Einführung
Die Produktion und der Verbrauch von Kunststoffabfällen nehmen mit der Zunahme der menschlichen Bevölkerung, dem rasanten Wirtschaftswachstum, der kontinuierlichen Verstädterung und den Veränderungen im Lebensstil in alarmierendem Maße zu. Darüber hinaus beschleunigt die kurze Lebensdauer von Kunststoffen die tägliche Produktion von Kunststoffabfällen. Die weltweite Kunststoffproduktion wurde auf rund 300 Millionen Tonnen pro Jahr geschätzt und nimmt jedes Jahr weiter zu (Miandad et al., 2016a; Ratnasari et al., 2017). Kunststoffe werden aus petrochemischen Kohlenwasserstoffen mit Zusätzen wie Flammschutzmitteln, Stabilisatoren und Oxidationsmitteln hergestellt, die einen biologischen Abbau erschweren (Ma et al., 2017). Das Recycling von Kunststoffabfällen wird auf unterschiedliche Weise durchgeführt, aber in den meisten Entwicklungsländern ist die Entsorgung im Freien oder auf Deponien eine gängige Praxis für die Bewirtschaftung von Kunststoffabfällen (Gandidi et al., 2018). Die Entsorgung von Kunststoffabfällen auf Mülldeponien bietet Lebensraum für Insekten und Nagetiere, die verschiedene Arten von Krankheiten verursachen können (Alexandra, 2012). Außerdem können die Kosten für Transport, Arbeit und Wartung die Kosten von Recyclingprojekten erhöhen (Gandidi et al., 2018). Aufgrund der rasanten Verstädterung nimmt zudem die für Deponien verfügbare Fläche, insbesondere in Städten, ab. Pyrolyse ist eine gängige Technik zur Umwandlung von Kunststoffabfällen in Energie in Form von festen, flüssigen und gasförmigen Brennstoffen.
Pyrolyse ist der thermische Abbau von Kunststoffabfällen bei verschiedenen Temperaturen (300-900°C) in Abwesenheit von Sauerstoff, um flüssiges Öl zu erzeugen (Rehan et al., 2017). Es werden verschiedene Arten von Katalysatoren verwendet, um den Pyrolyseprozess von Kunststoffabfällen insgesamt zu verbessern und die Prozesseffizienz zu erhöhen. Katalysatoren spielen eine sehr wichtige Rolle bei der Förderung der Prozesseffizienz, der Ausrichtung auf eine bestimmte Reaktion und der Reduzierung der Prozesstemperatur und -zeit (Serrano et al., 2012; Ratnasari et al., 2017). Bei der Kunststoffpyrolyse wird eine breite Palette von Katalysatoren eingesetzt, aber die am häufigsten verwendeten Katalysatoren sind ZSM-5, Zeolith, Y-Zeolith, FCC und MCM-41 (Ratnasari et al., 2017). Die katalytische Reaktion während der Pyrolyse von Kunststoffabfällen an festen sauren Katalysatoren kann Cracken, Oligomerisierung, Zyklisierung, Aromatisierung und Isomerisierungsreaktionen umfassen (Serrano et al., 2012).
Verschiedene Studien berichteten über die Verwendung von mikroporösen und mesoporösen Katalysatoren für die Umwandlung von Kunststoffabfällen in flüssiges Öl und Holzkohle. Uemichi et al. (1998) führten eine katalytische Pyrolyse von Polyethylen (PE) mit HZSM-5-Katalysatoren durch. Die Verwendung von HZSM-5 erhöhte die Produktion von Flüssigöl mit einer Zusammensetzung aus aromatischen und isoalkanischen Verbindungen. Gaca et al. (2008) führten die Pyrolyse von Kunststoffabfällen mit modifiziertem MCM-41 und HZSM-5 durch und berichteten, dass bei Verwendung von HZSM-5 leichtere Kohlenwasserstoffe (C3-C4) mit einem Maximum an aromatischen Verbindungen entstanden. Lin et al. (2004) verwendeten verschiedene Arten von Katalysatoren und berichteten, dass sogar die Mischung von HZSM-5 mit mesoporösem SiO2-Al2O3 oder MCM-41 zur maximalen Produktion von flüssigem Öl bei minimaler Gasproduktion führte. Aguado et al. (1997) berichteten über die Gewinnung von Aromaten und aliphatischen Verbindungen aus der katalytischen Pyrolyse von PE mit HZSM-5, während die Verwendung von mesoporösem MCM-41 aufgrund seiner geringen säurekatalytischen Aktivität zu einem Rückgang der erzeugten aromatischen Verbindungen führte. Die Verwendung synthetischer Katalysatoren verbesserte den gesamten Pyrolyseprozess und die Qualität des erzeugten flüssigen Öls. Die Verwendung synthetischer Katalysatoren erhöhte jedoch die Kosten des Pyrolyseprozesses.
Die NZ-Katalysatoren können verwendet werden, um die wirtschaftlichen Herausforderungen der katalytischen Pyrolyse zu überwinden, die mit der Verwendung teurer Katalysatoren einhergehen. In den letzten Jahren hat NZ wegen seiner potenziellen Umweltanwendungen erhebliche Aufmerksamkeit erregt. Natürlich kommt NZ in Japan, den USA, Kuba, Indonesien, Ungarn, Italien und dem Königreich Saudi-Arabien (KSA) vor (Sriningsih et al., 2014; Nizami et al., 2016). Die NZ-Lagerstätten in KSA befinden sich hauptsächlich in Harrat Shama und Jabbal Shama und enthalten hauptsächlich Mordenit-Mineralien mit hoher thermischer Stabilität, wodurch sie sich als Katalysator für die Pyrolyse von Kunststoffabfällen eignen. Sriningsih et al. (2014) modifizierten NZ aus Sukabumi, Indonesien, durch Ablagerung von Übergangsmetallen wie Ni, Co und Mo und führten eine Pyrolyse von Polyethylen niedriger Dichte (LDPE) durch. Gandidi et al. (2018) verwendeten NZ aus Lampung, Indonesien, für die katalytische Pyrolyse von festen Siedlungsabfällen.
Dies ist die erste Studie, die die Wirkung von modifiziertem saudischem Naturzeolith auf die Produktqualität und den Ertrag der katalytischen Pyrolyse von Kunststoffabfällen untersucht. Der saudische Naturzeolith-Katalysator wurde durch neuartige thermische Aktivierung (TA-NZ) bei 550°C und saure Aktivierung (AA-NZ) mit HNO3 modifiziert, um seine katalytischen Eigenschaften zu verbessern. Die katalytische Pyrolyse verschiedener Arten von Kunststoffabfällen (PS, PE, PP und PET), einzeln oder gemischt in verschiedenen Verhältnissen, in Gegenwart modifizierter natürlicher Zeolith (NZ)-Katalysatoren in einem kleinen Pyrolysereaktor im Pilotmaßstab wurde zum ersten Mal durchgeführt. Die Qualität und Ausbeute der Pyrolyseprodukte wie Flüssigöl, Gas und Holzkohle wurden untersucht. Die chemische Zusammensetzung des Flüssigöls wurde mittels GC-MS analysiert. Darüber hinaus wurden das Potenzial und die Herausforderungen von Bioraffinerien auf Pyrolysebasis diskutiert.
Materialien und Methoden
Aufbereitung des Ausgangsmaterials und Inbetriebnahme des Reaktors
Die Kunststoffabfälle, die als Ausgangsmaterial für den katalytischen Pyrolyseprozess verwendet wurden, wurden in Jeddah gesammelt und umfassten Einkaufstüten, Einweg-Saftbecher und -teller sowie Trinkwasserflaschen, die jeweils aus Polyethylen (PE), Polypropylen (PP), Polystyrol (PS) und Polyethylenterephthalat (PET) bestehen. Die Auswahl dieser Kunststoffe erfolgte aufgrund der Tatsache, dass sie die Hauptquelle der in KSA anfallenden Kunststoffabfälle sind. Um ein homogenes Gemisch zu erhalten, wurden alle Abfallproben in kleinere Stücke von etwa 2 cm2 zerkleinert. Die katalytische Pyrolyse wurde mit einzelnen oder gemischten Kunststoffabfällen in unterschiedlichen Verhältnissen durchgeführt (Tabelle 1). Bei jedem Versuch wurden 1000 g Ausgangsmaterial und 100 g Katalysator verwendet. Saudischer Naturzeolith (NZ), der in Harrat-Shama im Nordwesten der Stadt Jeddah, KSA, gesammelt wurde (Nizami et al., 2016), wurde durch thermische und saure Behandlung modifiziert und in diesen katalytischen Pyrolyseversuchen verwendet. NZ wurde vor der Modifizierung und der Verwendung in der Pyrolyse in einer Kugelmühle (Retsch MM 480) 3 h lang mit 20 Hz/sec zu Pulver (<100 nm) zerkleinert. Für die thermische Aktivierung (TA) wurde NZ in einem Muffelofen bei 550°C für 5 h erhitzt, während für die saure Aktivierung (AA) NZ in einer 0,1 M Lösung von Salpetersäure (HNO3) für 48 h eingeweicht und kontinuierlich mit einem IKA HS 501 Digitalschüttler mit 50 rpm geschüttelt wurde. Danach wurde die Probe mit entionisiertem Wasser gewaschen, bis ein normaler pH-Wert erreicht war.
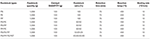
Tabelle 1. Versuchsschema.
Die Versuche wurden in einem kleinen Pyrolysereaktor im Pilotmaßstab bei 450°C mit einer Heizrate von 10°C/min und einer Reaktionszeit von 75 min durchgeführt (Abbildung 1). Die Ausbeute jedes Pyrolyseprodukts wurde nach Beendigung jedes Versuchs auf der Grundlage des Gewichts berechnet. Die Charakterisierung des erzeugten Flüssigöls wurde durchgeführt, um die Auswirkungen der Zusammensetzung des Ausgangsmaterials auf die Qualität des Flüssigöls zu untersuchen, das in Gegenwart von modifiziertem NZ erzeugt wurde. Die TGA wurde am Ausgangsmaterial durchgeführt, um die optimalen Prozessbedingungen wie Temperatur und Reaktionszeit (75 Minuten) unter kontrollierten Bedingungen zu ermitteln. Bei der TGA wurden 10 μg jeder Art von Kunststoffabfall entnommen und mit einer Rate von 10°C von 25 auf 900°C unter einem kontinuierlichen Stickstoffstrom (50 ml/min) erhitzt. Die Autoren dieser Studie haben kürzlich Arbeiten über die Auswirkungen der Zusammensetzung des Ausgangsmaterials und der natürlichen und synthetischen Zeolithkatalysatoren ohne Katalysatormodifikation auf verschiedene Arten von Kunststoffabfällen veröffentlicht (Miandad et al., 2017b; Rehan et al., 2017).
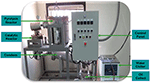
Abbildung 1. Kleiner Pyrolysereaktor im Pilotmaßstab (Miandad et al., 2016b).
