetapowy przebieg degradacji zaobserwowano w przypadku tworzywa PET, a początkowa degradacja rozpoczęła się w temperaturze 400°C z gwałtownym spadkiem utraty masy. Jednakże, druga degradacja rozpoczęła się w nieco wyższej temperaturze (550°C). Początkowa degradacja PE i PET może być spowodowana obecnością pewnych lotnych zanieczyszczeń, takich jak wypełniacz dodatków stosowanych podczas syntezy tworzyw sztucznych (Dimitrov i in., 2013).
Różni badacze donosili, że degradacja PE i PET wymaga wyższych temperatur w porównaniu z innymi tworzywami sztucznymi (Dimitrov i in., 2013; Rizzarelli i in., 2016). Lee (2012) podał, że PE ma długołańcuchową, rozgałęzioną strukturę i jego degradacja zachodzi poprzez losowe rozerwanie łańcucha, co wymaga wyższej temperatury, podczas gdy degradacja PET następuje poprzez losowe rozerwanie ogniw estrowych, co prowadzi do powstania oligomerów (Dziecioł i Trzeszczynski, 2000; Lecomte i Liggat, 2006). Początkowa degradacja PET była być może spowodowana obecnością pewnych lotnych zanieczyszczeń, takich jak glikol dietylenowy (Dimitrov i in., 2013). Literatura podaje, że obecność tych lotnych zanieczyszczeń dodatkowo sprzyja procesowi degradacji polimerów (McNeill i Bounekhel, 1991; Dziecioł i Trzeszczyński, 2000). Różnice w krzywych TGA różnych rodzajów tworzyw sztucznych mogą wynikać z ich mezoporowatej struktury (Chandrasekaran i in., 2015). Ponadto, Lopez i wsp. (2011) podali, że zastosowanie katalizatorów obniża temperaturę procesu. Dlatego za optymalną temperaturę, w obecności aktywowanego NZ, można przyjąć 450°C dla katalitycznej pirolizy wspomnianych odpadów z tworzyw sztucznych.
Effect of Feedstock and Catalysts on Pyrolysis Products Yield
Badano wpływ termicznej i kwasowej aktywacji NZ na wydajność produktu procesu pirolizy (rys. 3). Katalityczna piroliza pojedynczych tworzyw sztucznych PS przy użyciu katalizatorów TA-NZ i AA-NZ wykazała najwyższą wydajność oleju ciekłego, wynoszącą odpowiednio 70 i 60%, w porównaniu do wszystkich innych badanych rodzajów pojedynczych i łączonych odpadów tworzyw sztucznych. Wysoka wydajność ciekłego oleju z katalitycznej pirolizy PS została również odnotowana w kilku innych badaniach (Siddiqui i Redhwi, 2009; Lee, 2012; Rehan et al., 2017). Siddiqui i Redhwi (2009) podali, że PS ma strukturę cykliczną, co prowadzi do wysokiej wydajności ciekłego oleju z katalitycznej pirolizy. Lee (2012) podał, że degradacja PS zachodzi zarówno na drodze rozpadu łańcucha przypadkowego, jak i końcowego, co prowadzi do wytworzenia stabilnej struktury pierścienia benzenowego, która wspomaga dalsze krakowanie i może zwiększyć produkcję oleju ciekłego. Ponadto, w obecności katalizatorów kwasowych, degradacja PS przebiegała według mechanizmu karbenowego, który dalej ulegał uwodornieniu (międzycząsteczkowe/wewnątrzcząsteczkowe przeniesienie wodoru) i rozszczepieniu β (Serrano et al., 2000). Ponadto, degradacja PS zachodziła w niższej temperaturze, w porównaniu z innymi tworzywami sztucznymi, takimi jak PE, ze względu na jego cykliczną strukturę (Wu i in., 2014). Z drugiej strony, w wyniku katalitycznej pirolizy PS uzyskano większą ilość węgla drzewnego (24,6%) z katalizatorem AA-NZ niż z katalizatorem TA-NZ (15,8%). Ma i wsp. (2017) również odnotowali wysoką produkcję węgla drzewnego z katalitycznej pirolizy PS z katalizatorem z zeolitu kwaśnego (Hβ). Wysokie liczby produkcji węgli wynikały z wysokiej kwasowości katalizatora, która sprzyja produkcji węgli poprzez intensywne reakcje wtórnego sieciowania (Serrano et al., 2000).
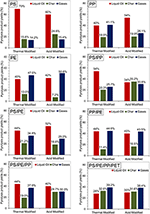
Rysunek 3. Wpływ TA-NZ i AA-NZ na wydajność produktu pirolizy.
W wyniku katalitycznej pirolizy PP uzyskano więcej ciekłego oleju (54%) przy użyciu katalizatora AA-NZ niż katalizatora TA-NZ (40%) (rys. 3). Z drugiej strony, katalizator TA-NZ produkował duże ilości gazu (41,1%), co może być spowodowane niższą aktywnością katalityczną katalizatora TA-NZ. Według Kim i wsp. (2002) katalizator o niskiej kwasowości i powierzchni BET o strukturze mikroporowatej sprzyja początkowej degradacji PP, co może prowadzić do maksymalnej produkcji gazów. Obali i wsp. (2012) przeprowadzili pirolizę PP z użyciem katalizatora glinowego i odnotowali maksymalną produkcję gazu. Ponadto, tworzenie się karbokacji podczas degradacji PP, ze względu na obecność trzeciorzędowego węgla w jego łańcuchu węglowym, może również sprzyjać produkcji gazu (Jung i in., 2010). Syamsiro i wsp. (2014) podali również, że piroliza katalityczna PP i PS z udziałem katalizatora z naturalnego zeolitu aktywowanego kwasem (HCL) produkowała więcej gazów niż proces z udziałem katalizatora z naturalnego zeolitu aktywowanego termicznie, ze względu na jego wysoką kwasowość i powierzchnię BET.
Piroliza katalityczna PE z udziałem katalizatorów TA-NZ i AA-NZ produkowała podobne ilości ciekłego oleju (40 i 42%). Jednak największe ilości gazów (50,8 i 47,0%) wytworzono z PE przy użyciu odpowiednio AA-NZ i TA-NZ w porównaniu do wszystkich innych badanych rodzajów tworzyw sztucznych. Produkcja węgla drzewnego była w tym przypadku najniższa i wynosiła odpowiednio 7,2 i 13,0% w przypadku AA-NZ i TA-NZ. W różnych badaniach odnotowano również niższą produkcję węgla drzewnego z katalitycznej pirolizy PE (Xue et al., 2017). Lopez et al. (2011) podali, że katalizatory o wysokiej kwasowości zwiększają pękanie polimerów podczas katalitycznej pirolizy. Wzrost krakingu, w obecności katalizatora o wysokiej kwasowości, sprzyja produkcji gazów (Miandad et al., 2016b, 2017a). Zeaiter (2014) przeprowadził katalityczną pirolizę PE z użyciem zeolitu HBeta i odnotował produkcję gazu na poziomie 95,7% dzięki wysokiej kwasowości katalizatora. Batool i wsp. (2016) również odnotowali maksymalną produkcję gazu z katalitycznej pirolizy PE, przy zastosowaniu silnie kwaśnego katalizatora ZSM-5. Według Lee (2012) i Williamsa (2006), PE ma strukturę węglową o długim łańcuchu, a jego degradacja zachodzi losowo na mniejsze cząsteczki łańcuchowe poprzez losowe rozszczepienie łańcucha, co może sprzyjać produkcji gazu. Podczas pirolizy PE, który posiada tylko wiązania C-H i C-C, początkowo dochodzi do rozerwania szkieletu makrocząsteczki, co prowadzi do powstania stabilnych wolnych rodników. Następnie zachodziły etapy uwodornienia, prowadzące do syntezy wtórnych wolnych rodników (nowe stabilne wiązanie C-H), co skutkowało rozszczepieniem β i wytworzeniem grupy nienasyconej (Rizzarelli i in., 2016).
Katalityczna piroliza PP/PE (stosunek 50/50%) nie wykazała znaczącej różnicy w ogólnej wydajności produktu przy zastosowaniu zarówno AA-NZ jak i TA-NZ. Uzysk oleju ciekłego z katalitycznej pirolizy PP/PE wynosił odpowiednio 44 i 40% w przypadku katalizatorów TA-NZ i AA-NZ. Niewielki spadek wydajności ciekłego oleju z AA-NZ może być spowodowany jego wysoką kwasowością. Syamsiro i wsp. (2014) podali, że AA-NZ z HCl ma wysoką kwasowość w porównaniu do TA-NZ, produkował mniejszą wydajność oleju ciekłego i miał wysoką produkcję gazów. Ogólna piroliza katalityczna PP/PE produkowała maksymalną ilość gazu przy niewielkich ilościach węgla drzewnego. Wysoka produkcja gazu może być spowodowana obecnością PP. Degradacja PP wzmaga proces karbokacji ze względu na obecność trzeciorzędowego węgla w jego łańcuchu węglowym (Jung et al., 2010). Ponadto, degradacja PE w obecności katalizatora również sprzyja produkcji gazu z niską wydajnością oleju ciekłego. Jednakże, gdy pirolizę katalityczną PP i PE prowadzono oddzielnie z PS, zaobserwowano znaczącą różnicę w wydajności produktu.
W przypadku pirolizy katalitycznej PS/PP (w stosunku 50/50%) z katalizatorami TA-NZ i AA-NZ zaobserwowano znaczącą różnicę w wydajności oleju ciekłego wynoszącą odpowiednio 54 i 34%. Podobnie, zaobserwowano znaczącą różnicę w uzysku węgla drzewnego wynoszącą 20,3 i 35,2%, natomiast wysoki uzysk gazów wynosił 25,7 i 30,8% przy zastosowaniu katalizatorów TA-NZ i AA-NZ, odpowiednio. Lopez et al. (2011) oraz Seo et al. (2003) podali, że katalizator o wysokiej kwasowości promuje proces krakingu i daje maksymalną produkcję gazu. Ponadto, obecność PP również zwiększa produkcję gazu ze względu na proces karbokacji podczas degradacji (Jung et al., 2010). Kim et al. (2002) podali, że degradacja PP powoduje maksymalne wytwarzanie gazu w obecności katalizatorów kwasowych.
Katalityczna piroliza PS z PE (stosunek 50/50%) w obecności katalizatora TA-NZ dała 44% ciekłego oleju, jednakże 52% ciekłego oleju uzyskano stosując katalizator AA-NZ. Kiran i in. (2000) przeprowadzili pirolizę PS z PE w różnych proporcjach i stwierdzili, że wzrost stężenia PE powoduje zmniejszenie stężenia ciekłego oleju wraz ze wzrostem stężenia gazu. Obecność PS z PE sprzyja procesowi degradacji ze względu na wytwarzanie aktywnego stabilnego pierścienia benzenowego z PS (Miandad et al., 2016b). Wu i wsp. (2014) przeprowadzili TGA PS z PE i zaobserwowali dwa piki, pierwszy dla PS w niskiej temperaturze, a następnie degradację PE w wysokiej temperaturze. Co więcej, degradacja PE przebiega zgodnie z procesem łańcuchowym wolnorodnikowym i procesem uwodornienia, podczas gdy PS przebiega zgodnie z procesem łańcuchowym rodnikowym obejmującym różne etapy (Kiran i in., 2000). Tak więc, nawet biorąc pod uwagę zjawiska degradacji, PS ulegało większej degradacji w porównaniu z PE i wytwarzało stabilne pierścienie benzenowe (McNeill i in., 1990).
Katalityczna piroliza PS/PE/PP (stosunek 50/25/25%) wykazała nieco niższą wydajność oleju ciekłego w porównaniu z pirolizą katalityczną wszystkich poszczególnych rodzajów tworzyw sztucznych. Uzysk oleju z obu katalizatorów, TA-NZ i AA-NZ, jest w tym przypadku podobny i wynosi odpowiednio 44 i 40%. Produkcja węgla drzewnego była wyższa (29,7%) w przypadku katalizatora AA-NZ niż (19,0%) w przypadku katalizatora TA-NZ, co może być spowodowane reakcjami polimeryzacji (Wu i Williams, 2010). Ponadto, dodatek PET do PS, PE i PP (w stosunku 20/40/20/20%) zmniejszył uzysk oleju ciekłego do 28 i 30% przy zastosowaniu katalizatorów TA-NZ i AA-NZ, przy czym frakcje węgla drzewnego i gazu były wyższe. Demirbas (2004) przeprowadził pirolizę PS/PE/PP i odnotował podobne wyniki dla wydajności produktu. Adnan et al. (2014) przeprowadzili katalityczną pirolizę PS i PET przy użyciu katalizatora Al-Al2O3 w proporcjach 80/20% i odnotowali tylko 37% ciekłego oleju. Ponadto, Yoshioka et al. (2004) odnotowali maksymalną produkcję gazu i węgla drzewnego przy znikomej produkcji oleju ciekłego z katalitycznej pirolizy PET. Ponadto, maksymalna produkcja węgla drzewnego została również odnotowana, gdy katalityczna piroliza PET została przeprowadzona z innymi tworzywami sztucznymi (Bhaskar et al., 2004). Wyższa produkcja węgla drzewnego z pirolizy PET wynikała z reakcji karbonizacji i kondensacji zachodzących podczas pirolizy w wysokiej temperaturze (Yoshioka i in., 2004). Dodatkowo, obecność atomu tlenu również sprzyja wysokiej produkcji węgli z katalitycznej pirolizy PET (Xue i in., 2017). Thilakaratne i wsp. (2016) podali, że produkcja wolnych od benzenu rodników, z dwoma aktywowanymi węglami, jest prekursorem katalitycznego koksu z degradacji PET.
Effect of Catalysts on the Composition of Liquid Oil
Skład chemiczny ciekłego oleju powstałego w wyniku katalitycznej pirolizy różnych odpadów z tworzyw sztucznych przy użyciu katalizatorów TA-NZ i AA-NZ scharakteryzowano metodą GC-MS (rys. 4, 5). Na skład wytworzonego oleju ciekłego mają wpływ różne rodzaje substratów i katalizatorów zastosowanych w procesie pirolizy (Miandad i in., 2016a,b,c). Ciekły olej wytworzony z poszczególnych rodzajów tworzyw sztucznych takich jak PS, PP i PE zawierał mieszaninę związków aromatycznych, alifatycznych i innych węglowodorów. Zawartość związków aromatycznych w oleju z PS i PE była wyższa niż z PP z zastosowaniem katalizatora TA-NZ. Zawartość związków aromatycznych wzrosła w oleju z PS i PP, a zmalała w PE przy zastosowaniu katalizatora AA-NZ. Mezoporowaty i kwaśny katalizator prowadzi do produkcji węglowodorów o krótszym łańcuchu ze względu na wysoką zdolność do krakingu (Lopez i in., 2011). Natomiast katalizatory mikroporowate i mniej kwaśne sprzyjają produkcji węglowodorów o długim łańcuchu, ponieważ proces krakingu zachodził tylko na zewnętrznej powierzchni katalizatorów. Ogólnie rzecz biorąc, w obecności katalizatorów, PE i PP podlegają mechanizmowi rozszczepiania łańcucha przypadkowego, podczas gdy PS podlega mechanizmowi rozpinania lub rozszczepiania łańcucha końcowego (Cullis i Hirschler, 1981; Peterson i in., 2001). Rozszczepienie łańcucha końcowego powoduje produkcję monomerów, podczas gdy losowe rozszczepienie łańcucha powoduje produkcję oligomerów i monomerów (Peterson i in., 2001).
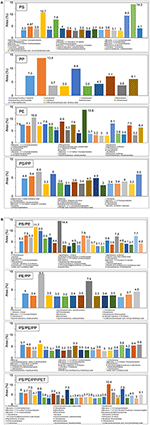
Rysunek 4. (A,B) GC-MS ciekłego oleju wytworzonego z różnych rodzajów odpadów z tworzyw sztucznych przy użyciu TA-NZ.
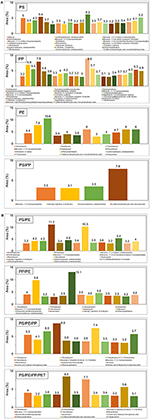
Rysunek 5. (A,B) GC-MS ciekłego oleju wytworzonego z różnych rodzajów odpadów z tworzyw sztucznych przy użyciu AA-NZ.
Ciekły olej wytworzony z katalitycznej pirolizy PE, przy użyciu obu katalizatorów, produkował głównie naftalen, fenantren, naftalen, 2-etenylo-, 1-pentadeken, antracen, 2-metylo-, heksadekan i tak dalej (Rysunki 4A, 5A). Wyniki te zgadzają się z kilkoma innymi badaniami (Lee, 2012; Xue i in., 2017). Produkcja pochodnej benzenu ujawnia, że TA-NZ wzmacnia proces aromatyzacji w porównaniu do AA-NZ. Xue et al. (2017) donoszą, że pośrednie olefiny powstające z katalitycznej pirolizy PE, ulegają dalszej aromatyzacji wewnątrz porów katalizatorów. Niemniej jednak, reakcja aromatyzacji prowadzi dalej do wytworzenia atomów wodoru, które mogą wzmocnić proces aromatyzacji. Lee (2012) doniósł, że ZSM-5 produkował więcej związków aromatycznych w porównaniu z katalizatorem mordenitowym, ze względu na jego krystaliczną strukturę.