Experimenteller Aufbau
Der kleine Reaktor im Pilotmaßstab kann sowohl für die thermische als auch für die katalytische Pyrolyse verwendet werden, wobei verschiedene Ausgangsmaterialien wie Kunststoff und Biomasse eingesetzt werden (Abbildung 1). In dieser Studie wurden modifizierte NZ-Katalysatoren zusammen mit dem Ausgangsmaterial in den Reaktor gegeben. Der Pyrolysereaktor kann bis zu 20 l Ausgangsmaterial fassen, und die maximale sichere Betriebstemperatur von bis zu 600 °C kann mit den gewünschten Heizraten erreicht werden. Die detaillierten Parameter des Pyrolysereaktors wurden bereits veröffentlicht (Miandad et al., 2016b, 2017b). Wenn die Temperatur über bestimmte Werte ansteigt, wandeln sich die Kunststoffabfälle (organische Polymere) in Monomere um, die in den Kondensator geleitet werden, wo diese Dämpfe zu flüssigem Öl kondensiert werden. Es wurde ein kontinuierliches Kondensationssystem mit einem Wasserbad und ACDelco Classic-Kühlmittel verwendet, um die Kondensationstemperatur unter 10 °C zu halten und eine maximale Kondensation der Dämpfe zu flüssigem Öl zu gewährleisten. Das erzeugte Flüssigöl wurde aus dem Ölsammeltank aufgefangen und weiter charakterisiert, um seine chemische Zusammensetzung und Eigenschaften für andere potenzielle Anwendungen zu ermitteln.
Analytische Methoden
Das Pyrolyseöl wurde mit verschiedenen Techniken wie Gaschromatographie gekoppelt mit Massenspektrophotometrie (GC-MS), Fourier-Transformations-Infrarot-Spektroskopie (FT-IR),
Bombenkalorimeter und TGA (Mettler Toledo TGA/SDTA851) unter Anwendung der ASTM-Standardmethoden charakterisiert. Die funktionellen Gruppen im Pyrolyseöl wurden mit einem FT-IR-Gerät von Perkin Elmer, UK, analysiert. Die FT-IR-Analyse wurde unter Verwendung von mindestens 32 Scans mit einem Durchschnitt von 4 cm-1 IR-Signalen im Frequenzbereich von 500-4.000 cm-1 durchgeführt.
Die chemische Zusammensetzung des Öls wurde mit einem GC-MS (Shimadzu QP-Plus 2010) mit FI-Detektor untersucht. Es wurde eine 30 m lange und 0,25 mm breite GC-Kapillarsäule verwendet, die mit einem 0,25 μm dicken Film aus 5 % Phenyl-Methylpolysiloxan (HP-5) beschichtet war. Der Ofen wurde für 2 Minuten auf 50°C eingestellt und dann mit einer Heizrate von 5°C/min auf 290°C erhöht. Die Temperatur der Ionenquelle und der Transferleitung wurde auf 230 bzw. 300 °C gehalten, und die Splitless-Injektion wurde bei 290 °C durchgeführt. Die Massenspektraldatenbibliothek NIST08s wurde zur Identifizierung der chromatographischen Peaks verwendet, und die Peak-Prozentsätze wurden anhand ihrer Gesamtionenchromatogramm-Peakfläche (TIC) bewertet. Die hohen Heizwerte (HHV) des erzeugten flüssigen Öls, das aus verschiedenen Arten von Kunststoffabfällen gewonnen wurde, wurden nach der Standardmethode ASTM D 240 mit einem Bombenkalorimeter (Parr 6200 Calorimeter) gemessen, während die Gaserzeugung anhand der Standard-Massenbilanzformel unter Berücksichtigung der Gewichtsdifferenz von flüssigem Öl und Holzkohle geschätzt wurde.
Ergebnisse und Diskussion
TGA-Analyse des Ausgangsmaterials
Die TGA wurde für jede Art von Kunststoffabfall einzeln durchgeführt, um die optimale Temperatur für den thermischen Abbau zu bestimmen. Alle Arten von Kunststoffabfällen zeigen ein ähnliches Abbauverhalten mit einem schnellen Gewichtsverlust der Kohlenwasserstoffe innerhalb eines engen Temperaturbereichs (150-250°C) (Abbildung 2). Der maximale Abbau für jede Art von Kunststoffabfall wurde bei 420-490°C erreicht. PS und PP zersetzten sich in einem Schritt, während PE und PET unter kontrollierten Bedingungen in zwei Schritten zersetzt wurden. Die einstufige Zersetzung ist auf das Vorhandensein einer Kohlenstoff-Kohlenstoff-Bindung zurückzuführen, die den zufälligen Spaltungsmechanismus mit steigender Temperatur fördert (Kim et al., 2006). Der Abbau von PP begann im Vergleich zu anderen Rohstoffen bei einer sehr niedrigen Temperatur (240 °C). Die Hälfte des Kohlenstoffs in der Kette von PP besteht aus tertiärem Kohlenstoff, der die Bildung von Carbokationen während des thermischen Abbauprozesses fördert (Jung et al., 2010). Dies ist wahrscheinlich der Grund dafür, dass der maximale PP-Abbau bei einer niedrigeren Temperatur erreicht wird. Die anfängliche Zersetzung von PS begann bei 330 °C und die maximale Zersetzung wurde bei 470 °C erreicht. PS hat eine zyklische Struktur, und sein Abbau unter thermischen Bedingungen beinhaltet sowohl eine zufällige Ketten- als auch eine Endkettenspaltung, was seinen Abbauprozess verstärkt (Demirbas, 2004; Lee, 2012).
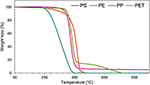
Abbildung 2. Thermogravimetrische Analyse (TGA) von PS-, PE-, PP- und PET-Kunststoffabfällen.
PE und PET zeigten einen zweistufigen Zersetzungsprozess; der anfängliche Abbau begann bei niedrigeren Temperaturen, gefolgt von der zweiten Abbauphase bei einer höheren Temperatur. Die anfängliche Zersetzung von PE begann bei 270 °C und setzte sich langsam, aber allmählich bis zu einer Temperatur von 385 °C fort. Nach dieser Temperatur wurde ein starker Abbau beobachtet, und bei einem weiteren Temperaturanstieg von etwa 100 °C wurde ein Abbau von 95 % erreicht. Ein ähnliches zweistufiges Zersetzungsmuster wurde für PET-Kunststoff beobachtet, wobei die erste Zersetzung bei 400 °C mit einem starken Gewichtsverlust begann. Der zweite Abbau begann jedoch bei einer etwas höheren Temperatur (550 °C). Der anfängliche Abbau von PE und PET kann auf das Vorhandensein einiger flüchtiger Verunreinigungen zurückzuführen sein, wie z. B. die bei der Kunststoffsynthese verwendeten Füllstoffe (Dimitrov et al., 2013).
Verschiedene Forscher haben berichtet, dass der Abbau von PE und PET im Vergleich zu anderen Kunststoffen höhere Temperaturen erfordert (Dimitrov et al., 2013; Rizzarelli et al., 2016). Lee (2012) berichtete, dass PE eine langkettige, verzweigte Struktur hat und dass sein Abbau durch zufällige Kettenspaltung erfolgt, was eine höhere Temperatur erfordert, während der Abbau von PET durch zufällige Spaltung der Esterverbindungen erfolgt, was zur Bildung von Oligomeren führt (Dziecioł und Trzeszczynski, 2000; Lecomte und Liggat, 2006). Der anfängliche Abbau von PET ist möglicherweise auf das Vorhandensein einiger flüchtiger Verunreinigungen wie Diethylenglykol zurückzuführen (Dimitrov et al., 2013). In der Literatur wird berichtet, dass das Vorhandensein dieser flüchtigen Verunreinigungen den Abbauprozess der Polymere weiter fördert (McNeill und Bounekhel, 1991; Dziecioł und Trzeszczynski, 2000). Die Unterschiede in den TGA-Kurven der verschiedenen Kunststoffarten könnten auf ihre mesoporöse Struktur zurückzuführen sein (Chandrasekaran et al., 2015). Darüber hinaus berichteten Lopez et al. (2011), dass der Einsatz von Katalysatoren die Prozesstemperatur senkt. Daher könnten 450 °C in Gegenwart von aktiviertem NZ als optimale Temperatur für die katalytische Pyrolyse der oben genannten Kunststoffabfälle angesehen werden.
Auswirkung von Ausgangsmaterial und Katalysatoren auf die Ausbeute der Pyrolyseprodukte
Die Wirkung der thermischen und sauren Aktivierung von NZ auf die Produktausbeute des Pyrolyseprozesses wurde untersucht (Abbildung 3). Die katalytische Pyrolyse von einzelnen PS-Kunststoffen unter Verwendung von TA-NZ- und AA-NZ-Katalysatoren ergab die höchsten Flüssigölausbeuten von 70 bzw. 60 % im Vergleich zu allen anderen untersuchten Arten von einzelnen und kombinierten Kunststoffabfällen. Die hohe Ausbeute an Flüssigöl aus der katalytischen Pyrolyse von PS wurde auch in mehreren anderen Studien berichtet (Siddiqui und Redhwi, 2009; Lee, 2012; Rehan et al., 2017). Siddiqui und Redhwi (2009) berichteten, dass PS eine zyklische Struktur hat, die zu einer hohen Ausbeute an flüssigem Öl aus der katalytischen Pyrolyse führt. Lee (2012) berichtete, dass der PS-Abbau sowohl durch zufällige Ketten- als auch durch Endkettenspaltungen erfolgt, was zur Bildung einer stabilen Benzolringstruktur führt, die das weitere Cracken fördert und die Flüssigölproduktion erhöhen kann. Darüber hinaus folgte der PS-Abbau in Gegenwart von Säurekatalysatoren einem Carbenium-Mechanismus, der zu einer Hydrierung (inter-/intramolekularer Wasserstofftransfer) und β-Spaltung führte (Serrano et al., 2000). Darüber hinaus erfolgte der Abbau von PS aufgrund seiner zyklischen Struktur bei einer niedrigeren Temperatur als bei anderen Kunststoffen wie PE (Wu et al., 2014). Andererseits wurde bei der katalytischen Pyrolyse von PS mit AA-NZ-Katalysator eine größere Menge an Holzkohle (24,6 %) erzeugt als mit TA-NZ-Katalysator (15,8 %). Ma et al. (2017) berichteten ebenfalls über die hohe Produktion von Holzkohle aus der katalytischen Pyrolyse von PS mit einem sauren Zeolith (Hβ)-Katalysator. Die hohen Zahlen der Holzkohleproduktion waren auf den hohen Säuregehalt des Katalysators zurückzuführen, der die Holzkohleproduktion durch intensive sekundäre Vernetzungsreaktionen begünstigt (Serrano et al., 2000).
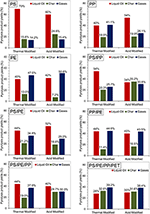
Abbildung 3. Auswirkung von TA-NZ und AA-NZ auf die Ausbeute an Pyrolyseprodukten.