Istnieją dwa możliwe mechanizmy, które mogą wiązać się z degradacją PE w obecności katalizatora; hybrydowa abstrakcja jonów ze względu na obecność miejsc Lewisa lub, ze względu na mechanizm jonów karbenowych poprzez dodanie protonu (Rizzarelli et al., 2016). Początkowo degradacja rozpoczyna się na zewnętrznej powierzchni katalizatorów, a następnie postępuje z dalszą degradacją w wewnętrznych porach katalizatorów (Lee, 2012). Mikroporowate katalizatory utrudniają jednak wnikanie większych cząsteczek i dlatego w wyniku katalitycznej pirolizy PE z użyciem mikroporowatych katalizatorów powstają związki o wyższych łańcuchach węglowych. Ponadto, w obecności katalizatorów kwaśnych, ze względu na mechanizm karbenowy, może wzrosnąć produkcja związków aromatycznych i olefinowych (Lee, 2012). Lin et al. (2004) donoszą o produkcji wysoko reaktywnych olefin, jako produktów pośrednich podczas katalitycznej pirolizy PE, co może sprzyjać produkcji parafin i związków aromatycznych w produkowanym oleju ciekłym. Ponadto, obecność kwaśnego katalizatora i wolnego atomu wodoru może prowadzić do alkilacji toluenu i benzenu, przekształcając pośredni alkilowany benzen do produkcji naftalenu w wyniku aromatyzacji (Xue et al., 2017).
Ciekły olej wytworzony z katalitycznej pirolizy PS z TA-NZ i AA-NZ, zawiera różnego rodzaju związki. Alfa-metylostyren, benzen, 1,1′-(2-butene-1,4-diyl)bis-, bibenzyl, benzen, (1,3-propanediyl), fenantren, 2-fenylonaftalen i tak dalej były głównymi związkami znalezionymi w wyprodukowanym ciekłym oleju (Rysunki 4A, 5A). Ciekły olej otrzymany z katalitycznej pirolizy PS, przy użyciu obu aktywowanych katalizatorów, zawiera głównie węglowodory aromatyczne z pewną ilością parafin, naftalenu i związków olefinowych (Rehan et al., 2017). Jednak w obecności katalizatora uzyskano maksymalną produkcję związków aromatycznych (Xue i in., 2017). Ramli et al. (2011) również donosili o produkcji olefin, naftalenu ze związkami aromatycznymi z katalitycznej pirolizy PS przy użyciu katalizatorów Al2O3, wspomaganych Cd i Sn. Degradacja PS rozpoczyna się od pękania na zewnętrznej powierzchni katalizatora, po czym następuje reforming wewnątrz porów katalizatora (Uemichi i in., 1999). Początkowo, pękanie polimeru jest prowadzone przez miejsce kwasu Lewisa na powierzchni katalizatorów w celu wytworzenia karbokationowych intermediatów, które dalej odparowują lub ulegają reformingowi wewnątrz porów katalizatora (Xue et al., 2017).
Katalityczna piroliza PS głównie wytwarza styren i jego pochodne jako główne związki w wytworzonym ciekłym oleju (Siddiqui i Redhwi, 2009; Rehan et al., 2017). Konwersja styrenu do jego pochodnej była zwiększona w obecności protonowanych katalizatorów w wyniku uwodornienia (Kim i in., 2002). Shah i Jan (2015) oraz Ukei i wsp. (2000) podali, że uwodornienie styrenu wzrastało wraz ze wzrostem temperatury reakcji. Ogawa et al. (1982) przeprowadzili pirolizę PS z katalizatorem glinowo-krzemionkowym w temperaturze 300°C i stwierdzili uwodornienie styrenu do jego pochodnej. Ramli et al. (2011) przedstawili możliwy mechanizm degradacji PS na katalizatorach kwasowych, który może zachodzić w wyniku ataku protonu związanego z miejscami kwasowymi Bronsteda, w wyniku czego powstaje mechanizm jonu karbenowego, który dalej ulega rozszczepieniu β, a następnie następuje przeniesienie wodoru. Ponadto, reakcja sieciowania była faworyzowana przez silne miejsca kwasowe Bronsteda i kiedy ta reakcja wystąpiła, całkowite krakowanie może zmniejszyć się do pewnego stopnia i zwiększyć produkcję węgla drzewnego (Serrano et al., 2000). Co więcej, katalizatory krzemionkowo-aluminiowe nie posiadają silnych miejsc kwasowych Bronsteda, choć może to nie poprawiać reakcji sieciowania, ale sprzyjać procesowi uwodornienia. Może to być zatem przyczyną, że w ciekłym oleju nie stwierdzono obecności styrenu, jednak jego pochodna została wykryta w dużych ilościach (Lee et al., 2001). Xue i wsp. (2017) donoszą również o dealkilacji styrenu, spowodowanej opóźnieniem odparowania wewnątrz reaktora, co może prowadzić do intensyfikacji procesu reformingu i skutkować wytworzeniem pochodnej styrenu. TA-NZ i AA-NZ zawierają dużą ilość tlenku glinu i krzemionki, które prowadzą do uwodornienia styrenu do jego pochodnej, co skutkuje produkcją monomerów styrenu zamiast styrenu.
W wyniku katalitycznej pirolizy PP powstała złożona mieszanina ciekłego oleju zawierająca związki aromatyczne, olefinowe i naftalenowe. Benzen, 1,1′-(2-butene-1,4-diyl)bis-, benzen, 1,1′-(1,3-propanediyl)bis-, antracen, 9-metylo-, naftalen, 2-fenylo-, 1,2,3,4-tetrahydro-1-fenylo-, naftalen, fenantren itd. były głównymi związkami znalezionymi w ciekłym oleju (Rysunki 4A, 5A). Wyniki te są zgodne z wynikami innych badań, w których przeprowadzono katalityczną pirolizę PP przy użyciu różnych katalizatorów (Marcilla i in., 2004). Ponadto, degradacja PP przy użyciu AA-NZ spowodowała maksymalną produkcję związków fenolowych. Wyższa produkcja była prawdopodobnie spowodowana obecnością miejsc o wysokiej kwasowości, gdyż sprzyja ona produkcji związków fenolowych. Ponadto, obecność miejsc o wysokiej kwasowości na katalizatorze wzmacnia mechanizm oligomeryzacji, aromatyzacji i deoksygenacji, co prowadzi do produkcji związków poli-aromatycznych i naftalenowych. Dawood i Miura (2002) również donieśli o wysokiej produkcji tych związków z katalitycznej pirolizy PP z użyciem wysokokwasowego modyfikowanego HY-zeolitu.
Skład oleju z katalitycznej pirolizy PP z PE zawiera związki występujące w oleju z obu poszczególnych substratów typu tworzywa sztucznego. Miandad i wsp. (2016b) podali, że skład surowca wpływa również na jakość i skład chemiczny oleju. Wytworzony ciekły olej z katalitycznej pirolizy PE/PP zawiera związki aromatyczne, olefinowe i naftalenowe. Głównymi znalezionymi związkami były: benzen, 1,1′-(1,3-propanediyl)bis-, mono(2-etyloheksyl) ester, kwas 1,2-benzenodikarboksylowy, antracen, pentadekan, fenantren, 2-fenyloftalen i tak dalej (Rysunki 4B, 5B). Jung et al. (2010) podali, że produkcja aromatów w wyniku katalitycznej pirolizy PP/PE może przebiegać zgodnie z mechanizmem reakcji Dielsa-Aldera, po której następuje dehydrogenacja. Ponadto, w wyniku katalitycznej pirolizy PP i PE prowadzonej oddzielnie z PS, wytwarzane są głównie związki aromatyczne ze względu na obecność PS. Ciekły olej wytwarzany z PS/PP zawiera benzen, 1,1′-(1,3-propanodiyl)bis, kwas 1,2-benzenodikarboksylowy, ester disooktylowy, bibenzyl, fenantren, 2-fenylonaftalen, benzen, (4-metylo-1-decenylo)- i tak dalej (rys. 4A, 5A). W wyniku pirolizy katalitycznej PS z PE otrzymywano głównie ciekły olej, którego głównymi składnikami były azulen, naftalen, 1-metylo-, naftalen, 2-etenyl, benzen, 1,1′-(1,3-propanodiyl)bis-, fenantren, 2-fenylonaftalen, benzen, 1,1′-(1-metylo-1,2-etanodiyl)bis- i kilka innych związków (rys. 4B, 5B). Miskolczi i wsp. (2006) przeprowadzili pirolizę PS z PE o stosunku odpowiednio 10 i 90% i odnotowali maksymalną produkcję związków aromatycznych nawet przy bardzo niskim stosunku PS. Miandad et al. (2016b) podali, że termiczna piroliza PE z PS bez katalizatora, spowodowała konwersję PE do ciekłego oleju o wysokim składzie aromatów. Natomiast piroliza termiczna samego PE bez katalizatora przekształcała go w wosk zamiast ciekłego oleju ze względu na silnie rozgałęzioną strukturę długołańcuchową (Lee, 2012; Miandad i in., 2016b). Wu i wsp. (2014) przeprowadzili TGA PS z PE i podali, że obecność PS sprzyja degradacji PE, ze względu na wytwarzanie stabilnych pierścieni benzenowych.
Skład chemiczny oleju pirolitycznego, według różnych grup funkcyjnych, badano metodą FT-IR. Uzyskane dane wykazały obecność w oleju aromatycznych i alifatycznych grup funkcyjnych (rys. 6, 7). W większości ciekłych olejów otrzymanych przy użyciu obu katalizatorów zaobserwowano bardzo silny pik przy 696 cm-1 , co odpowiada dużej koncentracji związków aromatycznych. Kolejne dwa piki, które są oczywiste, widoczne były przy ok. 1.456 i 1.495 cm-1 dla C-C z wiązaniami pojedynczymi i podwójnymi, odpowiadającymi związkom aromatycznym. Ponadto, na końcu widma, we wszystkich olejach ciekłych, z wyjątkiem PS, zaobserwowano silne piki przy 2,850, 2,923 i 2,958 cm-1 , odpowiadające rozciągowi C-H związków alkanowych. Ogólnie rzecz biorąc, ciekły olej otrzymany w wyniku katalitycznej pirolizy różnych odpadów z tworzyw sztucznych przy użyciu katalizatora AA-NZ wykazywał więcej pików niż próbki z katalizatorów TA-NZ. Te dodatkowe piki odpowiadały związkom aromatycznym, alkanom i alkenom. Wskazuje to, że, zgodnie z oczekiwaniami, AA-NZ miał lepsze właściwości katalityczne niż TA-NZ. Różni badacze podawali podobne wyniki, że w oleju ciekłym otrzymanym z PS dominowały związki aromatyczne. Tekin et al. (2012) oraz Panda i Singh (2013) również donosili o obecności aromatów z niektórymi alkanami i alkenami z katalitycznej pirolizy PP. Kunwar i wsp. (2016) przeprowadzili termiczną i katalityczną pirolizę PE i donieśli, że wytworzony ciekły olej zawierał alkany i alkeny jako główne grupy funkcyjne. Ogólnie rzecz biorąc, analiza FT-IR zapewniła większy wgląd w skład chemiczny wytworzonego ciekłego oleju, z katalitycznej pirolizy różnych odpadów z tworzyw sztucznych, przy użyciu zmodyfikowanych katalizatorów NZ i dodatkowo potwierdziła nasze wyniki GC-MS.
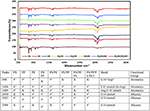
Rysunek 6. Analiza FT-IR ciekłego oleju otrzymanego z katalitycznej pirolizy z TA-NZ.
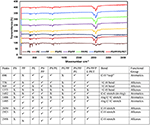
Rysunek 7. Analiza FT-IR ciekłego oleju otrzymanego w wyniku katalitycznej pirolizy z AA-NZ.
Potencjalne zastosowania produktów pirolizy
Ciekły olej otrzymany w wyniku katalitycznej pirolizy różnych rodzajów substratów z tworzyw sztucznych zawiera dużą liczbę związków aromatycznych, olefinowych i naftalenowych, które występują w produktach naftowych. Ponadto wartość HHV wytworzonego oleju ciekłego mieści się w zakresie 41,7-44,2 MJ/kg (tabela 2), co jest wartością bardzo zbliżoną do wartości energetycznej konwencjonalnego oleju napędowego. Najniższą wartość HHV wynoszącą 41,7 MJ/kg stwierdzono dla oleju ciekłego otrzymanego z PS przy użyciu katalizatora TA-NZ, natomiast najwyższą wartość HHV wynoszącą 44,2 MJ/kg uzyskano z PS/PE/PP przy użyciu katalizatora AA-NZ. Tak więc ciekły olej z pirolizy otrzymany z różnych odpadów tworzyw sztucznych ma potencjał do wykorzystania jako alternatywne źródło energii. Według Lee et al. (2015) oraz Rehan et al. (2016), produkcja energii elektrycznej jest możliwa do osiągnięcia przy zastosowaniu ciekłego oleju z pirolizy w silniku Diesla. Saptoadi i Pratama (2015) z powodzeniem wykorzystali ciekły olej pirolityczny jako alternatywę w piecu naftowym. Ponadto, wytworzone związki aromatyczne mogą być wykorzystane jako surowiec do polimeryzacji w różnych gałęziach przemysłu chemicznego (Sarker i Rashid, 2013; Shah i Jan, 2015). Ponadto, różni badacze wykorzystali wyprodukowany olej ciekły jako paliwo transportowe po zmieszaniu z konwencjonalnym olejem napędowym w różnych proporcjach. Badania przeprowadzono w celu poznania potencjału produkowanego oleju ciekłego w kontekście osiągów silnika i emisji spalin pojazdu. Nileshkumar et al. (2015) oraz Lee et al. (2015) podali, że proporcje mieszanki 20:80% pirolitycznego oleju ciekłego i konwencjonalnego oleju napędowego, odpowiednio, dały podobne wyniki osiągów silnika jak konwencjonalny olej napędowy. Ponadto, przy tym samym stosunku mieszanki, emisja spalin była również podobna, jednakże emisja spalin wzrastała wraz ze wzrostem ilości mieszanki oleju pirolitycznego (Frigo i in., 2014; Mukherjee i Thamotharan, 2014).
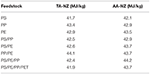
Tabela 2. High Heating Values (HHV) oleju do pirolizy z różnych substratów przy użyciu katalizatorów TA-NZ i AA-NZ.
Resztki (węgiel drzewny) pozostałe po procesie pirolizy mogą być wykorzystane do kilku zastosowań środowiskowych. Kilku badaczy aktywowało węgiel drzewny poprzez aktywację parową i termiczną (Lopez i in., 2009; Heras i in., 2014). Proces aktywacji zwiększył powierzchnię BET i zmniejszył wielkość porów węgla drzewnego (Lopez i in., 2009). Ponadto, Bernando (2011) ulepszył plastikowy węgiel drzewny biomateriałem i przeprowadził adsorpcję (3,6-22,2 mg/g) niebieskiego barwnika metylenowego ze ścieków. Miandad et al. (2018) wykorzystali węgiel drzewny uzyskany z pirolizy odpadów z tworzyw sztucznych PS do syntezy nowatorskiego nanoadsorbentu węglowo-metalowego z podwójną warstwą tlenków (C/MnCuAl-LDOs) do adsorpcji czerwieni Kongo (CR) w ściekach. Ponadto, węgiel drzewny może być wykorzystany jako surowiec do produkcji węgla aktywnego.
Limitations of GC-MS Analysis of Pyrolysis Oil
Istnieją pewne ograniczenia w prowadzeniu dokładnej analizy ilościowej składników chemicznych w oleju z pirolizy przy użyciu GC-MS. W tym badaniu wykorzystano procentowy udział masowy różnych związków chemicznych występujących w próbkach oleju, obliczony na podstawie powierzchni pików zidentyfikowanych przez kolumnę DP5-MS z fazą normalną i FID. Zidentyfikowane piki zostały dopasowane do biblioteki widm NIST i banku mas. Wyboru związków dokonano na podstawie wskaźnika podobieństwa (SI > 90%). Dalsze porównanie ze znanymi wzorcami (CRM) pozwoliło na potwierdzenie zidentyfikowanych związków. Zastosowana kolumna i detektory były ograniczone jedynie do węglowodorów. W rzeczywistości jednak olej z większości odpadów tworzyw sztucznych ma złożoną strukturę chemiczną i może zawierać inne grupy niezidentyfikowanych związków chemicznych, takich jak węglowodory zawierające siarkę, azot i tlen. Dlatego też potrzebna jest bardziej dogłębna i dokładna jakościowa analiza chemiczna, aby w pełni zrozumieć chemię oleju z pirolizy, przy użyciu zaawansowanej kalibracji i standaryzacji oraz przy użyciu różnych detektorów MS, takich jak SCD i NCD, jak również różnych kolumn GC.