Bei der katalytischen Pyrolyse von PP wurde mit dem AA-NZ-Katalysator mehr Flüssigöl (54 %) als mit dem TA-NZ-Katalysator (40 %) erzeugt (Abbildung 3). Der TA-NZ-Katalysator erzeugte dagegen große Mengen Gas (41,1 %), was auf die geringere katalytische Aktivität des TA-NZ-Katalysators zurückzuführen sein könnte. Nach Kim et al. (2002) begünstigen Katalysatoren mit geringer Acidität und BET-Oberflächen mit mikroporösen Strukturen den anfänglichen Abbau von PP, was zu einer maximalen Gasproduktion führen kann. Obali et al. (2012) führten die Pyrolyse von PP mit einem mit Aluminiumoxid beladenen Katalysator durch und berichteten über die maximale Gasproduktion. Darüber hinaus kann die Bildung von Carbokationen während des Abbaus von PP aufgrund des Vorhandenseins von tertiärem Kohlenstoff in der Kohlenstoffkette die Gasproduktion ebenfalls begünstigen (Jung et al., 2010). Syamsiro et al. (2014) berichteten auch, dass die katalytische Pyrolyse von PP und PS mit einem säureaktivierten (HCL) Naturzeolith-Katalysator aufgrund seiner hohen Acidität und BET-Oberfläche mehr Gase erzeugte als der Prozess mit einem thermisch aktivierten Naturzeolith-Katalysator.
Die katalytische Pyrolyse von PE mit TA-NZ- und AA-NZ-Katalysatoren erzeugte ähnliche Mengen an flüssigem Öl (40 und 42 %). Die höchsten Mengen an Gasen (50,8 und 47,0 %) wurden jedoch aus PE mit AA-NZ bzw. TA-NZ erzeugt, verglichen mit allen anderen untersuchten Kunststoffarten. Die Produktion von Holzkohle war in diesem Fall am geringsten: 7,2 und 13,0 % bei AA-NZ bzw. TA-NZ. Verschiedene Studien berichteten auch über die geringere Produktion von Holzkohle bei der katalytischen Pyrolyse von PE (Xue et al., 2017). Lopez et al. (2011) berichteten, dass Katalysatoren mit hohem Säuregehalt die Rissbildung von Polymeren während der katalytischen Pyrolyse verstärken. Die Zunahme der Spaltung in Gegenwart eines stark sauren Katalysators fördert die Produktion von Gasen (Miandad et al., 2016b, 2017a). Zeaiter (2014) führte eine katalytische Pyrolyse von PE mit HBeta-Zeolith durch und berichtete über eine Gasproduktion von 95,7 % aufgrund des hohen Säuregehalts des Katalysators. Batool et al. (2016) berichteten ebenfalls über die maximale Gasproduktion bei der katalytischen Pyrolyse von PE mit einem stark sauren ZSM-5-Katalysator. Nach Lee (2012) und Williams (2006) hat PE eine langkettige Kohlenstoffstruktur, und seine Zersetzung erfolgt zufällig in kleinere Kettenmoleküle durch zufällige Kettenspaltung, was die Gasproduktion fördern kann. Bei der Pyrolyse von PE, das nur C-H- und C-C-Bindungen aufweist, kam es zunächst zu einem Bruch des Makromolekülrückgrats, wobei stabile freie Radikale entstanden. Anschließend erfolgten Hydrierungsschritte, die zur Synthese von sekundären freien Radikalen (neue stabile C-H-Bindung) führten, die zu einer β-Spaltung führten und eine ungesättigte Gruppe erzeugten (Rizzarelli et al., 2016).
Die katalytische Pyrolyse von PP/PE (50/50%-Verhältnis) zeigte keinen signifikanten Unterschied in den Gesamtproduktausbeuten, wenn sowohl AA-NZ als auch TA-NZ verwendet wurden. Die Ausbeute an Flüssigöl aus der katalytischen Pyrolyse von PP/PE betrug 44 bzw. 40 % bei Verwendung von TA-NZ- und AA-NZ-Katalysatoren. Ein leichter Rückgang der Flüssigölausbeute bei AA-NZ könnte auf seinen hohen Säuregehalt zurückzuführen sein. Syamsiro et al. (2014) berichteten, dass AA-NZ mit HCl im Vergleich zu TA-NZ eine hohe Acidität aufweist, eine geringere Flüssigölausbeute liefert und eine hohe Gasproduktion aufweist. Insgesamt erzeugte die katalytische Pyrolyse von PP/PE die größte Gasmenge bei geringen Mengen an Holzkohle. Die hohe Gasproduktion kann auf die Anwesenheit von PP zurückzuführen sein. Der Abbau von PP verstärkt den Carbokationsprozess aufgrund des Vorhandenseins von tertiärem Kohlenstoff in seiner Kohlenstoffkette (Jung et al., 2010). Darüber hinaus begünstigt der Abbau von PE in Gegenwart eines Katalysators die Produktion von Gas mit einer geringen Ausbeute an flüssigem Öl. Wurde die katalytische Pyrolyse von PP und PE jedoch separat mit PS durchgeführt, wurde ein signifikanter Unterschied in der Produktausbeute beobachtet.
Bei der katalytischen Pyrolyse von PS/PP (50/50%-Verhältnis) mit TA-NZ- bzw. AA-NZ-Katalysatoren wurde ein signifikanter Unterschied in der Flüssigölausbeute von 54 bzw. 34% festgestellt. Ebenso wurde ein signifikanter Unterschied bei der Ausbeute an Holzkohle von 20,3 und 35,2 % beobachtet, während die hohe Ausbeute an Gasen bei Verwendung von TA-NZ- bzw. AA-NZ-Katalysatoren 25,7 und 30,8 % betrug. Lopez et al. (2011) und Seo et al. (2003) berichteten, dass ein Katalysator mit hohem Säuregehalt den Crackprozess fördert und eine maximale Gasproduktion erzeugt. Darüber hinaus erhöht das Vorhandensein von PP auch die Gasproduktion aufgrund des Carbokationsprozesses während des Abbaus (Jung et al., 2010). Kim et al. (2002) berichteten, dass der PP-Abbau in Gegenwart von sauren Katalysatoren ein Maximum an Gas erzeugt.
Die katalytische Pyrolyse von PS mit PE (50/50%-Verhältnis) in Gegenwart des TA-NZ-Katalysators ergab 44% flüssiges Öl, während mit dem AA-NZ-Katalysator 52% flüssiges Öl gewonnen wurde. Kiran et al. (2000) führten die Pyrolyse von PS mit PE in verschiedenen Verhältnissen durch und berichteten, dass eine Erhöhung der PE-Konzentration die Flüssigölkonzentration mit der Zunahme des Gases verringert. Die Anwesenheit von PS mit PE fördert den Abbauprozess aufgrund der Bildung eines aktiven stabilen Benzolrings aus PS (Miandad et al., 2016b). Wu et al. (2014) führten eine TGA von PS mit PE durch und beobachteten zwei Peaks, den ersten für PS bei einer niedrigen Temperatur, gefolgt vom PE-Abbau bei einer hohen Temperatur. Darüber hinaus folgt der PE-Abbau einem radikalischen Kettenprozess und einem Hydrierungsprozess, während PS einem radikalischen Kettenprozess mit verschiedenen Schritten folgt (Kiran et al., 2000). Somit führte PS selbst bei Berücksichtigung der Abbauphänomene zu einem höheren Abbau im Vergleich zu PE und produzierte stabile Benzolringe (McNeill et al., 1990).
Die katalytische Pyrolyse von PS/PE/PP (Verhältnis 50/25/25%) zeigte etwas geringere Flüssigölausbeuten im Vergleich zur katalytischen Pyrolyse aller einzelnen Kunststofftypen. Die Ölausbeute beider Katalysatoren, TA-NZ und AA-NZ, ist in diesem Fall ähnlich: 44 bzw. 40 %. Die Holzkohleproduktion war mit dem AA-NZ-Katalysator höher (29,7 %) als mit dem TA-NZ-Katalysator (19,0 %), was auf Polymerisationsreaktionen zurückzuführen sein könnte (Wu und Williams, 2010). Darüber hinaus verringerte die Zugabe von PET mit PS, PE und PP (Verhältnis 20/40/20/20 %) die Flüssigölausbeute auf insgesamt 28 bzw. 30 % unter Verwendung von TA-NZ- bzw. AA-NZ-Katalysatoren, mit höheren Anteilen von Holzkohle und Gas. Demirbas (2004) führte die Pyrolyse von PS/PE/PP durch und meldete ähnliche Ergebnisse für die Produktausbeute. Adnan et al. (2014) führten eine katalytische Pyrolyse von PS und PET unter Verwendung des Al-Al2O3-Katalysators mit einem Verhältnis von 80/20 % durch und meldeten nur 37 % flüssiges Öl. Darüber hinaus berichteten Yoshioka et al. (2004) über die maximale Produktion von Gas und Holzkohle bei vernachlässigbarer Flüssigölproduktion durch katalytische Pyrolyse von PET. Darüber hinaus wurde eine maximale Holzkohleproduktion gemeldet, wenn die katalytische Pyrolyse von PET mit anderen Kunststoffen durchgeführt wurde (Bhaskar et al., 2004). Die höhere Produktion von Holzkohle bei der Pyrolyse von PET war auf die Verkokungs- und Kondensationsreaktionen während der Pyrolyse bei hoher Temperatur zurückzuführen (Yoshioka et al., 2004). Darüber hinaus begünstigt das Vorhandensein des Sauerstoffatoms die hohe Produktion von Holzkohle bei der katalytischen Pyrolyse von PET (Xue et al., 2017). Thilakaratne et al. (2016) berichteten, dass die Produktion von benzolfreien Radikalen mit zwei aktivierten Kohlenstoffen der Vorläufer von katalytischem Koks aus dem PET-Abbau ist.
Einfluss der Katalysatoren auf die Zusammensetzung des Flüssigöls
Die chemische Zusammensetzung des Flüssigöls, das durch die katalytische Pyrolyse verschiedener Kunststoffabfälle unter Verwendung von TA-NZ- und AA-NZ-Katalysatoren hergestellt wurde, wurde mittels GC-MS charakterisiert (Abbildungen 4 und 5). Die Zusammensetzung des erzeugten Flüssigöls wird durch die verschiedenen Arten von Ausgangsmaterial und die im Pyrolyseprozess verwendeten Katalysatoren beeinflusst (Miandad et al., 2016a,b,c). Das aus den einzelnen Kunststoffarten wie PS, PP und PE hergestellte Flüssigöl enthielt eine Mischung aus aromatischen, aliphatischen und anderen Kohlenwasserstoffverbindungen. Die aromatischen Verbindungen, die im Öl aus PS und PE gefunden wurden, waren höher als bei PP unter Verwendung des TA-NZ-Katalysators. Bei Verwendung des AA-NZ-Katalysators nahmen die aromatischen Verbindungen in PS- und PP-Öl zu, während sie in PE abnahmen. Der mesoporöse und saure Katalysator führt aufgrund seiner hohen Crackfähigkeit zur Produktion von kürzerkettigen Kohlenwasserstoffen (Lopez et al., 2011). Mikroporöse und weniger saure Katalysatoren hingegen begünstigen die Produktion von langkettigen Kohlenwasserstoffen, da der Crackprozess nur an der äußeren Oberfläche der Katalysatoren stattfindet. Insgesamt folgen PE und PP in Gegenwart von Katalysatoren dem Mechanismus der zufälligen Kettenspaltung, während PS dem Mechanismus der Aufspaltung der Endkette folgt (Cullis und Hirschler, 1981; Peterson et al., 2001). Die Endkettenspaltung führt zur Produktion von Monomeren, während die zufällige Kettenspaltung Oligomere und Monomere produziert (Peterson et al., 2001).