Potencjał i wyzwania biorafinerii opartych na pirolizie
Bioreinerie odpadów przyciągają ogromną uwagę jako rozwiązanie do przekształcania odpadów MSW i innych odpadów biomasy w szereg produktów, takich jak paliwa, energia, ciepło i inne cenne chemikalia i materiały. Różne typy biorafinerii, takie jak biorafineria oparta na rolnictwie, biorafineria odpadów zwierzęcych, biorafineria ścieków, biorafineria oparta na algach, rafineria odpadów z tworzyw sztucznych, biorafineria oparta na leśnictwie, biorafineria odpadów przemysłowych i biorafineria odpadów spożywczych itp. mogą być rozwijane w zależności od rodzaju i źródła odpadów (Gebreslassie i in., 2013; De Wild i in., 2014; Nizami i in., 2017a,b; Waqas i in., 2018). Te biorafinerie mogą odegrać znaczącą rolę w zmniejszeniu zanieczyszczenia środowiska związanego z odpadami i emisji gazów cieplarnianych. Ponadto generują one znaczne korzyści ekonomiczne i mogą pomóc w osiągnięciu gospodarki cyrkularnej w każdym kraju.
Biorefineria oparta na pirolizie może zostać opracowana w celu przetworzenia szeregu odpadów biomasy i odpadów z tworzyw sztucznych w celu wytworzenia paliw płynnych i gazowych, energii, biocharu i innych chemikaliów o wyższej wartości przy użyciu zintegrowanego podejścia. Zintegrowane podejście pomaga osiągnąć maksymalne korzyści ekonomiczne i środowiskowe przy minimalnej produkcji odpadów. Istnieje wiele wyzwań i możliwości poprawy w biorafineriach opartych na pirolizie, które muszą zostać podjęte i zoptymalizowane, aby zapewnić maksymalne korzyści. Chociaż olej z pirolizy zawiera więcej energii niż węgiel i niektóre inne paliwa, piroliza sama w sobie jest procesem energochłonnym, a produkt olejowy wymaga więcej energii do rafinacji (Inman, 2012). Oznacza to, że olej z pirolizy może nie być dużo lepszy od konwencjonalnego oleju napędowego lub innych paliw kopalnych pod względem emisji gazów cieplarnianych, choć aby to potwierdzić, potrzebne są szczegółowe badania nad bilansem masy i energii w całym procesie. Aby przezwyciężyć te wymagania energetyczne procesu, można opracować bardziej zaawansowane technologie wykorzystujące integrację energii odnawialnych, takich jak energia słoneczna lub wodna, z biorafineriami opartymi na pirolizie, w celu osiągnięcia maksymalnych korzyści ekonomicznych i środowiskowych.
Dostępność odpadów z tworzyw sztucznych i biomasy jako surowców dla biorafinerii opartych na pirolizie jest kolejnym poważnym wyzwaniem, ponieważ recykling nie jest obecnie zbyt wydajny, szczególnie w krajach rozwijających się. Gazy powstające w wyniku pirolizy niektórych odpadów z tworzyw sztucznych, takich jak PCW, są toksyczne i dlatego technologia oczyszczania emisji z pirolizy musi być dalej udoskonalana w celu osiągnięcia maksymalnych korzyści dla środowiska. Olej z pirolizy uzyskany z różnych rodzajów tworzyw sztucznych musi być znacznie oczyszczony przed jego użyciem w jakimkolwiek zastosowaniu, aby zapewnić minimalny wpływ na środowisko. Wysoka zawartość związków aromatycznych w oleju z pirolizy jest korzystna i niektóre związki aromatyczne, takie jak benzen, toluen i styren mogą być rafinowane i sprzedawane na już istniejącym rynku. Jednakże niektóre z węglowodorów aromatycznych są znanymi substancjami rakotwórczymi i mogą powodować poważne szkody dla zdrowia ludzkiego i środowiska. Należy zatem poważnie rozważyć tę kwestię.
Inne aspekty optymalizacji biorafinerii opartych na pirolizie, takie jak nowe pojawiające się zaawansowane katalizatory, w tym nanokatalizatory, muszą zostać opracowane i zastosowane w procesach pirolizy w celu zwiększenia jakości i wydajności produktów oraz optymalizacji całego procesu. Rynek dla produktów biorafinerii opartych na pirolizie powinien zostać stworzony/rozszerzony w celu przyciągnięcia dalszego zainteresowania i finansowania, aby uczynić tę koncepcję bardziej praktyczną i udaną. Podobnie należy bardziej skoncentrować się na prowadzeniu dalszych prac badawczych i rozwojowych w celu wzbogacenia koncepcji biorafinerii i wykorzystania jej prawdziwego potencjału. Ponadto konieczne jest przeprowadzenie szczegółowej oceny ekonomicznego i środowiskowego oddziaływania biorafinerii na etapie projektowania, z wykorzystaniem specjalistycznych narzędzi, takich jak ocena cyklu życia (LCA). LCA może przeanalizować oddziaływanie na środowisko biorafinerii i wszystkich produktów poprzez przeprowadzenie szczegółowych bilansów energetycznych i materiałowych wszystkich etapów życia, w tym wydobycia i przetwarzania surowców, produkcji, dystrybucji produktów, użytkowania, konserwacji oraz utylizacji/recyklingu. Wyniki LCA pomogą określić zrównoważony charakter biorafinerii, co jest kluczowe w podjęciu właściwej decyzji.
Wnioski
Piroliza katalityczna jest obiecującą techniką przekształcania odpadów z tworzyw sztucznych w ciekły olej i inne produkty o wartości dodanej, przy użyciu zmodyfikowanego katalizatora z zeolitu naturalnego (NZ). Modyfikację katalizatorów NZ przeprowadzono poprzez nowatorską aktywację termiczną (TA) i kwasową (AA), która poprawiła ich właściwości katalityczne. W wyniku katalitycznej pirolizy PS uzyskano najwięcej ciekłego oleju (70 i 60%) w porównaniu z PP (40 i 54%) oraz PE (40 i 42%), stosując odpowiednio katalizatory TA-NZ i AA-NZ. Skład chemiczny oleju poddanego pirolizie analizowano metodą GC-MS i stwierdzono, że większość ciekłego oleju zawiera dużą ilość związków aromatycznych z pewną ilością związków alifatycznych i innych węglowodorów. Wyniki te zostały dodatkowo potwierdzone przez analizę FT-IR, która wykazała wyraźne piki odpowiadające aromatycznym i innym węglowodorowym grupom funkcyjnym. Ponadto, olej ciekły otrzymany z różnych rodzajów odpadów tworzyw sztucznych charakteryzował się wyższą wartością opałową (HHV) w zakresie 41,7-44,2 MJ/kg, podobną do konwencjonalnego oleju napędowego. Dlatego też, po dalszej obróbce i rafinacji, olej ten może być potencjalnie wykorzystywany w różnych zastosowaniach energetycznych i transportowych. Niniejsze badania stanowią krok w kierunku rozwoju biorafinerii opartych na pirolizie. Biorefinerie mają duży potencjał do przekształcania odpadów w energię i inne wartościowe produkty i mogą pomóc w osiągnięciu gospodarki cyrkulacyjnej. Jednakże, istnieje wiele technicznych, operacyjnych i społeczno-ekonomicznych wyzwań, jak omówiono powyżej, które należy przezwyciężyć, aby osiągnąć maksymalne korzyści ekonomiczne i środowiskowe z biorafinerii.
Dostępność danych
Wszystkie zestawy danych wygenerowane dla tego badania są zawarte w manuskrypcie i/lub plikach uzupełniających.
Wkład Autorów
RM wykonał eksperymenty pirolizy i pomógł w napisaniu manuskryptu. HK, JD, JG i AH przeprowadzili szczegółową charakterystykę produktów procesu. MR i ASA przeanalizowali dane i napisali część manuskryptu. MAB, MR, i A-SN poprawili i zredagowali manuskrypt. ASA i IMII wsparli projekt finansowo i technicznie.
Oświadczenie o konflikcie interesów
Autorzy oświadczają, że badania zostały przeprowadzone przy braku jakichkolwiek komercyjnych lub finansowych powiązań, które mogłyby być interpretowane jako potencjalny konflikt interesów.
Podziękowania
MR i A-SN dziękują Center of Excellence in Environmental Studies (CEES), King Abdulaziz University (KAU), Jeddah, KSA i Ministry of Education, KSA za wsparcie finansowe w ramach Grant No. 2/S/1438. Autorzy są również wdzięczni Deanship of Scientific Research (DSR) w KAU za wsparcie finansowe i techniczne dla CEES.
Adnan, A., Shah, J., and Jan, M. R. (2014). Polystyrene degradation studies using Cu supported catalysts. J. Anal. Appl. Pyrol. 109, 196-204. doi: 10.1016/j.jaap.2014.06.013
CrossRef Full Text | Google Scholar
Aguado, J., Sotelo, J. L., Serrano, D. P., Calles, J. A., and Escola, J. M. (1997). Catalytic conversion of polyolefins into liquid fuels over MCM-41: comparison with ZSM-5 and amorphous SiO2-Al2O3. Ener fuels 11, 1225-1231. doi: 10.1021/ef970055v
CrossRef Full Text | Google Scholar
Alexandra, L. C. (2012). Municipal Solid Waste: Turning a Problem Into Resourceewaste: The Challenges Facing Developing Countries, Urban Specialist. Bank Światowy. 2-4 s.
Batool, M., Shah, A. T., Imran Din, M., and Li, B. (2016). Catalytic pyrolysis of low density polyethylene using cetyltrimethyl ammonium encapsulated monovacant keggin units and ZSM-5. J. Chem. 2016:2857162. doi: 10.1155/2016/2857162
CrossRef Full Text | Google Scholar
Bernando, M. (2011). „Physico-chemical characterization of chars produced in the co-pyrolysis of wastes and possible routes of valorization,” in Chemical Engineering (Lisboa: Universidade Nova de Lisboa), 27-36.
Bhaskar, T., Kaneko, J., Muto, A., Sakata, Y., Jakab, E., Matsui, T., et al. (2004). Pyrolysis studies of PP/PE/PS/PVC/HIPS-Br plastics mixed with PET and dehalogenation (Br, Cl) of the liquid products. J. Anal. Appl. Pyrolysis 72, 27-33. doi: 10.1016/j.jaap.2004.01.005
CrossRef Full Text | Google Scholar
Chandrasekaran, S. R., Kunwar, B., Moser, B. R., Rajagopalan, N., and Sharma, B. K. (2015). Katalityczny kraking termiczny odpadowych tworzyw sztucznych z odpadów pokonsumenckich do paliw. 1. Kinetyka i optymalizacja. Energy Fuels 29, 6068-6077. doi: 10.1021/acs.energyfuels.5b01083
CrossRef Full Text | Google Scholar
Cullis, C. F., and Hirschler, M. M. (1981). The Combustion of Organic Polymers. Vol. 5. London: Oxford University Press.
Dawood, A., and Miura, K. (2002). Catalytic pyrolysis of c-irradiated polypropylene (PP) over HY-zeolite for enhancing the reactivity and the product selectivity. Polym. Degrad. Stab. 76, 45-52. doi: 10.1016/S0141-3910(01)00264-6
CrossRef Full Text | Google Scholar
De Wild, P. J., Huijgen, W. J., and Gosselink, R. J. (2014). Lignin pyrolysis for profitable lignocellulosic biorefineries. Biofuels Bioprod. Biorefining 8, 645-657. doi: 10.1002/bbb.1474
CrossRef Full Text | Google Scholar
Demirbas, A. (2004). Pyrolysis of municipal plastic waste for recovery of gasoline-range hydrocarbons. J. Anal. Appl. Pyrolysis 72, 97-102. doi: 10.1016/j.jaap.2004.03.001
CrossRef Full Text | Google Scholar
Dimitrov, N., Krehula, L. K., Siročić, A. P., and Hrnjak-Murgić, Z. (2013). Analysis of recycled PET bottles products by pyrolysis-gas chromatography. Polym. Degrad. Stab. 98, 972-979. doi: 10.1016/j.polymdegradstab.2013.02.013
CrossRef Full Text | Google Scholar
Dziecioł, M., and Trzeszczynski, J. (2000). Lotne produkty degradacji termicznej poli(tereftalanu etylenu) w atmosferze azotu. J. Appl. Polym. Sci. 77, 1894-1901. doi: 10.1002/1097-4628(20000829)77:9<1894::AID-APP5>3.0.CO;2-Y
CrossRef Full Text | Google Scholar
Frigo, S., Seggiani, M., Puccini, M., and Vitolo, S. (2014). Produkcja paliwa ciekłego z pirolizy zużytych opon i jego utylizacja w silniku Diesla. Fuel 116, 399-408. doi: 10.1016/j.fuel.2013.08.044
CrossRef Full Text | Google Scholar
Gaca, P., Drzewiecka, M., Kaleta, W., Kozubek, H., and Nowinska, K. (2008). Katalityczna degradacja polietylenu na mezoporowatym sicie molekularnym MCM-41 modyfikowanym związkami heteropolimerowymi. Polish J. Environ. Stud. 17, 25-35.
Google Scholar
Gandidi, I. M., Susila, M. D., Mustofa, A., and Pambudi, N. A. (2018). Thermal-Catalytic cracking of real MSW into Bio-Crude Oil. J. Energy Inst. 91, 304-310. doi: 10.1016/j.joei.2016.11.005
CrossRef Full Text | Google Scholar
Gebreslassie, B. H., Slivinsky, M., Wang, B., and You, F. (2013). Life cycle optimization for sustainable design and operations of hydrocarbon biorefinery via fast pyrolysis, hydrotreating and hydrocracking. Comput. Chem. Eng. 50, 71-91. doi: 10.1016/j.compchemeng.2012.10.013
CrossRef Full Text | Google Scholar
Heras, F., Jimenez-Cordero, D., Gilarranz, M. A., Alonso-Morales, N., and Rodriguez, J. J. (2014). Activation of waste tire char by cyclic liquid-phase oxidation. Fuel Process. Technol. 127, 157-162. doi: 10.1016/j.fuproc.2014.06.018
CrossRef Full Text | Google Scholar
Inman, M. (2012). Gotowanie paliwa. Nat. Clim. Change 2, 218-220. doi: 10.1038/nclimate1466
CrossRef Full Text | Google Scholar
Jung, S. H., Cho, M. H., Kang, B. S., and Kim, J. S. (2010). Pyroliza frakcji odpadowego polipropylenu i polietylenu w celu odzysku aromatów BTX z wykorzystaniem reaktora fluidalnego. Fuel Process. Technol. 91, 277-284. doi: 10.1016/j.fuproc.2009.10.009
CrossRef Full Text | Google Scholar
Kim, H. S., Kim, S., Kim, H. J., and Yang, H. S. (2006). Właściwości cieplne kompozytów poliolefinowych napełnionych bio-mączką o różnej zawartości i rodzaju środka kompatybilizującego. Thermochim. Acta 451, 181-188. doi: 10.1016/j.tca.2006.09.013
CrossRef Full Text | Google Scholar
Kim, J. R., Yoon, J. H., and Park, D. W. (2002). Katalityczny recykling mieszaniny polipropylenu i polistyrenu. Polym. Degrad. Stab. 76, 61-67. doi: 10.1016/S0141-3910(01)00266-X
CrossRef Full Text | Google Scholar
Kiran, N., Ekinci, E., and Snape, C. E. (2000). Recykling odpadów z tworzyw sztucznych poprzez pirolizę. Resour. Conserv. Recycl. 29, 273-283. doi: 10.1016/S0921-3449(00)00052-5
CrossRef Full Text | Google Scholar
Kunwar, B., Moser, B. R., Chandrasekaran, S. R., Rajagopalan, N., and Sharma, B. K. (2016). Catalytic and thermal depolymerization of low value post-consumer high density polyethylene plastic. Energy 111, 884-892. doi: 10.1016/j.energy.2016.06.024
CrossRef Full Text | Google Scholar
Lecomte, H. A., and Liggat, J. J. (2006). Mechanizm degradacji jednostek glikolu dietylenowego w polimerze tereftalanu. Polym. Degrad. Stab. 91, 681-689. doi: 10.1016/j.polymdegradstab.2005.05.028
CrossRef Full Text | Google Scholar
Lee, K. H. (2012). Effects of the types of zeolites on catalytic upgrading of pyrolysis wax oil. J. Anal. Appl. Pyrol. 94, 209-214. doi: 10.1016/j.jaap.2011.12.015