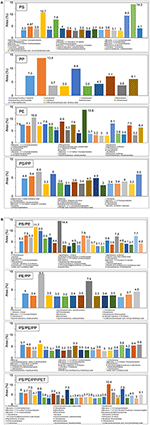
Abbildung 4. (A,B) GC-MS von flüssigem Öl, das aus verschiedenen Arten von Kunststoffabfällen mit TA-NZ hergestellt wurde.
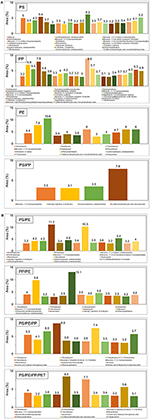
Abbildung 5. (A,B) GC-MS von flüssigem Öl, das aus verschiedenen Arten von Kunststoffabfällen mit AA-NZ hergestellt wurde.
Das flüssige Öl, das bei der katalytischen Pyrolyse von PE mit beiden Katalysatoren hergestellt wurde, produzierte hauptsächlich Naphthalin, Phenanthren, Naphthalin, 2-Ethylen, 1-Pentadecen, Anthracen, 2-Methyl, Hexadecan usw. (Abbildungen 4A, 5A). Diese Ergebnisse stimmen mit mehreren anderen Studien überein (Lee, 2012; Xue et al., 2017). Die Herstellung eines Benzolderivats zeigt, dass TA-NZ den Prozess der Aromatisierung im Vergleich zu AA-NZ verstärkt. Xue et al. (2017) berichteten, dass intermediäre Olefine, die bei der katalytischen Pyrolyse von PE entstehen, in den Poren der Katalysatoren weiter aromatisiert werden. Die Aromatisierungsreaktion führt jedoch auch zur Bildung von Wasserstoffatomen, die den Aromatisierungsprozess verstärken können. Lee (2012) berichtete, dass ZSM-5 im Vergleich zum Mordenit-Katalysator aufgrund seiner kristallinen Struktur mehr aromatische Verbindungen produziert.
Es gibt zwei mögliche Mechanismen, die den Abbau von PE in Gegenwart eines Katalysators bewirken können: die Abstraktion von Hybridionen aufgrund des Vorhandenseins von Lewis-Stellen oder der Carbenium-Ionen-Mechanismus durch die Addition eines Protons (Rizzarelli et al., 2016). Der Abbau beginnt zunächst an der äußeren Oberfläche der Katalysatoren und setzt sich später in den inneren Poren der Katalysatoren fort (Lee, 2012). Mikroporöse Katalysatoren behindern jedoch den Eintritt größerer Moleküle, so dass bei der katalytischen Pyrolyse von PE mit mikroporösen Katalysatoren Verbindungen mit höheren Kohlenstoffketten entstehen. Darüber hinaus kann in Gegenwart von sauren Katalysatoren aufgrund des Carbenium-Mechanismus die Bildung von aromatischen und olefinischen Verbindungen zunehmen (Lee, 2012). Lin et al. (2004) berichteten über eine hochreaktive Olefinproduktion als Zwischenprodukte bei der katalytischen Pyrolyse von PE, die die Produktion von Paraffin und aromatischen Verbindungen im erzeugten Flüssigöl begünstigen kann. Darüber hinaus kann das Vorhandensein eines sauren Katalysators und eines freien Wasserstoffatoms zur Alkylierung von Toluol und Benzol führen, wobei das alkylierte Benzol durch Aromatisierung in Naphthalin umgewandelt wird (Xue et al., 2017).
Das Flüssigöl, das bei der katalytischen Pyrolyse von PS mit TA-NZ und AA-NZ entsteht, enthält verschiedene Arten von Verbindungen. Alpha-Methylstyrol, Benzol, 1,1′-(2-Buten-1,4-diyl)bis-, Bibenzyl, Benzol, (1,3-Propandiyl), Phenanthren, 2-Phenylnaphthalin und so weiter waren die wichtigsten Verbindungen, die im hergestellten flüssigen Öl gefunden wurden (Abbildungen 4A, 5A). Das aus der katalytischen Pyrolyse von PS mit beiden aktivierten Katalysatoren hergestellte Flüssigöl enthält hauptsächlich aromatische Kohlenwasserstoffe mit einigen Paraffinen, Naphthalin und Olefinverbindungen (Rehan et al., 2017). In Gegenwart eines Katalysators wurde jedoch die maximale Produktion von aromatischen Verbindungen erreicht (Xue et al., 2017). Ramli et al. (2011) berichteten ebenfalls über die Herstellung von Olefinen, Naphthalin und aromatischen Verbindungen aus der katalytischen Pyrolyse von PS mit Al2O3, unterstützt durch Cd- und Sn-Katalysatoren. Der Abbau von PS beginnt mit dem Cracken an der äußeren Oberfläche des Katalysators, gefolgt von der Reformierung in den Poren des Katalysators (Uemichi et al., 1999). Zunächst wird das Cracken des Polymers durch die Lewis-Säure auf der Oberfläche des Katalysators durchgeführt, um Carbokation-Zwischenprodukte zu erzeugen, die dann verdampfen oder in den Poren des Katalysators reformiert werden (Xue et al., 2017).
Die katalytische Pyrolyse von PS erzeugt hauptsächlich Styrol und seine Derivate als die wichtigsten Verbindungen im erzeugten flüssigen Öl (Siddiqui und Redhwi, 2009; Rehan et al., 2017). Die Umwandlung von Styrol in sein Derivat wurde in Gegenwart von protonierten Katalysatoren aufgrund der Hydrierung erhöht (Kim et al., 2002). Shah und Jan (2015) und Ukei et al. (2000) berichteten, dass die Hydrierung von Styrol mit der Erhöhung der Reaktionstemperatur zunimmt. Ogawa et al. (1982) führten die Pyrolyse von PS mit einem Aluminiumoxid-Silika-Katalysator bei 300 °C durch und stellten die Hydrierung von Styrol zu seinem Derivat fest. Ramli et al. (2011) berichteten über den möglichen Abbaumechanismus von PS an sauren Katalysatoren, der durch den Angriff eines Protons, das mit sauren Bronsted-Stellen assoziiert ist, zustande kommt, was zu einem Carbenium-Ionen-Mechanismus führt, bei dem es zu einer β-Spaltung kommt, auf die später eine Wasserstoffübertragung folgt. Darüber hinaus wurde die Vernetzungsreaktion durch starke saure Bronsted-Stellen begünstigt, und wenn diese Reaktion auftritt, kann die vollständige Rissbildung bis zu einem gewissen Grad abnehmen und die Produktion von Holzkohle fördern (Serrano et al., 2000). Darüber hinaus haben Siliziumdioxid-Aluminiumoxid-Katalysatoren keine starken sauren Bronsted-Zentren, was zwar die Vernetzungsreaktion nicht verbessert, aber den Hydrierungsprozess begünstigt. Dies könnte der Grund dafür sein, dass Styrol im flüssigen Öl nicht gefunden wurde, sein Derivat jedoch in großen Mengen nachgewiesen wurde (Lee et al., 2001). Xue et al. (2017) berichteten auch über die Dealkylierung von Styrol aufgrund der Verzögerung der Verdampfung im Reaktor, was zu einem verstärkten Reformierungsprozess und der Produktion eines Styrolderivats führen kann. TA-NZ und AA-NZ enthalten einen hohen Anteil an Aluminiumoxid und Siliziumdioxid, der zur Hydrierung von Styrol zu seinem Derivat führt, was die Produktion von Styrolmonomeren anstelle von Styrol zur Folge hat.
Die katalytische Pyrolyse von PP ergab ein komplexes Gemisch aus flüssigem Öl, das Aromaten, Olefine und Naphthalinverbindungen enthält. Benzol, 1,1′-(2-Buten-1,4-diyl)bis-, Benzol, 1,1′-(1,3-Propandiyl)bis-, Anthracen, 9-Methyl-, Naphthalin, 2-Phenyl-, 1,2,3,4-Tetrahydro-1-Phenyl-, Naphthalin, Phenanthren usw. waren die wichtigsten Verbindungen, die im flüssigen Öl gefunden wurden (Abbildungen 4A, 5A). Diese Ergebnisse stehen im Einklang mit anderen Studien, die eine katalytische Pyrolyse von PP mit verschiedenen Katalysatoren durchgeführt haben (Marcilla et al., 2004). Darüber hinaus führte der Abbau von PP mit AA-NZ zu einer maximalen Produktion von Phenolverbindungen. Die höhere Produktion war möglicherweise auf das Vorhandensein von stark sauren Stellen zurückzuführen, da diese die Produktion von Phenolverbindungen begünstigen. Darüber hinaus förderte das Vorhandensein einer stark sauren Stelle auf den Katalysatoren den Mechanismus der Oligomerisierung, Aromatisierung und Desoxygenierung, der zur Herstellung von polyaromatischen und Naphthalinverbindungen führte. Dawood und Miura (2002) berichteten ebenfalls über die hohe Produktion dieser Verbindungen aus der katalytischen Pyrolyse von PP mit einem stark säurehaltigen modifizierten HY-Zeolith.
Die Zusammensetzung des Öls aus der katalytischen Pyrolyse von PP mit PE enthält Verbindungen, die in dem Öl aus beiden einzelnen Kunststoffarten vorkommen. Miandad et al. (2016b) berichteten, dass die Zusammensetzung des Ausgangsmaterials auch die Qualität und chemische Zusammensetzung des Öls beeinflusst. Das aus der katalytischen Pyrolyse von PE/PP gewonnene flüssige Öl enthält aromatische, olefinische und Naphthalinverbindungen. Die wichtigsten gefundenen Verbindungen waren Benzol, 1,1′-(1,3-Propandiyl)bis-, Mono(2-ethylhexyl)ester, 1,2-Benzoldicarbonsäure, Anthracen, Pentadecan, Phenanthren, 2-Phenylnaphthalin und so weiter (Abbildungen 4B und 5B). Jung et al. (2010) berichteten, dass die Produktion von Aromaten aus der katalytischen PP/PE-Pyrolyse dem Diels-Alder-Reaktionsmechanismus folgen könnte, dem dann eine Dehydrierung folgt. Außerdem wurden bei der katalytischen Pyrolyse von PP und PE, die einzeln mit PS durchgeführt wurde, aufgrund des Vorhandenseins von PS hauptsächlich aromatische Verbindungen erzeugt. Das aus PS/PP gewonnene flüssige Öl enthält Benzol, 1,1′-(1,3-Propandiyl)bis, 1,2-Benzoldicarbonsäure, Disooctylester, Bibenzyl, Phenanthren, 2-Phenylnaphthalin, Benzol, (4-Methyl-1-decenyl)- und so weiter (Abbildungen 4A, 5A). Bei der katalytischen Pyrolyse von PS mit PE entstand hauptsächlich flüssiges Öl mit den Hauptbestandteilen Azulen, Naphthalin, 1-Methyl-, Naphthalin, 2-Ethenyl, Benzol, 1,1′-(1,3-Propandiyl)bis-, Phenanthren, 2-Phenylnaphthalin, Benzol, 1,1′-(1-Methyl-1,2-Ethandiyl)bis- und einigen anderen Verbindungen (Abbildungen 4B und 5B). Miskolczi et al. (2006) führten die Pyrolyse von PS mit PE in einem Verhältnis von 10 bzw. 90 % durch und berichteten über die maximale Produktion von Aromaten selbst bei einem sehr niedrigen PS-Anteil. Miandad et al. (2016b) berichteten, dass die thermische Pyrolyse von PE mit PS ohne Katalysator zu einer Umwandlung von PE in flüssiges Öl mit einem hohen Anteil an Aromaten führte. Bei der thermischen Pyrolyse von PE ohne Katalysator wurde es jedoch aufgrund seiner stark langkettig verzweigten Struktur in Wachs und nicht in flüssiges Öl umgewandelt (Lee, 2012; Miandad et al., 2016b). Wu et al. (2014) führten eine TGA von PS mit PE durch und berichteten, dass die Anwesenheit von PS den Abbau von PE aufgrund der Bildung stabiler Benzolringe begünstigt.
Die chemische Zusammensetzung des Pyrolyseöls nach verschiedenen funktionellen Gruppen wurde mithilfe von FT-IR untersucht. Die erhaltenen Daten zeigten das Vorhandensein von aromatischen und aliphatischen funktionellen Gruppen im Öl (Abbildungen 6 und 7). Ein sehr starker Peak bei 696 cm-1 wurde in den meisten flüssigen Ölen, die mit beiden Katalysatoren gewonnen wurden, beobachtet, was auf eine hohe Konzentration an aromatischen Verbindungen hinweist. Zwei weitere offensichtliche Peaks waren bei ca. 1.456 und 1.495 cm-1 für C-C mit Einfach- und Doppelbindungen sichtbar, die aromatischen Verbindungen entsprechen. Darüber hinaus wurden am Ende des Spektrums bei allen Arten von Flüssigölen außer dem PS starke Peaks bei 2 850, 2 923 und 2 958 cm-1 beobachtet, die der C-H-Strecke von Alkanverbindungen entsprechen. Insgesamt zeigte das Flüssigöl, das aus der katalytischen Pyrolyse verschiedener Kunststoffabfälle mit dem AA-NZ-Katalysator gewonnen wurde, mehr Peaks als die Proben aus den TA-NZ-Katalysatoren. Diese zusätzlichen Peaks entsprachen den Aromaten, Alkanen und Alkenverbindungen. Dies deutet darauf hin, dass der AA-NZ erwartungsgemäß bessere katalytische Eigenschaften als der TA-NZ hatte. Verschiedene Forscher haben über ähnliche Ergebnisse berichtet, wonach das aus PS hergestellte Flüssigöl überwiegend aus Aromaten bestand. Tekin et al. (2012) und Panda und Singh (2013) berichteten ebenfalls über das Vorhandensein von Aromaten mit einigen Alkanen und Alkenen bei der katalytischen Pyrolyse von PP. Kunwar et al. (2016) führten die thermische und katalytische Pyrolyse von PE durch und berichteten, dass das erzeugte Flüssigöl Alkane und Alkene als wichtigste funktionelle Gruppe enthält. Insgesamt lieferte die FT-IR-Analyse einen besseren Einblick in die chemische Zusammensetzung des Flüssigöls, das bei der katalytischen Pyrolyse verschiedener Kunststoffabfälle unter Verwendung modifizierter NZ-Katalysatoren hergestellt wurde, und bestätigte unsere GC-MS-Ergebnisse.
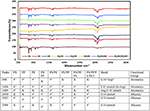
Abbildung 6. FT-IR-Analyse des durch katalytische Pyrolyse mit TA-NZ hergestellten flüssigen Öls.
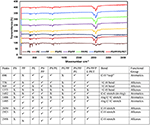
Abbildung 7. FT-IR-Analyse des aus der katalytischen Pyrolyse mit AA-NZ hergestellten Flüssigöls.
Potenzielle Anwendungen von Pyrolyseprodukten
Das aus der katalytischen Pyrolyse verschiedener Arten von Kunststoffen hergestellte Flüssigöl weist eine hohe Anzahl von aromatischen, olefinischen und naphthalinischen Verbindungen auf, die in Erdölprodukten vorkommen. Außerdem liegt der HHV des erzeugten Flüssigöls im Bereich von 41,7-44,2 MJ/kg (Tabelle 2), was dem Energiewert von herkömmlichem Diesel sehr nahe kommt. Der niedrigste HHV von 41,7 MJ/kg wurde bei Flüssigöl aus PS unter Verwendung des TA-NZ-Katalysators festgestellt, während der höchste HHV von 44,2 MJ/kg aus PS/PE/PP unter Verwendung des AA-NZ-Katalysators ermittelt wurde. Das aus verschiedenen Kunststoffabfällen hergestellte flüssige Pyrolyseöl hat also das Potenzial, als alternative Energiequelle genutzt zu werden. Nach Lee et al. (2015) und Rehan et al. (2016) ist die Erzeugung von Elektrizität mit flüssigem Pyrolyseöl in einem Dieselmotor möglich. Saptoadi und Pratama (2015) nutzten pyrolytisches Flüssigöl erfolgreich als Alternative in einem Kerosinkocher. Darüber hinaus können die erzeugten aromatischen Verbindungen als Rohmaterial für die Polymerisation in verschiedenen chemischen Industrien verwendet werden (Sarker und Rashid, 2013; Shah und Jan, 2015). Darüber hinaus nutzten verschiedene Forscher das gewonnene Flüssigöl als Kraftstoff für den Transport, nachdem es mit herkömmlichem Diesel in unterschiedlichen Verhältnissen gemischt wurde. Die Studien wurden durchgeführt, um das Potenzial des gewonnenen Flüssigöls in Bezug auf die Motorleistung und die Abgasemissionen von Fahrzeugen zu untersuchen. Nileshkumar et al. (2015) und Lee et al. (2015) berichteten, dass ein Mischungsverhältnis von 20:80 % zwischen pyrolytischem Flüssigöl und konventionellem Diesel zu ähnlichen Ergebnissen bei der Motorleistung führte wie konventioneller Diesel. Darüber hinaus waren die Abgasemissionen bei gleichem Mischungsverhältnis ebenfalls ähnlich, jedoch stiegen die Abgasemissionen mit der Erhöhung der Mischungsmenge an Pyrolyseöl (Frigo et al., 2014; Mukherjee und Thamotharan, 2014).
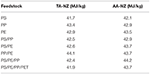
Tabelle 2. High Heating Values (HHV) von Pyrolyseöl aus verschiedenen Rohstoffen unter Verwendung von TA-NZ- und AA-NZ-Katalysatoren.
Der nach dem Pyrolyseprozess verbleibende Rückstand (Holzkohle) kann für verschiedene Umweltanwendungen genutzt werden. Mehrere Forscher aktivierten die Holzkohle durch Dampf und thermische Aktivierung (Lopez et al., 2009; Heras et al., 2014). Der Aktivierungsprozess vergrößerte die BET-Oberfläche und verringerte die Porengröße der Kohle (Lopez et al., 2009). Darüber hinaus hat Bernando (2011) die Kunststoffkohle mit Biomaterial aufgewertet und die Adsorption (3,6-22,2 mg/g) von Methylenblau-Farbstoff aus Abwasser durchgeführt. Miandad et al. (2018) nutzten die aus der Pyrolyse von PS-Kunststoffabfällen gewonnene Holzkohle zur Synthese eines neuartigen Kohlenstoff-Metall-Doppelschicht-Oxids (C/MnCuAl-LDOs) als Nano-Adsorptionsmittel für die Adsorption von Kongorot (CR) in Abwasser. Darüber hinaus kann die Holzkohle auch als Rohstoff für die Herstellung von Aktivkohle verwendet werden.
Grenzen der GC-MS-Analyse von Pyrolyseöl
Es gibt einige Einschränkungen bei der Durchführung einer genauen quantitativen Analyse der chemischen Komponenten in Pyrolyseöl mit GC-MS. In dieser Studie wurde der prozentuale Massenanteil der verschiedenen Chemikalien in den Ölproben verwendet, der auf der Grundlage der Peakflächen berechnet wurde, die mit einer Normalphasen-DP5-MS-Säule und einem FID identifiziert wurden. Die identifizierten Peaks wurden mit der NIST- und Massenbank-Spektrenbibliothek abgeglichen. Die Verbindungen wurden auf der Grundlage des Ähnlichkeitsindex (SI > 90%) ausgewählt. Ein weiterer Vergleich mit bekannten (CRM-)Standards ermöglichte die Bestätigung der identifizierten Verbindungen. Die verwendete Säule und die Detektoren waren nur auf Kohlenwasserstoffe beschränkt. In Wirklichkeit hat das Öl aus den meisten Kunststoffabfällen jedoch eine komplexe chemische Struktur und kann andere Gruppen nicht identifizierter Chemikalien wie schwefel-, stickstoff- und sauerstoffhaltige Kohlenwasserstoffe enthalten. Deshalb ist eine gründlichere und genauere qualitative chemische Analyse erforderlich, um die Chemie des Pyrolyseöls vollständig zu verstehen, wobei eine fortgeschrittene Kalibrierung und Standardisierung und verschiedene MS-Detektoren wie SCD und NCD sowie verschiedene GC-Säulen zum Einsatz kommen.
Das Potenzial und die Herausforderungen von Bioraffinerien auf Pyrolysebasis
Abfallbioraffinerien ziehen große Aufmerksamkeit auf sich, da sie eine Lösung für die Umwandlung von Hausmüll und anderen Biomasseabfällen in eine Reihe von Produkten wie Kraftstoffe, Strom, Wärme und andere wertvolle Chemikalien und Materialien darstellen. Je nach Art und Quelle der Abfälle können verschiedene Arten von Bioraffinerien entwickelt werden, z. B. eine Bioraffinerie für landwirtschaftliche Abfälle, eine Bioraffinerie für tierische Abfälle, eine Bioraffinerie für Abwässer, eine Bioraffinerie für Algen, eine Bioraffinerie für Kunststoffabfälle, eine Bioraffinerie für forstwirtschaftliche Abfälle, eine Bioraffinerie für Industrieabfälle, eine Bioraffinerie für Lebensmittelabfälle usw. (Gebreslassie et al., 2013; De Wild et al., 2014; Nizami et al., 2017a,b; Waqas et al., 2018). Diese Bioraffinerien können eine wichtige Rolle bei der Verringerung der abfallbedingten Umweltverschmutzung und der Treibhausgasemissionen spielen. Darüber hinaus generieren sie beträchtliche wirtschaftliche Vorteile und können dazu beitragen, eine Kreislaufwirtschaft in jedem Land zu erreichen.
Eine Bioraffinerie auf Pyrolysebasis kann entwickelt werden, um eine Reihe von Biomasseabfällen und Kunststoffabfällen zu behandeln, um flüssige und gasförmige Brennstoffe, Energie, Biokohle und andere höherwertige Chemikalien mithilfe eines integrierten Ansatzes zu erzeugen. Der integrierte Ansatz trägt dazu bei, bei minimaler Abfallproduktion einen maximalen wirtschaftlichen und ökologischen Nutzen zu erzielen. In Bioraffinerien auf Pyrolysebasis gibt es viele Herausforderungen und Verbesserungsmöglichkeiten, die angegangen und optimiert werden müssen, um einen maximalen Nutzen zu gewährleisten. Obwohl Pyrolyseöl mehr Energie enthält als Kohle und einige andere Brennstoffe, ist die Pyrolyse selbst ein energieintensiver Prozess, und das Ölprodukt benötigt mehr Energie für seine Raffination (Inman, 2012). Dies bedeutet, dass Pyrolyseöl in Bezug auf die THG-Emissionen möglicherweise nicht viel besser ist als herkömmlicher Diesel oder andere fossile Kraftstoffe, obwohl viele detaillierte Forschungsstudien zur Massen- und Energiebilanz über die gesamten Prozessgrenzen hinweg erforderlich sind, um dies zu bestätigen. Um diesen Energiebedarf zu überwinden, können fortschrittlichere Technologien entwickelt werden, bei denen erneuerbare Energien wie Solar- oder Wasserkraft mit Bioraffinerien auf Pyrolysebasis integriert werden, um maximale wirtschaftliche und ökologische Vorteile zu erzielen.