CrossRef Full Text | Google Scholar
Lee, S., Yoshida, K., and Yoshikawa, K. (2015). Application of waste plastic pyrolysis oil in a direct injection diesel engine: For a small scale non-grid electrification. Energy Environ. Res. 5:18. doi: 10.5539/eer.v5n1p18
CrossRef Full Text
Lee, S. Y., Yoon, J. H., Kim, J. R., and Park, D. W. (2001). Catalytic degradation of polystyrene over natural clinoptilolite zeolite. Polym. Degrad. Stab. 74, 297-305. doi: 10.1016/S0141-3910(01)00162-8
CrossRef Full Text | Google Scholar
Lin, Y. H., Yang, M. H., Yeh, T. F., and Ger, M. D. (2004). Catalytic degradation of high density polyethylene over mesoporous and microporous catalysts in a fluidised-bed reactor. Polym. Degrad. Stab. 86, 121-128. doi: 10.1016/j.polymdegradstab.2004.02.015
CrossRef Full Text | Google Scholar
Lopez, A., Marco d, I., Caballero, B. M., Laresgoiti, M. F., Adrados, A., and Torres, A. (2011). Pyrolysis of municipal plastic waste II: influence of raw material composition under catalytic conditions. Waste Manag. 31, 1973-1983. doi: 10.1016/j.wasman.2011.05.021
CrossRef Full Text | Google Scholar
Lopez, G., Olazar, M., Artetxe, M., Amutio, M., Elordi, G., and Bilbao, J. (2009). Steam activation of pyrolytic tyre char at different temperatures. J. Anal. Appl. Pyrol. 85, 539-543. doi: 10.1016/j.jaap.2008.11.002
CrossRef Full Text | Google Scholar
Ma, C., Yu, J., Wang, B., Song, Z., Xiang, J., Hu, S., et al. (2017). Catalytic pyrolysis of flame retarded high impact polystyrene over various solid acid catalysts. Fuel Process. Technol. 155, 32-41. doi: 10.1016/j.fuproc.2016.01.018
CrossRef Full Text | Google Scholar
Marcilla, A., Beltrán, M. I., Hernández, F., and Navarro, R. (2004). Dezaktywacja HZSM5 i HUSY podczas katalitycznej pirolizy polietylenu. Appl. Catal. A Gen. 278, 37-43. doi: 10.1016/j.apcata.2004.09.023
CrossRef Full Text | Google Scholar
McNeill, I. C., and Bounekhel, M. (1991). Badania degradacji termicznej poliestrów tereftalanowych: 1. Poli(tereftalany alkilenu). Polymer Degrad. Stab. 34, 187-204. doi: 10.1016/0141-3910(91)90119-C
CrossRef Full Text | Google Scholar
McNeill, I. C., Zulfiqar, M., and Kousar, T. (1990). A detailed investigation of the products of the thermal degradation of polystyrene. Polym. Degrad. Stab. 28, 131-151. doi: 10.1016/0141-3910(90)90002-O
CrossRef Full Text | Google Scholar
Miandad, R., Barakat, M. A., Aburiazaiza, A. S., Rehan, M., Ismail, I. M. I., and Nizami, A. S. (2017b). Effect of plastic waste types on pyrolysis liquid oil. Int. Biodeterior. Biodegrad. 119, 239-252. doi: 10.1016/j.ibiod.2016.09.017
CrossRef Full Text | Google Scholar
Miandad, R., Barakat, M. A., Aburiazaiza, A. S., Rehan, M., and Nizami, A. S. (2016a). Catalytic pyrolysis of plastic waste: a review. Process Safety Environ. Protect. 102, 822-838. doi: 10.1016/j.psep.2016.06.022
CrossRef Full Text | Google Scholar
Miandad, R., Barakat, M. A., Rehan, M., Aburiazaiza, A. S., Ismail, I. M. I., and Nizami, A. S. (2017a). Plastic waste to liquid oil through catalytic pyrolysis using natural and synthetic zeolite catalysts. Waste Manag. 69, 66-78. doi: 10.1016/j.wasman.2017.08.032
PubMed Abstract | CrossRef Full Text | Google Scholar
Miandad, R., Kumar, R., Barakat, M. A., Basheer, C., Aburiazaiza, A. S., Nizami, A. S., et al. (2018). Untapped conversion of plastic waste char into carbon-metal LDOs for the adsorption of Congo red. J Colloid Interface Sci. 511, 402-410. doi: 10.1016/j.jcis.2017.10.029
PubMed Abstract | CrossRef Full Text | Google Scholar
Miandad, R., Nizami, A. S., Rehan, M., Barakat, M. A., Khan, M. I., Mustafa, A., et al. (2016b). Influence of temperature and reaction time on the conversion of polystyrene waste to pyrolysis liquid oil. Waste Manag. 58, 250-259. doi: 10.1016/j.wasman.2016.09.023
PubMed Abstract | CrossRef Full Text | Google Scholar
Miandad, R., Rehan, M., Nizami, A. S., Barakat, M. A. E. F., and Ismail, I. M. (2016c). „The energy and value- added products from pyrolysis of waste plastics,” in Recycling of Solid Waste for Biofuels and Bio- Chemicals, eds O. P. Karthikeyan, K. H. Subramanian, and S. Muthu (Singapore: Springer), 333-355.
Google Scholar
Miskolczi, N., Bartha, L., and Deak, G. (2006). Thermal degradation of polyethylene and polystyrene from the packaging industry over different catalysts into fuel-like feed stocks. Polym. Degrad. Stab. 91, 517-526. doi: 10.1016/j.polymdegradstab.2005.01.056
CrossRef Full Text | Google Scholar
Mukherjee, M. K., and Thamotharan, P. C. (2014). Performance and emission test of several blends of waste plastic oil with diesel and ethanol on four stroke twin cylinder diesel engine. IOSR J. Mech. Civil Eng. 11, 2278-1684. doi: 10.9790/1684-11214751
CrossRef Full Text
Nileshkumar, K. D., Jani, R. J., Patel, T. M., and Rathod, G. P. (2015). Effect of blend ratio of plastic pyrolysis oil and diesel fuel on the performance of single cylinder CI engine. Int. J. Sci. Technol. Eng. 1, 2349-2784.
Google Scholar
Nizami, A. S., Ouda, O. K. M., Rehan, M., El-Maghraby, A. M. O., Gardy, J., Hassanpour, A., et al. (2016). Potencjał saudyjskich naturalnych zeolitów w technologiach odzysku energii. Energy 108, 162-171. doi: 10.1016/j.energy.2015.07.030
CrossRef Full Text | Google Scholar
Nizami, A. S., Rehan, M., Waqas, M., Naqvi, M., Ouda, O. K. M., Shahzad, K., et al. (2017a). Waste biorefineries: enabling circular economies in developing countries. Bioresour. Technol. 241, 1101-1117. doi: 10.1016/j.biortech.2017.05.097
PubMed Abstract | CrossRef Full Text | Google Scholar
Nizami, A. S., Shahzad, K., Rehan, M., Ouda, O. K. M., Khan, M. Z., Ismail, I. M. I., et al. (2017b). Developing waste biorefinery in makkah: a way forward to convert urban waste into renewable energy. Appl. Energy. 186, 189-196. doi: 10.1016/j.apenergy.2016.04.116
CrossRef Full Text | Google Scholar
Obali, Z., Sezgi, N. A., and Doğu, T. (2012). Katalityczna degradacja polipropylenu za pomocą mezoporowatych katalizatorów obciążonych tlenkiem glinu. Chem. Ind. Ind. Eng. J. 207, 421-425. doi: 10.1016/j.cej.2012.06.146
CrossRef Full Text | Google Scholar
Ogawa, T., Kuroki, T., Ide, S., and Ikemura, T. (1982). Recovery of indan derivatives from polystyrene waste. J. Appl. Polym. Sci. 27, 857-869. doi: 10.1002/app.1982.070270306
CrossRef Full Text | Google Scholar
Panda, A. K., and Singh, R. K. (2013). Experimental optimization of process for the thermo-catalytic degradation of waste polypropylene to liquid fuel. Adv. Energy Eng. 1, 74-84.