Die Verfügbarkeit von Kunststoff- und Biomasseabfällen als Ausgangsmaterial für Bioraffinerien auf Pyrolysebasis ist eine weitere große Herausforderung, da das Recycling derzeit nicht sehr effizient ist, insbesondere in den Entwicklungsländern. Die bei der Pyrolyse einiger Kunststoffabfälle wie PVC entstehenden Gase sind giftig, so dass die Technologie zur Behandlung der Pyrolyseemissionen weiter verfeinert werden muss, um einen maximalen Nutzen für die Umwelt zu erzielen. Das aus verschiedenen Kunststoffarten gewonnene Pyrolyseöl muss vor seiner Verwendung erheblich gereinigt werden, um die Umwelt so wenig wie möglich zu belasten. Der hohe Aromatengehalt des Pyrolyseöls ist gut und einige aromatische Verbindungen wie Benzol, Toluol und Styrol können raffiniert und auf einem bereits etablierten Markt verkauft werden. Einige der aromatischen Kohlenwasserstoffe sind jedoch als krebserregend bekannt und können die menschliche Gesundheit und die Umwelt ernsthaft schädigen. Weitere Aspekte zur Optimierung von Bioraffinerien auf Pyrolysebasis, wie z. B. neue, fortschrittliche Katalysatoren, einschließlich Nanokatalysatoren, müssen entwickelt und in Pyrolyseprozessen eingesetzt werden, um die Qualität und den Ertrag der Produkte zu erhöhen und den Gesamtprozess zu optimieren. Der Markt für Bioraffinerieprodukte auf Pyrolysebasis sollte geschaffen/erweitert werden, um weiteres Interesse und Finanzmittel anzuziehen, damit dieses Konzept praktischer und erfolgreicher wird. Ebenso ist es notwendig, weitere Forschungs- und Entwicklungsarbeiten durchzuführen, um das Bioraffineriekonzept zu bereichern und sein wahres Potenzial auszuschöpfen. Darüber hinaus ist es von entscheidender Bedeutung, in der Planungsphase eine detaillierte Bewertung der wirtschaftlichen und ökologischen Auswirkungen von Bioraffinerien mit Hilfe spezieller Instrumente wie der Lebenszyklusanalyse (LCA) durchzuführen. Die Ökobilanz kann die Umweltauswirkungen der Bioraffinerie und aller Produkte analysieren, indem sie detaillierte Energie- und Materialbilanzen aller Lebensphasen, einschließlich der Rohstoffgewinnung und -verarbeitung, der Herstellung, des Produktvertriebs, der Nutzung, der Wartung und der Entsorgung/Recycling, erstellt. Die Ergebnisse der LCA helfen, die Nachhaltigkeit von Bioraffinerien zu bestimmen, was für die Entscheidungsfindung von entscheidender Bedeutung ist.
Schlussfolgerungen
Die katalytische Pyrolyse ist eine vielversprechende Technik zur Umwandlung von Kunststoffabfällen in flüssiges Öl und andere Mehrwertprodukte unter Verwendung eines modifizierten natürlichen Zeolith-Katalysators (NZ). Die Modifizierung der NZ-Katalysatoren erfolgte durch eine neuartige thermische (TA) und saure (AA) Aktivierung, die ihre katalytischen Eigenschaften verbesserte. Bei der katalytischen Pyrolyse von PS wurde im Vergleich zu PP (40 und 54 %) und PE (40 und 42 %) mit den TA-NZ- bzw. AA-NZ-Katalysatoren das meiste Flüssigöl (70 und 60 %) gewonnen. Die chemische Zusammensetzung des Pyrolyseöls wurde mittels GC-MS analysiert, und es wurde festgestellt, dass der Großteil des flüssigen Öls einen hohen Gehalt an Aromaten mit einigen aliphatischen und anderen Kohlenwasserstoffverbindungen aufwies. Diese Ergebnisse wurden auch durch die FT-IR-Analyse bestätigt, die deutliche Peaks zeigte, die aromatischen und anderen funktionellen Kohlenwasserstoffgruppen entsprechen. Darüber hinaus wies das aus verschiedenen Arten von Kunststoffabfällen hergestellte Flüssigöl einen höheren Heizwert (HHV) im Bereich von 41,7-44,2 MJ/kg auf, ähnlich dem von herkömmlichem Diesel. Daher hat es das Potenzial, nach weiterer Behandlung und Raffinierung in verschiedenen Energie- und Transportanwendungen eingesetzt zu werden. Diese Studie ist ein Schritt zur Entwicklung von Bioraffinerien auf Pyrolysebasis. Bioraffinerien haben ein großes Potenzial, Abfälle in Energie und andere wertvolle Produkte umzuwandeln und könnten dazu beitragen, Kreislaufwirtschaften zu erreichen. Es gibt jedoch viele technische, betriebliche und sozioökonomische Herausforderungen, die überwunden werden müssen, um den maximalen wirtschaftlichen und ökologischen Nutzen von Bioraffinerien zu erreichen.
Datenverfügbarkeit
Alle für diese Studie generierten Datensätze sind im Manuskript und/oder den ergänzenden Dateien enthalten.
Beiträge der Autoren
RM führte die Pyrolyseexperimente durch und half beim Verfassen des Manuskripts. HK, JD, JG und AH haben die detaillierte Charakterisierung der Prozessprodukte durchgeführt. MR und ASA haben die Daten ausgewertet und Teile des Manuskripts verfasst. MAB, MR und A-SN haben das Manuskript korrigiert und bearbeitet. ASA und IMII haben das Projekt finanziell und technisch unterstützt.
Erklärung zu Interessenkonflikten
Die Autoren erklären, dass die Forschung in Abwesenheit von kommerziellen oder finanziellen Beziehungen durchgeführt wurde, die als potenzieller Interessenkonflikt ausgelegt werden könnten.
Danksagung
MR und A-SN danken dem Center of Excellence in Environmental Studies (CEES), King Abdulaziz University (KAU), Jeddah, KSA und dem Bildungsministerium, KSA für die finanzielle Unterstützung unter der Förderungsnummer 2/S/1438. Die Autoren danken auch dem Dekanat für wissenschaftliche Forschung (DSR) der KAU für die finanzielle und technische Unterstützung des CEES.
Adnan, A., Shah, J., and Jan, M. R. (2014). Untersuchungen zum Abbau von Polystyrol mit Hilfe von Katalysatoren auf Cu-Trägern. J. Anal. Appl. Pyrol. 109, 196-204. doi: 10.1016/j.jaap.2014.06.013
CrossRef Full Text | Google Scholar
Aguado, J., Sotelo, J. L., Serrano, D. P., Calles, J. A., and Escola, J. M. (1997). Katalytische Umwandlung von Polyolefinen in flüssige Kraftstoffe über MCM-41: Vergleich mit ZSM-5 und amorphem SiO2-Al2O3. Ener fuels 11, 1225-1231. doi: 10.1021/ef970055v
CrossRef Full Text | Google Scholar
Alexandra, L. C. (2012). Municipal Solid Waste: Turning a Problem Into Resourceewaste: The Challenges Facing Developing Countries, Urban Specialist. World Bank. 2-4 p.
Batool, M., Shah, A. T., Imran Din, M., and Li, B. (2016). Catalytic pyrolysis of low density polyethylene using cetyltrimethyl ammonium encapsulated monovacant keggin units and ZSM-5. J. Chem. 2016:2857162. doi: 10.1155/2016/2857162
CrossRef Full Text | Google Scholar
Bernando, M. (2011). „Physico-chemical characterization of chars produced in the co-pyrolysis of wastes and possible routes of valorization“, in Chemical Engineering (Lisboa: Universidade Nova de Lisboa), 27-36.
Bhaskar, T., Kaneko, J., Muto, A., Sakata, Y., Jakab, E., Matsui, T., et al. (2004). Untersuchungen zur Pyrolyse von PP/PE/PS/PVC/HIPS-Br-Kunststoffen im Gemisch mit PET und Dehalogenierung (Br, Cl) der flüssigen Produkte. J. Anal. Appl. Pyrolysis 72, 27-33. doi: 10.1016/j.jaap.2004.01.005
CrossRef Full Text | Google Scholar
Chandrasekaran, S. R., Kunwar, B., Moser, B. R., Rajagopalan, N., and Sharma, B. K. (2015). Catalytic thermal cracking of postconsumer waste plastics to fuels. 1. Kinetics and optimization. Energy Fuels 29, 6068-6077. doi: 10.1021/acs.energyfuels.5b01083
CrossRef Full Text | Google Scholar
Cullis, C. F., and Hirschler, M. M. (1981). The Combustion of Organic Polymers. Vol. 5. London: Oxford University Press.
Dawood, A., and Miura, K. (2002). Katalytische Pyrolyse von c-bestrahltem Polypropylen (PP) über HY-Zeolith zur Verbesserung der Reaktivität und der Produktselektivität. Polym. Degrad. Stab. 76, 45-52. doi: 10.1016/S0141-3910(01)00264-6
CrossRef Full Text | Google Scholar
De Wild, P. J., Huijgen, W. J., and Gosselink, R. J. (2014). Ligninpyrolyse für rentable lignozellulosehaltige Bioraffinerien. Biofuels Bioprod. Biorefining 8, 645-657. doi: 10.1002/bbb.1474
CrossRef Full Text | Google Scholar
Demirbas, A. (2004). Pyrolyse von kommunalen Kunststoffabfällen zur Rückgewinnung von Kohlenwasserstoffen aus dem Benzinbereich. J. Anal. Appl. Pyrolysis 72, 97-102. doi: 10.1016/j.jaap.2004.03.001
CrossRef Full Text | Google Scholar
Dimitrov, N., Krehula, L. K., Siročić, A. P., and Hrnjak-Murgić, Z. (2013). Analyse von Produkten aus recycelten PET-Flaschen durch Pyrolyse-Gaschromatographie. Polym. Degrad. Stab. 98, 972-979. doi: 10.1016/j.polymdegradstab.2013.02.013
CrossRef Full Text | Google Scholar
Dziecioł, M., and Trzeszczynski, J. (2000). Flüchtige Produkte des thermischen Abbaus von Poly(ethylenterephthalat) in Stickstoffatmosphäre. J. Appl. Polym. Sci. 77, 1894-1901. doi: 10.1002/1097-4628(20000829)77:9<1894::AID-APP5>3.0.CO;2-Y
CrossRef Full Text | Google Scholar
Frigo, S., Seggiani, M., Puccini, M., and Vitolo, S. (2014). Herstellung von Flüssigkraftstoff aus der Pyrolyse von Altreifen und dessen Nutzung in einem Dieselmotor. Fuel 116, 399-408. doi: 10.1016/j.fuel.2013.08.044
CrossRef Full Text | Google Scholar
Gaca, P., Drzewiecka, M., Kaleta, W., Kozubek, H., and Nowinska, K. (2008). Katalytischer Abbau von Polyethylen über mesoporösem Molekularsieb MCM-41, modifiziert mit Heteropolyverbindungen. Polish J. Environ. Stud. 17, 25-35.
Google Scholar
Gandidi, I. M., Susila, M. D., Mustofa, A., and Pambudi, N. A. (2018). Thermal-Catalytic cracking of real MSW into Bio-Crude Oil. J. Energy Inst. 91, 304-310. doi: 10.1016/j.joei.2016.11.005
CrossRef Full Text | Google Scholar
Gebreslassie, B. H., Slivinsky, M., Wang, B., and You, F. (2013). Lebenszyklusoptimierung für nachhaltiges Design und Betrieb einer Kohlenwasserstoff-Bioraffinerie durch Schnellpyrolyse, Hydrotreating und Hydrocracking. Comput. Chem. Eng. 50, 71-91. doi: 10.1016/j.compchemeng.2012.10.013
CrossRef Full Text | Google Scholar
Heras, F., Jimenez-Cordero, D., Gilarranz, M. A., Alonso-Morales, N., and Rodriguez, J. J. (2014). Aktivierung von Altreifenkohle durch zyklische Flüssigphasenoxidation. Fuel Process. Technol. 127, 157-162. doi: 10.1016/j.fuproc.2014.06.018
CrossRef Full Text | Google Scholar
Inman, M. (2012). Cooking up fuel. Nat. Clim. Change 2, 218-220. doi: 10.1038/nclimate1466
CrossRef Full Text | Google Scholar
Jung, S. H., Cho, M. H., Kang, B. S., and Kim, J. S. (2010). Pyrolyse einer Fraktion von Abfall-Polypropylen und Polyethylen zur Rückgewinnung von BTX-Aromaten unter Verwendung eines Wirbelschichtreaktors. Fuel Process. Technol. 91, 277-284. doi: 10.1016/j.fuproc.2009.10.009
CrossRef Full Text | Google Scholar
Kim, H. S., Kim, S., Kim, H. J., and Yang, H. S. (2006). Thermische Eigenschaften von mit Biomehl gefüllten Polyolefin-Verbundwerkstoffen mit unterschiedlichem Kompatibilisierungsmitteltyp und -gehalt. Thermochim. Acta 451, 181-188. doi: 10.1016/j.tca.2006.09.013
CrossRef Full Text | Google Scholar
Kim, J. R., Yoon, J. H., and Park, D. W. (2002). Katalytisches Recycling einer Mischung aus Polypropylen und Polystyrol. Polym. Degrad. Stab. 76, 61-67. doi: 10.1016/S0141-3910(01)00266-X
CrossRef Full Text | Google Scholar
Kiran, N., Ekinci, E., and Snape, C. E. (2000). Wiederverwertung von Kunststoffabfällen durch Pyrolyse. Resour. Conserv. Recycl. 29, 273-283. doi: 10.1016/S0921-3449(00)00052-5
CrossRef Full Text | Google Scholar
Kunwar, B., Moser, B. R., Chandrasekaran, S. R., Rajagopalan, N., and Sharma, B. K. (2016). Catalytic and thermal depolymerization of low value post-consumer high density polyethylene plastic. Energy 111, 884-892. doi: 10.1016/j.energy.2016.06.024
CrossRef Full Text | Google Scholar
Lecomte, H. A., and Liggat, J. J. (2006). Degradationsmechanismus von Diethylenglykol-Einheiten in einem Terephthalat-Polymer. Polym. Degrad. Stab. 91, 681-689. doi: 10.1016/j.polymdegradstab.2005.05.028
CrossRef Full Text | Google Scholar
Lee, K. H. (2012). Effects of the types of zeolites on catalytic upgrading of pyrolysis wax oil. J. Anal. Appl. Pyrol. 94, 209-214. doi: 10.1016/j.jaap.2011.12.015
CrossRef Full Text | Google Scholar
Lee, S., Yoshida, K., and Yoshikawa, K. (2015). Application of waste plastic pyrolysis oil in a direct injection diesel engine: For a small scale non-grid electrification. Energy Environ. Res. 5:18. doi: 10.5539/eer.v5n1p18
CrossRef Full Text
Lee, S. Y., Yoon, J. H., Kim, J. R., and Park, D. W. (2001). Katalytischer Abbau von Polystyrol über natürlichem Klinoptilolith-Zeolith. Polym. Degrad. Stab. 74, 297-305. doi: 10.1016/S0141-3910(01)00162-8
CrossRef Full Text | Google Scholar
Lin, Y. H., Yang, M. H., Yeh, T. F., and Ger, M. D. (2004). Katalytischer Abbau von Polyethylen hoher Dichte über mesoporösen und mikroporösen Katalysatoren in einem Wirbelschichtreaktor. Polym. Degrad. Stab. 86, 121-128. doi: 10.1016/j.polymdegradstab.2004.02.015
CrossRef Full Text | Google Scholar
Lopez, A., Marco d, I., Caballero, B. M., Laresgoiti, M. F., Adrados, A., and Torres, A. (2011). Pyrolyse von kommunalen Kunststoffabfällen II: Einfluss der Zusammensetzung des Rohmaterials unter katalytischen Bedingungen. Waste Manag. 31, 1973-1983. doi: 10.1016/j.wasman.2011.05.021
CrossRef Full Text | Google Scholar
Lopez, G., Olazar, M., Artetxe, M., Amutio, M., Elordi, G., and Bilbao, J. (2009). Dampfaktivierung von pyrolytischer Reifenkohle bei verschiedenen Temperaturen. J. Anal. Appl. Pyrol. 85, 539-543. doi: 10.1016/j.jaap.2008.11.002
CrossRef Full Text | Google Scholar
Ma, C., Yu, J., Wang, B., Song, Z., Xiang, J., Hu, S., et al. (2017). Katalytische Pyrolyse von flammgeschütztem hochschlagzähem Polystyrol über verschiedenen festen sauren Katalysatoren. Fuel Process. Technol. 155, 32-41. doi: 10.1016/j.fuproc.2016.01.018
CrossRef Full Text | Google Scholar
Marcilla, A., Beltrán, M. I., Hernández, F., and Navarro, R. (2004). HZSM5 und HUSY Deaktivierung während der katalytischen Pyrolyse von Polyethylen. Appl. Catal. A Gen. 278, 37-43. doi: 10.1016/j.apcata.2004.09.023
CrossRef Full Text | Google Scholar
McNeill, I. C., and Bounekhel, M. (1991). Thermal degradation studies of terephthalate polyesters: 1. Poly (alkylene terephthalates). Polymer Degrad. Stab. 34, 187-204. doi: 10.1016/0141-3910(91)90119-C
CrossRef Full Text | Google Scholar
McNeill, I. C., Zulfiqar, M., and Kousar, T. (1990). Eine detaillierte Untersuchung der Produkte des thermischen Abbaus von Polystyrol. Polym. Degrad. Stab. 28, 131-151. doi: 10.1016/0141-3910(90)90002-O
CrossRef Full Text | Google Scholar
Miandad, R., Barakat, M. A., Aburiazaiza, A. S., Rehan, M., Ismail, I. M. I., and Nizami, A. S. (2017b). Auswirkung von Kunststoffabfallarten auf flüssiges Pyrolyseöl. Int. Biodeterior. Biodegrad. 119, 239-252. doi: 10.1016/j.ibiod.2016.09.017
CrossRef Full Text | Google Scholar
Miandad, R., Barakat, M. A., Aburiazaiza, A. S., Rehan, M., and Nizami, A. S. (2016a). Katalytische Pyrolyse von Kunststoffabfällen: ein Überblick. Process Safety Environ. Protect. 102, 822-838. doi: 10.1016/j.psep.2016.06.022
CrossRef Full Text | Google Scholar
Miandad, R., Barakat, M. A., Rehan, M., Aburiazaiza, A. S., Ismail, I. M. I., and Nizami, A. S. (2017a). Plastic waste to liquid oil through catalytic pyrolysis using natural and synthetic zeolite catalysts. Waste Manag. 69, 66-78. doi: 10.1016/j.wasman.2017.08.032
PubMed Abstract | CrossRef Full Text | Google Scholar
Miandad, R., Kumar, R., Barakat, M. A., Basheer, C., Aburiazaiza, A. S., Nizami, A. S., et al. (2018). Ungenutzte Umwandlung von Kunststoffabfall-Holzkohle in Kohlenstoff-Metall-LDOs für die Adsorption von Kongorot. J Colloid Interface Sci. 511, 402-410. doi: 10.1016/j.jcis.2017.10.029
PubMed Abstract | CrossRef Full Text | Google Scholar
Miandad, R., Nizami, A. S., Rehan, M., Barakat, M. A., Khan, M. I., Mustafa, A., et al. (2016b). Einfluss von Temperatur und Reaktionszeit auf die Umwandlung von Polystyrolabfällen in flüssiges Pyrolyseöl. Waste Manag. 58, 250-259. doi: 10.1016/j.wasman.2016.09.023
PubMed Abstract | CrossRef Full Text | Google Scholar
Miandad, R., Rehan, M., Nizami, A. S., Barakat, M. A. E. F., and Ismail, I. M. (2016c). „The energy and value- added products from pyrolysis of waste plastics,“ in Recycling of Solid Waste for Biofuels and Bio- Chemicals, eds O. P. Karthikeyan, K. H. Subramanian, and S. Muthu (Singapore: Springer), 333-355.
Google Scholar
Miskolczi, N., Bartha, L., and Deak, G. (2006). Thermischer Abbau von Polyethylen und Polystyrol aus der Verpackungsindustrie über verschiedene Katalysatoren zu brennstoffähnlichen Ausgangsstoffen. Polym. Degrad. Stab. 91, 517-526. doi: 10.1016/j.polymdegradstab.2005.01.056
CrossRef Full Text | Google Scholar
Mukherjee, M. K., and Thamotharan, P. C. (2014). Performance and emission test of several blends of waste plastic oil with diesel and ethanol on four stroke twin cylinder diesel engine. IOSR J. Mech. Civil Eng. 11, 2278-1684. doi: 10.9790/1684-11214751
CrossRef Full Text
Nileshkumar, K. D., Jani, R. J., Patel, T. M., and Rathod, G. P. (2015). Auswirkungen des Mischungsverhältnisses von Kunststoffpyrolyseöl und Dieselkraftstoff auf die Leistung eines Einzylinder-CI-Motors. Int. J. Sci. Technol. Eng. 1, 2349-2784.