Google Scholar
Peterson, J. D., Vyazovkin, S., and Wight, C. A. (2001). Kinetyka degradacji termicznej i termooksydacyjnej polistyrenu, polietylenu i poli(propylenu). Macromol. Chem. Phys. 202, 775-784. doi: 10.1002/1521-3935(20010301)202:6<775::AID-MACP775>3.0.CO;2-G
CrossRef Full Text | Google Scholar
Ramli, M. R., Othman, M. B. H., Arifin, A., and Ahmad, Z. (2011). Sieć usieciowana polidimetylosiloksanu za pomocą mechanizmów addycji i kondensacji (RTV). Część I: synteza i właściwości termiczne. Polym. Degrad. Stab. 96, 2064-2070. doi: 10.1016/j.polymdegradstab.2011.10.001
CrossRef Full Text | Google Scholar
Ratnasari, D. K., Nahil, M. A., and Williams, P. T. (2017). Catalytic pyrolysis of waste plastics using staged catalysis for production of gasoline range hydrocarbon oils. J. Anal. Appl. Pyrolysis 124, 631-637. doi: 10.1016/j.jaap.2016.12.027
CrossRef Full Text | Google Scholar
Rehan, M., Miandad, R., Barakat, M. A., Ismail, I. M. I., Almeelbi, T., Gardy, J., et al. (2017). Effect of zeolite catalysts on pyrolysis liquid oil. Int. Biodeterior. Biodegrad. 119, 162-175. doi: 10.1016/j.ibiod.2016.11.015
CrossRef Full Text | Google Scholar
Rehan, M., Nizami, A. S., Shahzad, K., Ouda, O. K. M., Ismail, I. M. I., Almeelbi, T., et al. (2016). Pirolityczne paliwo ciekłe: źródło energii odnawialnej w Makkah. Energy Sources A 38, 2598-2603. doi: 10.1080/15567036.2016.1153753
CrossRef Full Text | Google Scholar
Rizzarelli, P., Rapisarda, M., Perna, S., Mirabella, E. F., La Carta, S., Puglisi, C., et al. (2016). Determination of polyethylene in biodegradable polymer blends and in compostable carrier bags by Py-GC/MS and TGA. J. Anal. Appl. Pyrolysis 117,72-81. doi: 10.1016/j.jaap.2015.12.014
CrossRef Full Text | Google Scholar
Saptoadi, H., and Pratama, N. N. (2015). Utilization of plastics waste oil as partial substitute for kerosene in pressurized cookstoves. Int. J. Environ. Sci. Dev. 6, 363-368. doi: 10.7763/IJESD.2015.V6.619
CrossRef Full Text | Google Scholar
Sarker, M., and Rashid, M. M. (2013). Waste plastics mixture of polystyrene and polypropylene into light grade fuel using Fe2O3 catalyst. Int. J. Renew. Energy Technol. Res. 2, 17-28.
Google Scholar
Seo, Y. H., Lee, K. H., and Shin, D. H. (2003). Investigation of catalytic degradation of high density, polyethylene by hydrocarbon group type analysis. J. Anal. Appl. Pyrol. 70, 383-398. doi: 10.1016/S0165-2370(02)00186-9
CrossRef Full Text | Google Scholar
Serrano, D. P., Aguado, J., and Escola, J. M. (2000). Catalytic conversion of polystyrene over HMCM-41, HZSM-5 and amorphous SiO2-Al2O3: comparison with thermal cracking. Appl. Catal. B:Environ. 25, 181-189. doi: 10.1016/S0926-3373(99)00130-7
CrossRef Full Text | Google Scholar
Serrano, D. P., Aguado, J., and Escola, J. M. (2012). Developing advanced catalysts for the conversion of polyolefinic waste plastics into fuels and chemicals. ACS Catal. 2, 1924-1941. doi: 10.1021/cs3003403
CrossRef Full Text | Google Scholar
Shah, J., and Jan, M. R. (2015). Effect of polyethylene terephthalate on the catalytic pyrolysis of polystyrene: Investigation of the liquid products. J. Taiwan Inst. Chem. Eng. 51, 96-102. doi: 10.1016/j.jtice.2015.01.015
CrossRef Full Text | Google Scholar
Siddiqui, M. N., and Redhwi, H. H. (2009). Piroliza mieszanych tworzyw sztucznych w celu odzyskania użytecznych produktów. Fuel Process. Technol. 90, 545-552. doi: 10.1016/j.fuproc.2009.01.003
CrossRef Full Text | Google Scholar
Sriningsih, W., Saerodji, M. G., Trisunaryanti, W., Armunanto, R., and Falah, I. I. (2014). Fuel production from LDPE plastic waste over natural zeolite supported Ni, Ni-Mo, Co and Co-Mo metals. Proc. Environ. Sci. 20, 215-224. doi: 10.1016/j.proenv.2014.03.028
CrossRef Full Text | Google Scholar
Syamsiro, M., Cheng, S., Hu, W., Saptoadi, H., Pratama, N. N., Trisunaryanti, W., et al. (2014). Liquid and gaseous fuel from waste plastics by sequential pyrolysis and catalytic reforming processes over indonesian natural zeolite catalysts. Waste Technol. 2, 44-51. doi: 10.12777/wastech.2.2.44-51
CrossRef Full Text | Google Scholar
Tekin, K., Akalin, M. K., Kadi, C., and Karagöz, S. (2012). Catalytic degradation of waste polypropylene by pyrolysis. J. Energy Ins. 85, 150-155. doi: 10.1179/1743967112Z.00000000029
CrossRef Full Text | Google Scholar
Thilakaratne, R., Tessonnier, J. P., and Brown, R. C. (2016). Conversion of methoxy and hydroxyl functionalities of phenolic monomers over zeolites. Green Chem. 18, 2231-2239. doi: 10.1039/c5gc02548f
CrossRef Full Text | Google Scholar
Uemichi, Y., Hattori, M., Itoh, T., Nakamura, J., and Sugioka, M. (1998). Deactivation behaviors of Zeolite and Silica- Alumina catalysts in the degradation of polyethylene. Ind. Eng. Chem. Res. 37, 867-872. doi: 10.1021/ie970605c
CrossRef Full Text | Google Scholar
Uemichi, Y., Nakamura, J., Itoh, T., Sugioka, M., Garforth, A. A., and Dwyer, J. (1999). Conversion of polyethylene into gasoline-range fuels by two-stage catalytic degradation using Silica-Alumina and HZSM-5 Zeolite. Ind. Eng. Chem. Res. 38, 385-390. doi: 10.1021/ie980341+
CrossRef Full Text | Google Scholar
Ukei, H., Hirose, T., Horikawa, S., Takai, Y., Taka, M., Azuma, N., et al. (2000). Catalytic degradation of polystyrene into styrene and a design of recyclable polystyrene with dispersed catalysts. Catal. Today 62, 67-75. doi: 10.1016/S0920-5861(00)00409-0
CrossRef Full Text | Google Scholar
Waqas, M., Rehan, M., Aburiazaiza, A. S., and Nizami, A. S. (2018). „Chapter 17-Wastewater Biorefinery based on the microbial electrolysis cell: opportunities and challenges,” in Progress and Recent Trends in Microbial Fuel Cells, eds K. Dutta and P. Kundu (New York, NY: Elsevier Inc.), 347-374. doi: 10.1016/B978-0-444-64017-8.00017-8
CrossRef Full Text
Williams, P. T. (2006). „Yield and composition of gases and oils/waxes from the feedstock recycling of waste plastic.” W Feeds Tock Recycling and Pyrolysis of Waste Plastics: Converting Waste Plastics into Diesel and Other Fuels, eds J. Scheirs and W. Kaminsky (West Sussex: John Wiley & Sons Press), 285-309.
Google Scholar
Wu, C., and Williams, P. T. (2010). Piroliza-gazowanie tworzyw sztucznych, mieszanych tworzyw sztucznych i odpadów z tworzyw sztucznych z i bez katalizatora Ni-Mg-Al. Fuel 89, 3022-3032. doi: 10.1016/j.fuel.2010.05.032
CrossRef Full Text | Google Scholar
Wu, J., Chen, T., Luo, X., Han, D., Wang, Z., and Wu, J. (2014). TG/FTIR analysis on co-pyrolysis behavior of PE, PVC and PS. Waste Manag. 34, 676-682. doi: 10.1016/j.wasman.2013.12.005
PubMed Abstract | CrossRef Full Text | Google Scholar
Xue, Y., Johnston, P., and Bai, X. (2017). Effect of catalyst contact mode and gas atmosphere during catalytic pyrolysis of waste plastics. Energy Conv. Manag. 142, 441-451. doi: 10.1016/j.enconman.2017.03.071
CrossRef Full Text | Google Scholar
Yoshioka, T., Grause, G., Eger, C., Kaminsky, W., and Okuwaki, A. (2004). Piroliza poli(tereftalanu etylenu) w instalacji ze złożem fluidalnym. Polym. Degrad. Stab. 86, 499-504. doi: 10.1016/j.polymdegradstab.2004.06.001
CrossRef Full Text | Google Scholar
Zeaiter, J. (2014). Studium procesowe pirolizy odpadowego polietylenu. Fuel 133, 276-282. doi: 10.1016/j.fuel.2014.05.028
CrossRef Full Text | Google Scholar
.