Google Scholar
Nizami, A. S., Ouda, O. K. M., Rehan, M., El-Maghraby, A. M. O., Gardy, J., Hassanpour, A., et al. (2016). Das Potenzial von saudi-arabischen Naturzeolithen in Technologien zur Energierückgewinnung. Energy 108, 162-171. doi: 10.1016/j.energy.2015.07.030
CrossRef Full Text | Google Scholar
Nizami, A. S., Rehan, M., Waqas, M., Naqvi, M., Ouda, O. K. M., Shahzad, K., et al. (2017a). Waste biorefineries: enabling circular economies in developing countries. Bioresour. Technol. 241, 1101-1117. doi: 10.1016/j.biortech.2017.05.097
PubMed Abstract | CrossRef Full Text | Google Scholar
Nizami, A. S., Shahzad, K., Rehan, M., Ouda, O. K. M., Khan, M. Z., Ismail, I. M. I., et al. (2017b). Entwicklung einer Abfall-Bioraffinerie in Makkah: ein Weg zur Umwandlung von Siedlungsabfällen in erneuerbare Energie. Appl. Energy. 186, 189-196. doi: 10.1016/j.apenergy.2016.04.116
CrossRef Full Text | Google Scholar
Obali, Z., Sezgi, N. A., and Doğu, T. (2012). Katalytischer Abbau von Polypropylen über mit Tonerde beladenen mesoporösen Katalysatoren. Chem. Eng. J. 207, 421-425. doi: 10.1016/j.cej.2012.06.146
CrossRef Full Text | Google Scholar
Ogawa, T., Kuroki, T., Ide, S., and Ikemura, T. (1982). Recovery of indan derivatives from polystyrene waste. J. Appl. Polym. Sci. 27, 857-869. doi: 10.1002/app.1982.070270306
CrossRef Full Text | Google Scholar
Panda, A. K., and Singh, R. K. (2013). Experimentelle Optimierung des Prozesses für den thermokatalytischen Abbau von Abfall-Polypropylen zu flüssigem Brennstoff. Adv. Energy Eng. 1, 74-84.
Google Scholar
Peterson, J. D., Vyazovkin, S., and Wight, C. A. (2001). Kinetik des thermischen und thermo-oxidativen Abbaus von Polystyrol, Polyethylen und Poly(propylen). Macromol. Chem. Phys. 202, 775-784. doi: 10.1002/1521-3935(20010301)202:6<775::AID-MACP775>3.0.CO;2-G
CrossRef Full Text | Google Scholar
Ramli, M. R., Othman, M. B. H., Arifin, A., and Ahmad, Z. (2011). Vernetzungsnetzwerk von Polydimethylsiloxan über Additions- und Kondensationsmechanismen (RTV). Teil I: Synthese und thermische Eigenschaften. Polym. Degrad. Stab. 96, 2064-2070. doi: 10.1016/j.polymdegradstab.2011.10.001
CrossRef Full Text | Google Scholar
Ratnasari, D. K., Nahil, M. A., and Williams, P. T. (2017). Katalytische Pyrolyse von Kunststoffabfällen mittels Stufenkatalyse zur Herstellung von Kohlenwasserstoffölen im Benzinbereich. J. Anal. Appl. Pyrolysis 124, 631-637. doi: 10.1016/j.jaap.2016.12.027
CrossRef Full Text | Google Scholar
Rehan, M., Miandad, R., Barakat, M. A., Ismail, I. M. I., Almeelbi, T., Gardy, J., et al. (2017). Wirkung von Zeolith-Katalysatoren auf die Pyrolyse von flüssigem Öl. Int. Biodeterior. Biodegrad. 119, 162-175. doi: 10.1016/j.ibiod.2016.11.015
CrossRef Full Text | Google Scholar
Rehan, M., Nizami, A. S., Shahzad, K., Ouda, O. K. M., Ismail, I. M. I., Almeelbi, T., et al. (2016). Pyrolytischer Flüssigbrennstoff: eine Quelle für erneuerbare Energie in Makkah. Energy Sources A 38, 2598-2603. doi: 10.1080/15567036.2016.1153753
CrossRef Full Text | Google Scholar
Rizzarelli, P., Rapisarda, M., Perna, S., Mirabella, E. F., La Carta, S., Puglisi, C., et al. (2016). Bestimmung von Polyethylen in biologisch abbaubaren Polymermischungen und in kompostierbaren Tragetaschen mittels Py-GC/MS und TGA. J. Anal. Appl. Pyrolysis 117,72-81. doi: 10.1016/j.jaap.2015.12.014
CrossRef Full Text | Google Scholar
Saptoadi, H., and Pratama, N. N. (2015). Utilization of plastics waste oil as partial substitute for kerosene in pressurized cookstoves. Int. J. Environ. Sci. Dev. 6, 363-368. doi: 10.7763/IJESD.2015.V6.619
CrossRef Full Text | Google Scholar
Sarker, M., and Rashid, M. M. (2013). Waste plastics mixture of polystyrene and polypropylene into light grade fuel using Fe2O3 catalyst. Int. J. Renew. Energy Technol. Res. 2, 17-28.
Google Scholar
Seo, Y. H., Lee, K. H., and Shin, D. H. (2003). Untersuchung des katalytischen Abbaus von Polyethylen hoher Dichte durch Analyse des Kohlenwasserstoffgruppentyps. J. Anal. Appl. Pyrol. 70, 383-398. doi: 10.1016/S0165-2370(02)00186-9
CrossRef Full Text | Google Scholar
Serrano, D. P., Aguado, J., and Escola, J. M. (2000). Katalytische Umwandlung von Polystyrol über HMCM-41, HZSM-5 und amorphes SiO2-Al2O3: Vergleich mit thermischem Cracken. Appl. Catal. B:Environ. 25, 181-189. doi: 10.1016/S0926-3373(99)00130-7
CrossRef Full Text | Google Scholar
Serrano, D. P., Aguado, J., and Escola, J. M. (2012). Entwicklung fortschrittlicher Katalysatoren für die Umwandlung von polyolefinischen Kunststoffabfällen in Kraftstoffe und Chemikalien. ACS Catal. 2, 1924-1941. doi: 10.1021/cs3003403
CrossRef Full Text | Google Scholar
Shah, J., and Jan, M. R. (2015). Einfluss von Polyethylenterephthalat auf die katalytische Pyrolyse von Polystyrol: Investigation of the liquid products. J. Taiwan Inst. Chem. Eng. 51, 96-102. doi: 10.1016/j.jtice.2015.01.015
CrossRef Full Text | Google Scholar
Siddiqui, M. N., and Redhwi, H. H. (2009). Pyrolyse von Mischkunststoffen zur Gewinnung nützlicher Produkte. Fuel Process. Technol. 90, 545-552. doi: 10.1016/j.fuproc.2009.01.003
CrossRef Full Text | Google Scholar
Sriningsih, W., Saerodji, M. G., Trisunaryanti, W., Armunanto, R., and Falah, I. I. (2014). Kraftstoffherstellung aus LDPE-Kunststoffabfällen über natürliche Zeolithe mit Ni, Ni-Mo, Co und Co-Mo Metallen. Proc. Environ. Sci. 20, 215-224. doi: 10.1016/j.proenv.2014.03.028
CrossRef Full Text | Google Scholar
Syamsiro, M., Cheng, S., Hu, W., Saptoadi, H., Pratama, N. N., Trisunaryanti, W., et al. (2014). Flüssige und gasförmige Brennstoffe aus Kunststoffabfällen durch sequenzielle Pyrolyse und katalytische Reformierungsprozesse über indonesischen Naturzeolith-Katalysatoren. Waste Technol. 2, 44-51. doi: 10.12777/wastech.2.2.44-51
CrossRef Full Text | Google Scholar
Tekin, K., Akalin, M. K., Kadi, C., and Karagöz, S. (2012). Catalytic degradation of waste polypropylene by pyrolysis. J. Energy Ins. 85, 150-155. doi: 10.1179/1743967112Z.00000000029
CrossRef Full Text | Google Scholar
Thilakaratne, R., Tessonnier, J. P., and Brown, R. C. (2016). Umwandlung von Methoxy- und Hydroxylfunktionalitäten von phenolischen Monomeren über Zeolithe. Green Chem. 18, 2231-2239. doi: 10.1039/c5gc02548f
CrossRef Full Text | Google Scholar
Uemichi, Y., Hattori, M., Itoh, T., Nakamura, J., and Sugioka, M. (1998). Deaktivierungsverhalten von Zeolith- und Kieselerde-Tonerde-Katalysatoren beim Abbau von Polyethylen. Ind. Eng. Chem. Res. 37, 867-872. doi: 10.1021/ie970605c
CrossRef Full Text | Google Scholar
Uemichi, Y., Nakamura, J., Itoh, T., Sugioka, M., Garforth, A. A., and Dwyer, J. (1999). Umwandlung von Polyethylen in benzinähnliche Kraftstoffe durch zweistufigen katalytischen Abbau unter Verwendung von Silica-Alumina und HZSM-5 Zeolith. Ind. Eng. Chem. Res. 38, 385-390. doi: 10.1021/ie980341+
CrossRef Full Text | Google Scholar
Ukei, H., Hirose, T., Horikawa, S., Takai, Y., Taka, M., Azuma, N., et al. (2000). Katalytischer Abbau von Polystyrol zu Styrol und Entwurf eines wiederverwertbaren Polystyrols mit dispergierten Katalysatoren. Catal. Today 62, 67-75. doi: 10.1016/S0920-5861(00)00409-0
CrossRef Full Text | Google Scholar
Waqas, M., Rehan, M., Aburiazaiza, A. S., and Nizami, A. S. (2018). „Chapter 17-Wastewater Biorefinery based on the microbial electrolysis cell: opportunities and challenges,“ in Progress and Recent Trends in Microbial Fuel Cells, eds K. Dutta and P. Kundu (New York, NY: Elsevier Inc.), 347-374. doi: 10.1016/B978-0-444-64017-8.00017-8
CrossRef Full Text
Williams, P. T. (2006). „Ausbeute und Zusammensetzung von Gasen und Ölen/Wachsen aus der rohstofflichen Verwertung von Kunststoffabfällen“. In Feeds Tock Recycling and Pyrolysis of Waste Plastics: Converting Waste Plastics into Diesel and Other Fuels, eds J. Scheirs and W. Kaminsky (West Sussex: John Wiley & Sons Press), 285-309.
Google Scholar
Wu, C., and Williams, P. T. (2010). Pyrolyse-Vergasung von Kunststoffen, gemischten Kunststoffen und Kunststoffabfällen aus der realen Welt mit und ohne Ni-Mg-Al-Katalysator. Fuel 89, 3022-3032. doi: 10.1016/j.fuel.2010.05.032
CrossRef Full Text | Google Scholar
Wu, J., Chen, T., Luo, X., Han, D., Wang, Z., and Wu, J. (2014). TG/FTIR-Analyse zum Co-Pyrolyseverhalten von PE, PVC und PS. Waste Manag. 34, 676-682. doi: 10.1016/j.wasman.2013.12.005
PubMed Abstract | CrossRef Full Text | Google Scholar
Xue, Y., Johnston, P., and Bai, X. (2017). Einfluss von Katalysatorkontaktmodus und Gasatmosphäre bei der katalytischen Pyrolyse von Kunststoffabfällen. Energy Conv. Manag. 142, 441-451. doi: 10.1016/j.enconman.2017.03.071
CrossRef Full Text | Google Scholar
Yoshioka, T., Grause, G., Eger, C., Kaminsky, W., and Okuwaki, A. (2004). Pyrolyse von Poly(ethylenterephthalat) in einer Wirbelschichtanlage. Polym. Degrad. Stab. 86, 499-504. doi: 10.1016/j.polymdegradstab.2004.06.001
CrossRef Full Text | Google Scholar
Zeaiter, J. (2014). Eine Prozessstudie zur Pyrolyse von Altpolyethylen. Fuel 133, 276-282. doi: 10.1016/j.fuel.2014.05.028
CrossRef Full Text | Google Scholar